カンバン方式の弱点やデメリットとは?克服するためのツールや方法を解説
2024.12.11A0 生産管理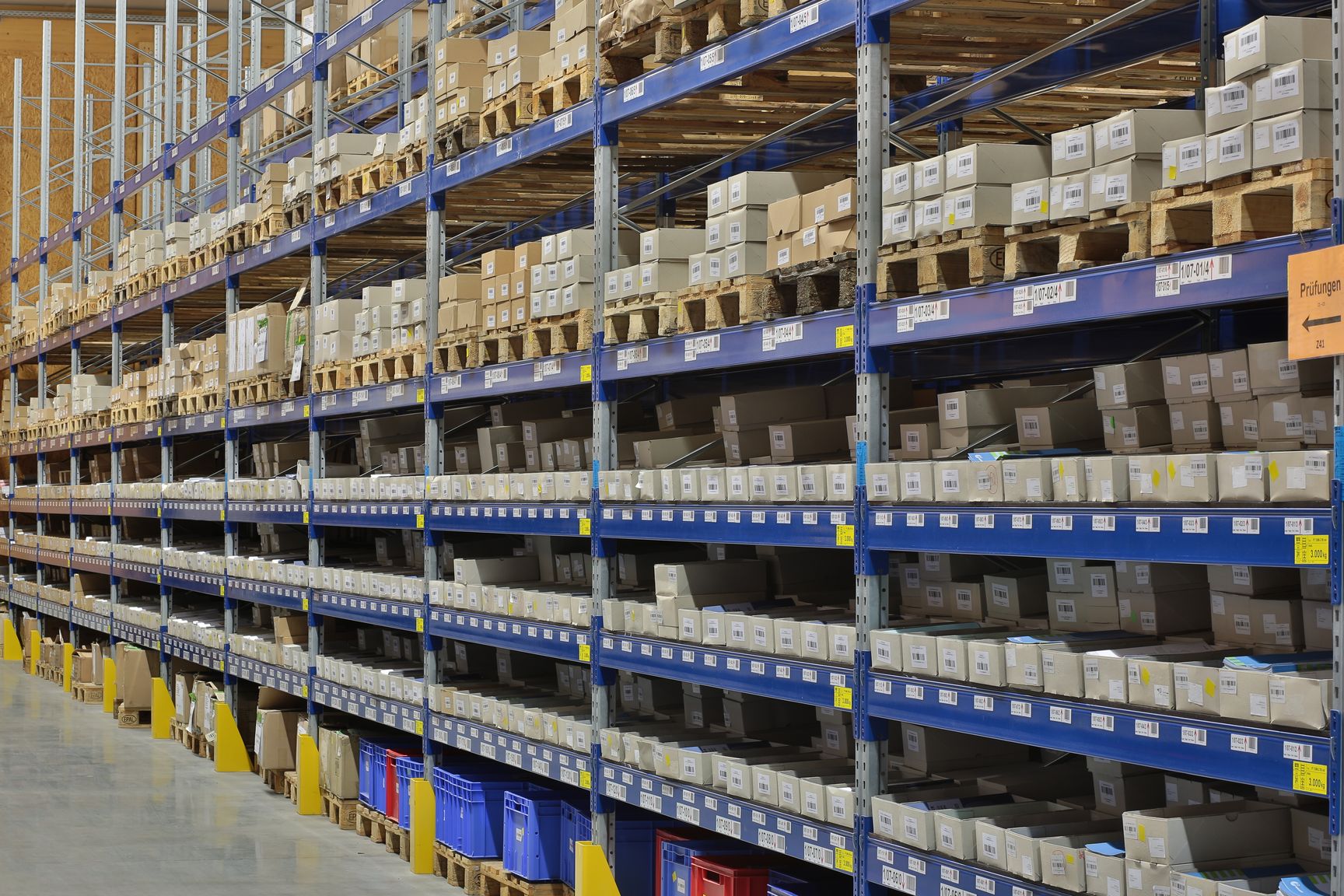
カンバン方式はトヨタ自動車が生み出した効率的な生産管理手法として知られ、製造業だけでなく、一般企業でもプロジェクトの管理方法として活用されています。製造業において様々なメリットをもたらしてくれるカンバン方式ですが、導入を検討する際は弱点やリスクについても理解しておくことが重要です。
本記事では、カンバン方式とはどういったものなのかの基礎知識をはじめ、メリットや弱点、効果的に活用するための方法やツールを紹介します。
【目次】
■カンバン方式とは?
