ジャストインタイム(JIT)とは?意味やメリット、実施のポイントを紹介
2024.10.15A0 生産管理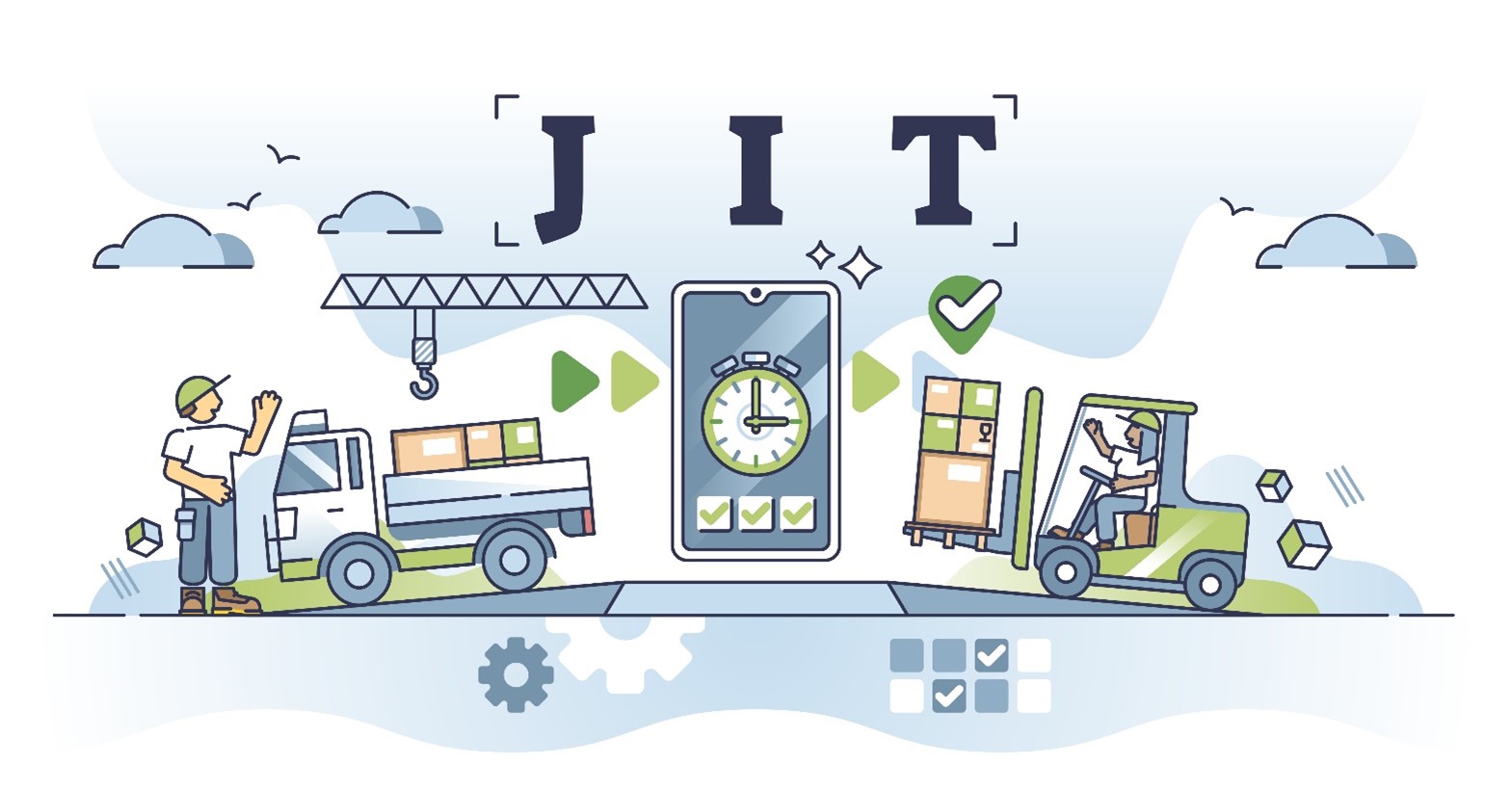
「必要以上に在庫を持たない」という大胆な発想で、製造業の常識を覆したジャストインタイム(JIT)方式。シンプルなスタンスですが、実際に現場に落とし込むのは難しいと感じる方も多いのではないでしょうか。本記事では、生産管理の画期的な考え方であるジャストインタイム生産方式について、意味やメリット、実施する際のポイントを解説します。
【目次】
■ジャストインタイム(JIT)とは
■ジャストインタイムの実施方法
■ジャストインタイムの注意点や課題
■まとめ
ジャストインタイム(JIT)とは
ジャストインタイムについて、その基本的な考えと、企業にとっての利点を見ていきましょう。
ジャストインタイムの定義と原則
ジャストインタイム(JIT)生産方式とは、「必要なものを、必要な時に、必要な量だけ作る」という考え方です。トヨタの大野耐一氏が考案した新しい生産方式で、今では多くの製造業や物流業界で取り入れられています。
ジャストインタイムの起源を知るために、製造業の生産方式について歴史を振り返ってみましょう。
1910年代、製造業の主流はヘンリー・フォードが確立した流れ作業による大量生産方式でした。この方式は効率的でしたが、市場需要の急な変化には対応できず、販売機会の損失や過剰在庫のリスクという問題がありました。この頃、「多種少量生産」という日本の事情に適した方法を模索していた大野氏は、スーパーで顧客が購入した分だけ商品を補充するように、必要な時に必要な分だけ生産するという発想を得ました。それがジャストインタイムです。この考え方は、需要に応じた生産を可能にし、在庫管理を最適化することで、従来の大量生産方式の欠点を克服しました。
ジャストインタイムには、以下3つの重要な原則があります。
・後工程引き取り(カンバン方式) 次の工程が必要とする時に、必要な分だけ提供する方法です。前の工程は、次の工程が求める分だけ生産します。
・工程の流れ化(小ロット生産、レイアウト整備) 生産過程で、無駄な待ち時間をなくします。製品がスムーズに流れるように工夫します。
・必要数でラインタクトを決める(教育・訓練、同期化) 顧客の需要、必要性に合わせて、ラインタクト(1つの製品を作るのにかかる時間)を決定します。
これらの原則を守ることで、在庫の保管時間やコストを削減でき、効率的な生産体制が実現できます。 また、トヨタではジャストインタイムを実現するために「カンバン方式」を採用しています。カンバン方式の「カンバン」とは、概念上のものではく実物です。製品に品名や品番、発注数などが記載されたカンバンがついているという点が大きな特徴です。各工程の担当者は、自分の作業が終わったらそのカンバンと製品を次の工程の担当者に渡します。カンバンと製品はセットで流れ、次の担当者は、カンバンを受けとってから製品を作るのです。
