MPSとMRPの違いとは?活用方法も解説
2025.02.07A0 生産管理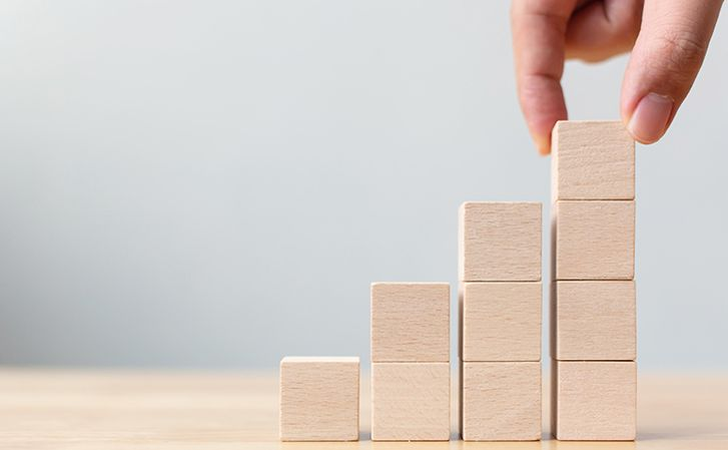
製造業における効率的な生産計画は、企業の競争力を左右します。本記事では、基準日程生産計画(MPS)と資材所要計画(MRP)の基本概念から、その違い、導入によるメリット、そして効果的な活用方法までを詳しく解説します。
【目次】
■生産計画の用語 MPSについて
■生産計画の用語 MRPについて
■MRP補足 MRP2について
■MPSとMRPの違いを整理する
・MPSとMRPの違い
・MPSとMRPの連携の重要性
■MPS導入によるメリット
・生産負荷の平準化
・需要変動への柔軟な対応
・生産リソースの有効活用
・在庫の適正化
■MRP導入によるメリット
・在庫管理・生産計画の最適化
・コスト削減とキャッシュフローの改善
・部門間の情報共有の強化
■MPSとMRPを活用した効率的な生産計画の立て方
・大日程計画(長期計画)
・中日程計画(中期計画)
・小日程計画(短期計画)
・MRPを使った資材の調達計画
■おわりに
生産計画の用語 MPSについて
MPSとは、「Master Production Schedule」の略称です。日本語でいうと、「基準日程生産計画」となります。
MPSは生産活動において「いつまでに」「いくつ」の製品を生産すべきかを定めるものです。各製品の納期と数量を具体的に決め、安定した供給体制の維持に欠かせません。
受注したすべての注文に対して納期通りの対応が常に可能であれば、MPS(基準日程生産計画)の導入は不要です。しかし、現実には生産能力には限りがあり、特に受注数が多すぎる場合には、すべてを同時に生産することが困難です。
このため、MPSは限られた生産リソースの中で受注を効率的にさばき、納期遵守を目指すために欠かせない計画手法とされています。
MPS(基準日程生産計画)を立てることで、以下のような問題が解決できます。
- 受注数が多すぎて、一括で生産を行うことができない
- 生産負荷を平準化する必要がある
- 安全在庫を確保しておかなければならない
- 先行生産をしておきたい
受注と生産の間での様々な問題を解決するために、MPS(基準日程生産計画)は活用されています。
生産計画の用語 MRPについて

MRPは「Material Requirement Planning」の略称で、日本語では「資材所要計画」と呼ばれます。1960年代に考案され、製造業の生産管理において広く採用され続けている手法です。
MRPはMPS(基準日程生産計画)を基にして在庫引当てを行います。MPSによって「いつまでに」「いくつ」の製品を生産するかが決定され、その情報を基にMRPが具体的な生産日や生産数量、資材の必要日や必要数量を計算します。
従来は、過去の使用分を補充する方法が主流でしたが、MRPでは今後の需要を予測して必要な資材を計算するため、過剰在庫や欠品のリスクが減少するのがポイントです。MRPを導入することで在庫管理の精度が向上し、資材管理の効率化につながります。
MRP補足 MRP2について
MRPの進化形として「MRP2」という手法があります。MRPは在庫管理に特化した手法でしたが、MRP2は資材調達や生産計画に加えて、生産に関わるヒト、モノ、カネの管理も含めた総合的なリソース管理を目指しています。
製造業では、過剰在庫が資金の固定化や保管コストの増加を招き、キャッシュフローの悪化につながるという課題がありました。MRP2は、こうした課題への対応策として広く採用されています。
MPSとMRPの違いを整理する
ここでは、MPSとMRPの違いや両者を連携する重要性について分かりやすく解説します。
MPSとMRPの違い
MPS(基準日程生産計画)とMRP(資材所要計画)は、製造業の生産計画を支える重要なシステムです。それぞれ役割が異なります。
まず、MPSの役割は、製品ごとの生産量や生産タイミングを決めることで、生産工程全体にかかる負荷を管理することです。今後数か月の需要予測に基づき、製品Aをどれだけ生産するかを計画することで、生産ラインの効率と安定性を確保します。
一方、MRPは、MPSで決められた生産計画を実行するために必要な材料や部品の調達を管理します。具体的には、製品Aの生産に必要な部品Bをどの時点でどれだけ手配するかを決定し、資材の供給を円滑に進めるのが目的です。