■カンバン方式の限界が時代遅れとされる5つの理由
・1. 複雑なプロジェクトには対応力が不足
・2. タイムライン管理の欠如で予測が困難
・3. 過負荷による作業のバランス崩壊
・4. 自主性に依存しすぎて混乱を招く可能性
・5. 大規模プロジェクトには不向き
■カンバン方式の流れ
・1. 後工程からの「引き取りカンバン」発行
・2. 前工程での「生産指示カンバン」発行
・3. カンバンの回収と再利用
・4. 平準化とカイゼンの実施
■カンバン方式のメリット
・生産効率の向上で業務を最適化
・在庫を減らしてコストを削減
・情報共有のスムーズ化でミスを防止
・無駄の削減でリソースの最適化
■カンバン方式のデメリット
・欠品のリスクを招く可能性がある
・リアルタイムな対応が難しい
・平準化が前提条件であるため柔軟性に欠ける
■カンバン方式の概要と導入に向けた理解のポイント
カンバン方式とは?
カンバン方式とはトヨタ自動車が開発した生産管理方式で、「必要な物を、必要な時に、必要な量だけつくる」というジャストインタイムの考え方が取り入れられています。カンバン方式では、カンバンと呼ばれる商品管理カードを使用するのが特徴です。カードには商品名・品番・保管場所などの詳細情報が記載されており、後工程で使用した部品だけを製造することで在庫を最小限に抑える仕組みになっています。
かつては在庫過剰の問題を抱えていたトヨタ自動車ですが、カンバン方式の導入によって無駄な部品の生産を徹底的になくし、原価低減を実現しました。カンバン方式は、商品製造の無駄を省いて効率的に作業を進められる生産管理方式として主に製造業で採用されていますが、一般企業においてもプロジェクトのタスク管理や進捗管理の手段として応用されています。
カンバン方式の限界が時代遅れとされる5つの理由
カンバン方式でできることには限界があるため、カンバン方式に固執せずに自社に合った手法を検討することも必要です。自社に合っているかを判断するために、カンバン方式の限界についても把握しておきましょう。
1. 複雑なプロジェクトには対応力が不足
カンバン方式が効果を発揮するのは、タスクがシンプルで依存関係の少ないプロジェクトです。各タスクが独立していることを前提としているため、タスク間の依存関係が複雑なプロジェクトの場合、カンバン方式だけでは適切に管理するのが難しくなる可能性があります。カンバン方式だけで無理に管理しようとせず、別の手段やツールとの組み合わせを検討しましょう。
2. タイムライン管理の欠如で予測が困難
カンバン方式はタスク管理として優れている一方で、時系列ごとのタスクを把握できないため、前後にどのようなタスクがあるのかを把握するのが難しいというデメリットがあります。時系列での生産管理が難しく、部品がいつ必要になるのかも予測できないので、常に指示通りに生産できるとは限りません。そのため、納期厳守が求められるプロジェクトには不向きです。また、在庫や納期に余裕がない中で生産を求められる場合もあり、非効率的な作業環境によって現場の負担が大きくなる可能性もあります。
3. 過負荷による作業のバランス崩壊
カンバン方式では全工程で生産量や作業負荷を均一に保つことを前提としているため、特定の部分に業務が集中すると作業負荷のバランスが崩れ、ボトルネックが発生しやすくなります。カンバン方式は各タスクが独立しているので、タスク同士の関係が見えにくかったり全体で見た時のタスクの重要度を把握しにくかったりするのも難点です。業務の偏りをなくして平準化を長期的に維持するには、定期的に工程の見直しを行うことも求められます。
4. 自主性に依存しすぎて混乱を招く可能性
カンバン方式では平準化のために継続的な改善が求められるため、従業員は現場で見つかった課題に対してPDCAサイクルを実施しながら自ら立てた仮説を実行し、効果検証を行っていく必要があります。従業員の自主性を養うのに効果的な一方で、ガイドラインが不十分な場合や経験の浅いチームだと混乱を招く可能性があるので注意が必要です。現場の改善を従業員の自主性に依存しすぎるのは、生産効率の低下を招く場合もあることを認識し、必要に応じてガイドラインの作成や教育など自主性を養うための土台づくりも行うようにしましょう。