ジャストインタイムとカンバン方式の違いに混乱するかもしれませんが、この2つは目的と道具として明確に区別されています。ジャストインタイムの考え方を実現するための具体的な手段として、カンバン方式が存在するという点を押さえておきましょう。
ビジネスへの影響
ジャストインタイムの主なメリットは、在庫量の最適化、コスト削減と作業効率の向上、そしてリードタイムの短縮の3点です。以下で詳しく説明します。
在庫量の最適化
従来の生産方式では、次の受注に備えて先行生産を行うことが一般的でした。しかし、この方法には需要変動によって在庫が無駄になるリスクがありました。繰り返しになりますが、ジャストインタイムでは「必要なものを、必要な時に、必要な量だけ」生産することを目指します。カンバン方式を活用し、後工程の需要に応じて前工程が生産を行うため、過剰在庫のリスクを大幅に軽減できるのです。
コスト削減と作業効率の向上
ジャストインタイムでは、製造コストと在庫管理コストの削減が期待できます。製造コストには原材料費、人件費、電気代などで、在庫管理コストには保管場所や移動にかかる費用などが含まれます。ジャストインタイムは無駄を徹底的に排除する考え方に基づいているため、必要最小限の生産を行うことで原材料費や電気代を抑え、同時に人員の効率化による人件費削減にもつながるのです。
リードタイムの短縮
ジャストインタイムは、無駄な工程を排除することで製品の製造から納品までのリードタイムを大幅に短縮します。そのため、販売機会の損失を防止し、顧客満足度の向上につなげられます。さらに、迅速な対応や取引は企業イメージアップにも大きく貢献します。
ジャストインタイムの実施方法
ジャストインタイムの導入時のポイントとして、需要の予想や供給チェーンの整備などがあります。以下3つのポイントについて説明します。
- 需要予測と計画の重要性
- 供給チェーンの整備と管理
- 継続的改善の取り組み
需要予測と計画の重要性
ジャストインタイムを成功させるためには、正確な需要予測が欠かせません。需要予測の主な方法には、データ分析とマーケットリサーチがあります。 データ分析では、過去の販売データや市場動向を詳しく調べます。具体的には、季節変動や経済指標との相関関係を分析することで、将来の需要をより正確に予測できます。
一方、マーケットリサーチでは、顧客アンケートや競合他社の動向調査を行います。市場の変化や新たなトレンドをいち早く捉えることができる点が特徴です。
正確な需要予測が重要な理由は、在庫の最適化と生産効率の向上にあります。不正確な予測は、過剰在庫や品切れといった問題が発生し、コストの増加や顧客満足度の低下につながります。
反対に、予測が的中すれば、必要な量だけを適切なタイミングで生産・供給することができ、無駄を省いた効率的な生産が可能になります。
供給チェーンの整備と管理