このように、MPSは生産スケジュール全体の管理に焦点を当て、MRPはその計画を支える資材調達に特化している点が大きな違いです。しかし、どちらのシステムも無駄な在庫を防ぎ、生産効率を高めるために活用されている点は共通しています。
MPS(基準日程生産計画) | MRP(資材所要計画) | |
---|---|---|
主な役割 | 生産量・生産タイミングの決定 | 必要な材料や部品の調達計画 |
管理対象 | 生産スケジュール全体 | 資材の供給と在庫管理 |
対象範囲 | 生産ライン全体の効率と安定性 | 生産計画に基づく部品・材料の確保 |
使用目的 | 生産負荷の管理、需要予測に基づく計画 | 生産計画に必要な資材の適切な手配 |
MPSとMRPの連携の重要性
MPSとMRPの連携は、生産活動の効率化と安定において非常に重要です。MPSで正確な生産スケジュールを設定することで、MRPはその計画に基づき、適切なタイミングで必要な資材を確保できます。この連携が上手く機能すれば、資材の過不足が解消され、生産ラインがスムーズに進みます。その結果、コストの削減や納期の確保にもつながるでしょう。
MPSの精度が高まると、MRPも効率的に機能し、過剰在庫や資材不足といったリスクが減少します。余分な在庫コストを抑えながら、必要なタイミングで必要な量の資材を確保でき、生産活動の安定性が保たれるでしょう。
このように、MPSとMRPの連携は、生産活動全体のパフォーマンス向上に欠かせない要素です。
MPS導入によるメリット
MPSの導入により、企業は効率的な生産計画が立てやすくなり、リソースの無駄が減ります。以下で、MPSがもたらす具体的なメリットを解説します。
生産負荷の平準化
MPSを使用すると、一定期間内で均等な生産計画を立てることが可能です。繁忙期と閑散期による極端な生産の波を抑え、不均衡を解消することで、作業員や設備に過度な負荷がかかりません。たとえば、月の初めに急激に生産量が増え、月末に減るといった生産の偏りがある場合でも、MPSを活用して生産を均等に分散させることで、生産負荷を平準化できます。
需要変動への柔軟な対応
市場環境が変化して需要予測が外れることもあるでしょう。ですが、MPSを導入することで需要の変動に対して柔軟に対応する体制を整えられます。MPSは需要予測に基づいて生産計画を立てるため、あらかじめ設定された期間ごとに計画を見直します。そのため、急な需要変更があってもそれを踏まえて計画を立て直しやすいのです。
たとえば、飲料メーカーでは、夏に冷たい飲料の大口注文が予想外に増えることがあります。MPSを活用することで、事前に需要予測とリソース配分を調整しているため、急な需要変更にも柔軟に対応が可能です。
生産リソースの有効活用
MPSを導入することで、労働力や設備を効率的に管理し、生産リソースの無駄を減らせます。稼働していない時間を把握して別の生産に充てることで、リソースを有効に活用できるでしょう。また、生産コストの削減にもつながります。
たとえば、飲料メーカーが清涼飲料水の生産が一時的に停止しているラインを利用して、その時間を別の飲料の生産に充てることで、設備の稼働率を高めるといったことが挙げられます。MPSで計画をたてているからこそ、無駄なくリソースを使えるのです。
在庫の適正化
MPSを活用することで、需要予測に基づいた適切なタイミングでの生産が可能となり、過剰な在庫を持つことなく必要な量を供給できます。また、リードタイムを考慮した効率的な補充により、在庫の回転率が向上し、保管コストの削減や滞留リスクも軽減。こうした理由により、在庫の適正化が行えるのがメリットです。
MRP導入によるメリット
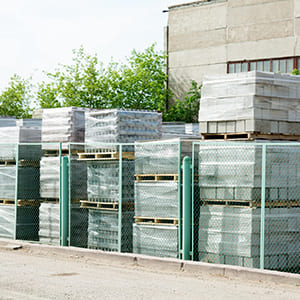
MRP(資材所要計画)を導入すると、資材を適切なタイミングで調達でき、在庫過剰や不足を防ぎます。以下では、MRP導入のメリットを紹介します。
在庫管理・生産計画の最適化
MRPは在庫データや需要予測、リードタイムを基に、資材の量と調達タイミングを管理する手法です。過剰在庫や資材不足のリスクを抑え、適切な在庫水準を維持しやすくなります。また、資材手配と生産スケジュールを一元化するため、部門間での情報共有もスムーズになり、生産中断や納期遅延のリスクが軽減します。MRPにより、在庫管理と生産計画を効率的に行う体制が整うでしょう。