5. 大規模プロジェクトには不向き
複数のチームが関わる大規模なプロジェクトの場合、カンバン方式だと管理が複雑になりすぎる可能性があります。小規模なチームやプロジェクト向きのため、大規模なプロジェクトの生産管理やタスク管理に取り組みたい場合は別の手法を検討しましょう。
カンバン方式の流れ
カンバン方式を実践するにあたり、どのようなステップで行なわれるのか基本的な流れをみていきましょう。
1. 後工程からの「引き取りカンバン」発行
後工程で使用する部品には「引き取りカンバン」が取り付けられています。引き取りカンバンとは、何を・いつ・どこに・どれだけ・どういう順序で運搬するかの指示情報です。後工程では部品を使用する際に取り付けられている引き取りカンバンを外し、外したカンバンを持って在庫置き場へ部品を引き取りに行きます。部品を引き取ったら持ってきた引き取りカンバンを取り付け、後工程に運びます。
2. 前工程での「生産指示カンバン」発行
在庫置き場に保管されている部品には生産指示カンバン(仕掛けカンバン)が取り付けられており、後工程が部品を引き取る際は生産指示カンバンを外して前工程に送ります。前工程では生産指示カンバンに記載された数だけの部品を生産し、完成した部品に生産指示カンバンを取り付けて在庫置き場に補充します。前工程にはリードタイムが定められており、それまでに部品を生産して在庫置き場に供給しなければいけません。
カンバンの枚数とリードタイムは、生産が遅延すると在庫が欠品する可能性が高くなるように設定されています。
3. カンバンの回収と再利用
後工程が部品を引き取る際に外した生産指示カンバンは等間隔で回収され、次の生産の準備が進められます。カンバンの発行から回収までの流れを繰り返すことで一定のリードタイム内での生産フローが維持され、無駄な在庫をできる限り発生させないように管理するのがカンバン方式の特徴です。
部品を引き取る際にカンバンの外し忘れがあると、前工程に生産の指示が共有されないので注意しましょう。後工程で必要な部品が供給されずに、欠品の発生や作業の中断といった問題が発生してしまいます。生産指示カンバンを入れるポストの場所を工夫して外し忘れを防ぐほか、生産効率を上げるためにカンバンを小刻みに回収する仕組みづくりも必要です。
また、カンバンを回収する時間を定めて後工程と前工程で共有しておけばお互いに作業の見通しができ、現場の作業効率を高められます。
4. 平準化とカイゼンの実施
カンバン方式の運用は「平準化」が前提です。平準化とはすべての工程で生産量や作業負荷を均一に保つことを言います。生産量にばらつきがあると、無駄な人員や在庫が発生する原因になります。平準化によって適切な生産量とそれに見合った人員に調整することで、リソースの無駄を最小限に抑えながら、効率的な生産を実現。また、平準化が前提となるカンバン方式では現場の抱えている課題を見つけやすいため、改善活動の一環としても活用されており、常に業務の最適化を図ることができます。
カンバン方式についてより詳しく知りたい方は下記記事もご覧ください。
かんばん方式とは?種類や流れを分かりやすく解説
カンバン方式のメリット
カンバン方式の導入は現場に少なからず管理の負担を与えるので、現場にとってもメリットのあるものだと説明して、理解を得ることが大切です。そのためにも、カンバン方式のメリットについてしっかりと把握しておきましょう。
生産効率の向上で業務を最適化
カンバン方式では必要な部品や材料が必要な時に供給されるため、生産を計画通りに進められ、全体の作業効率が向上するというメリットがあります。作業効率の向上によってリードタイムが短縮されるほか、無駄な作業の削減による業務の最適化にもつながります。
在庫を減らしてコストを削減
カンバン方式では必要な量を必要な時にだけ生産するため、過剰在庫のリスクが減り、在庫管理の効率化・安定化を図れるのがメリットです。過剰在庫を抱えていると保管・管理のための手間やコストがかかるほか、製品のモデルチェンジによって処分費用が発生することもあります。カンバン方式によって無駄な在庫をできる限り発生させないようにすることで、これらのコストを削減することが可能です。