ジャストインタイムを効果的に実施するためには、供給チェーンの整備やサプライヤーとの良好な関係構築を重視しましょう。ジャストインタイムは必要な部品を必要な時に必要な量だけ調達するスタイルです。この考え方を実現するには、部品や資材の調達で関わってくるサプライヤーとの協力が欠かせません。単なる取引先ではなく、ビジネスパートナーとしてサプライヤーと協力体制をとる意識が大切です。
継続的改善の取り組み
ジャストインタイムの継続的な改善活動の例として、「トヨタ式カイゼン」があります。トヨタ式カイゼンは、日本の製造業界で有名な改善手法の一つです。この手法は、トヨタ自動車が開発し、世界中に広まったことで、カイゼンという概念が国際的に認知されるきっかけとなりました。
トヨタ式カイゼンでは、製造過程において発生しがちな以下の要素を「7つのムダ」としています。
- 加工のムダ
- 在庫のムダ
- 造りすぎのムダ
- 手待ちのムダ
- 動作のムダ
- 運搬のムダ
- 不良・手直しのムダ
上記の無駄を排除することを基本として、課題の認識や対策、改善への行動につなげることがポイントです。
ジャストインタイムの注意点や課題
ジャストインタイムの導入には、注意点や課題があります。ここでは、在庫や生産遅延、コストの面から紹介します。
在庫切れや過剰在庫のリスクがある
ジャストインタイム方式では、必要最小限の在庫しか持たないのが特徴です。これにはメリットもありますが、同時にリスクも伴います。
たとえば、需要の増加や部品の供給遅延が想定外に起こると、部品不足による生産ラインの停止や、在庫切れによる欠品という販売機会の損失を招きます。逆に、需要が予想を下回った場合には、過剰在庫となるリスクもあります。過剰在庫は資金の無駄遣いになるだけでなく、保管や管理のコストもかかってしまいます。
下請けにしわ寄せがいくことで生産が遅延する
徹底したジャストインタイム方式では、自社だけでなく下請け企業にも余分な在庫を持たせないケースがあります。これには効率的な面もありますが、リスクも伴います。
たとえば、下請け企業からの部品供給が滞ると、すぐに生産ラインに支障をきたします。下請け企業の生産能力や輸送の問題で、部品が予定通りに届かないことがあるためです。
また、下請け企業の経営状況によっては、生産が遅延するリスクもあります。下請け企業が財政的な問題を抱えていたり、急な注文に対応できなかったりすると、全体の生産スケジュールに影響が出てしまいます。
徹底した在庫管理がポイントなジャストインタイムですが、あまりにも在庫に余裕がないと「下請けいじめ」と捉えられてしまうリスクもあります。導入を検討する際には、自社の生産体制だけでなく、下請け企業や子会社といった関連企業にどのくらい影響が出るのか想定し、相談のうえ進めていく必要があるでしょう。
導入時にはコストがかかる
ジャストインタイムを効果的に機能させるためには、カンバン方式の仕組みや、後工程引き取り・工程の流れ化・必要数でタクトを決めるといった三原則を適切に実装する必要があります。このカンバン方式の仕組みや工程の流れを実現するには、設備や動線などを新たに構築する必要があるため、コストがかかると言えるでしょう。導入のハードルが高いため、ジャストインタイムは中小企業には適していないという見方もあります。