コスト削減とキャッシュフローの改善
MRPの導入により、無駄な資材調達や過剰在庫が抑えられれば、保管や廃棄コストが削減できます。必要な資材を適切なタイミングで調達できる仕組みにより、在庫に資金が固定されることも防げるため、キャッシュフローも安定するでしょう。その分、効率的な資金運用が可能となり、他の分野への投資も行いやすくなります。
部門間の情報共有の強化
MRPを導入すると、生産部門や購買部門が共通のデータベースからリアルタイムで在庫や調達状況を確認できます。担当者に話を聞く手間がかからず、情報を即座に取り出せるのがメリットです。コミュニケーションコストを削減することで、従業員一人ひとりの時間を有効活用できるようになります。また、オープンに情報をやり取りできるため、A部門は知っているがB部門は知らない、といった格差も是正でき、関係性を強化できるでしょう。
MPSとMRPを活用した効率的な生産計画の立て方
生産計画は「大日程計画」「中日程計画」「小日程計画」の段階で管理され、長期から日々の資材調達までを調整します。MPSで全体方針を決め、MRPで具体的な資材調達を進めるのが特徴です。以下では、それぞれの計画の流れを詳しく説明します。
大日程計画(長期計画)
大日程計画は、将来の需要予測に基づき、長期的な生産枠組みを決める段階です。通常3か月から1年のスパンで策定され、生産量や設備稼働、必要な労働力を見通し、リソース確保や戦略立案を行います。
たとえば、製品Aの年間生産量を見据え、設備投資や人員配置を検討することが大日程計画の例です。具体的な製造スケジュールではなく、設備や人員の準備・調整と言った内容が含まれます。厳密なスケジュールではないため、ある程度の柔軟性があるのも特徴です。
中日程計画(中期計画)
中日程計画は、MPSを基に実際の需要や受注に応じて月単位や週単位で生産計画を立てる段階です。通常1〜3か月の期間を対象とし、製品ごとに生産量を決定します。
たとえば、今月は製品Aを何個、来月は製品Bを何個生産するかを決め、週ごとの生産量や稼働スケジュールを調整します。この段階では、長期計画を基にしつつ、現実の需要に合わせて柔軟に計画を修正することが重要です。中日程計画では、MPSをもとに具体的な数量やスケジュールをより詳細に決定します。
小日程計画(短期計画)
小日程計画は、MRPを活用して日単位で生産スケジュールや資材調達を管理する段階です。対象期間は1週間から1か月と短期で、各生産ラインの稼働や部品の入荷タイミングを調整し、効率的に生産を行います。
たとえば、1週間のうちにどの生産ラインでどの製品を製造するかを決定し、そのための部品が適切に納品されるよう計画します。小日程計画は、より現場の状況に即した生産を行うために必要とされ、設備の稼働率を高めつつ計画通りの納品を目指すものです。
MRPを使った資材の調達計画
MRPによる資材調達計画は、中日程・小日程計画に基づき、必要な部品や材料を適切なタイミングで確保できるように計画します。生産に必要な資材が不足しないよう管理し、同時に余剰在庫を防ぐことが目的です。
たとえば、製品Aの生産に必要な部品Bの在庫が50%以下になった時点で追加発注を行い、月末の需要に間に合うように調整します。これにより、在庫切れを防ぎつつ、過剰在庫を抱えるリスクも低減します。
MRPを活用した調達計画の特徴は、在庫と生産スケジュールの両方を見ながら適量を管理し、過剰在庫や欠品のリスクを最小限に抑える点と言えるでしょう。
おわりに
MPSとMRPは、製品の生産計画と資材調達の基盤を構築する重要なシステムで、それぞれが異なる役割で生産効率を高めます。MPSが生産量とタイミングを設定し、MRPがそれに基づいた資材手配を管理することで、需要に対する生産の安定性が向上します。Asprovaの生産スケジューラは、これらの計画を具体的なスケジュールに落とし込み、現場での効率的な生産指示を可能にします。生産スケジューラを導入して、生産現場での計画運用を強化してみませんか?
製品の詳細な導入事例は、以下よりご覧ください。

コラム編集部

最新記事 by コラム編集部 (全て見る)
- 納期管理:生産スケジューラの活用 - 2025年4月14日
- スケジューリング技術の応用による生産性の改善 - 2025年4月14日
- Lean Manufacturing~生産スケジューラの活用で最適な生産を - 2025年4月14日