品質管理にコストがかかる
ジャストインタイムは、各工程の無駄を徹底的に排除するため、余計な在庫は持ちません。また、生産ラインがスムーズに進むようにすることも、原則として盛り込んでいます。
そのため、不良品が出ると、必要な部品の在庫が不足し、生産ラインが止まるリスクがあります。そうならないために、常に品質の高い製品を生産しなければならず、品質管理にコストがかかります。
供給チェーンの断絶(供給の遅延や不足)
ジャストインタイムの大きなリスクの一つは、部品の供給が滞った際の影響です。余分な在庫がないため、部品供給の遅延や不足が生じると生産ラインが停止する恐れがあります。 たとえば、自然災害や事故による部品メーカーの操業停止、取引先の倒産などが起きた場合、部品の供給が途絶えて生産に大きな支障をきたす可能性も。
これらの問題に対処するためには、複数の供給元を確保することや、重要部品については、一定期間供給がなくても問題がない程度の在庫を保持するなどの対策が考えられます。
まとめ
ジャストインタイム(JIT)は、製造現場の業務効率を向上させる重要な手法です。必要なものを、必要な時に、必要な量だけ生産するという基本原則は簡潔ですが、実践するには課題があります。
ジャストインタイムのメリットをより効果的に引き出すには、ぜひ生産スケジューラを活用してください。Asprovaの生産スケジューラは豊富な標準機能の他にも、生産計画の良し悪しを判定できるSolverオプションがあり、ジャストインタイム の原則と高い親和性を持っています。
ジャストインタイムのメリットをより効果的に引き出すには、ぜひ生産スケジューラを活用してください。Asprovaの生産スケジューラは、工程全体のスケジュールを自動的に最適化し、無駄な在庫や遅延を防ぐことが可能です。例えば、後工程の進捗を見ながらタイムリーに生産指示を出すことで、在庫量の最適化が図れます。さらに、Solverオプションは、数百万通りの候補から最も効率の良い生産計画を自動で導き出し、リソースの最適配分を行います。この機能により、後工程に必要な部品の供給タイミングや量を最適化できるため、ジャストインタイムにおける「後工程引き取り」をサポート。また、納期遅延の最小化や段取り時間の削減を実現することで、ジャストインタイムの目標である生産ラインの効率化に貢献します。
製造業の悩みに寄り添った製品ですので、ぜひ業務効率化にお役立てください。生産スケジューラ導入によって具体的にどのような業務改善が実現したのかはこちらのページをご確認ください。

コラム編集部

最新記事 by コラム編集部 (全て見る)
- なぜこの2社は計画のブレを最小限にできたのか?精度向上のカギを解説 - 2025年7月2日
- “半日が10分に短縮”も可能に!属人化を脱し、計画作成を効率化した方法とは? - 2025年7月2日
- “なんとなく管理”からの脱却!デンカが語る、見える化による現場改善ストーリー - 2025年7月2日