情報共有のスムーズ化でミスを防止
生産プロセスにおいて必要な情報がカンバンにすべて記載されているため、何をどのぐらい生産したら良いのかといった作業指示をスムーズに共有できるというメリットがあります。また、カンバンの数で作業の遅れや進捗についても把握できるので、進捗管理の負担を軽減することも可能です。カンバンを使った情報の一元管理によって必要な情報をすぐに把握できるようになるほか、情報の伝達ミスの防止にもつながります。
無駄の削減でリソースの最適化
平準化が求められるカンバン方式は、製造現場が抱える問題点を可視化する道具としても活用できます。無駄な工程や作業を把握することで余剰人員も明らかにでき、最適な人員配置が行えるでしょう。あらゆる無駄の排除とリソースの最適化によって全体的な効率が向上し、コスト削減につながるのもカンバン方式のメリットです。
カンバン方式のデメリット
カンバン方式の導入にはメリットだけでなくデメリットも伴うため、事前に把握して対策を検討しておくことが重要です。カンバン方式の導入によって想定されるデメリットを解説します。
欠品のリスクを招く可能性がある
カンバン方式は、必要なものを必要なだけ生産することで在庫を最小限に抑える仕組みになっているため、予期せぬトラブルや工程に問題が発生した場合、欠品する恐れがあります。欠品が発生すると工場全体の生産に影響を及ぼすほか、納期遅延によるクライアントからの信頼低下や売上減少につながりかねません。欠品のリスクを避けるためにも、緊急時に備えて安全在庫を確保しておく、緊急発生時の対応をサプライヤーと事前に決めておくなどの対策が必要です。
現場の負担が増大する恐れ
カンバン方式は不良品を出さないことを前提とした生産方式で、現場には徹底した品質管理が求められます。また、カンバンの枚数が在庫数を決定する重要な指標となるため、カンバンを適切に管理できる体制が整っていないとカンバン方式の効果を十分に得られません。枚数が適正かを分析・管理するのはもちろん、生産終了となった場合には速やかに破棄する必要があるため、管理工数もかかります。徹底した品質管理やカンバン管理が必要となるので、現場の作業者や担当者の負担が大きくなる可能性があります。
リアルタイムな対応が難しい
カンバン方式は過去の実績に基づいて生産指示を出すため、需要の急激な変化に対応しにくいのがデメリットです。また、生産量や人員を平準化していることがカンバン方式の前提になるので、計画の変動に弱く、急な増産依頼に対応できないのも弱点です。需要が急増した場合にリアルタイムで生産量を増やすということが難しく、納期に遅れが生じる、もしくは納品に対応できないということも考えられます。売上減少や受注機会の損失につながりかねないため、需要の変動が激しい業界には向きません。
平準化が前提条件であるため柔軟性に欠ける
カンバン方式は生産の平準化が前提となるため、どの現場でも適用できる生産管理手法ではありません。使った分だけ在庫を補充するという考え方なので繰り返し生産する製品には適していますが、多品種少量生産や一点物の受注生産、需要変動の大きい製品、使用期限や賞味期限の短い製品には不向きです。これらの製品にカンバン方式を導入したとしても生産効率が悪化することがあるため、自社の生産環境に適しているかを考えたうえで導入を検討しましょう。
カンバン方式の概要と導入に向けた理解のポイント
カンバン方式は「必要な物を、必要な時に、必要な量だけつくる」というジャストインタイムの考え方を取り入れた生産管理方式で、在庫を最小限に抑えられるというメリットがあります。効率的な生産を実現するために、すべての工程で生産量や作業負荷を均一に保つ平準化が前提となっているのも特徴です。
ただ、平準化を実現するには、納期や効率などを考慮しながら生産計画を立てる必要があります。生産量を一定にしたとしても、納期遅れや段取り替えの増加によって生産効率が下がっては意味がないからです。生産量や作業負荷を一定にする生産計画を立てるのは手間がかかるため、カンバン方式を取り入れるうえで平準化を図りたいのであればシステムの導入を検討しましょう。
アスプローバが提供する生産スケジューラは、複雑な生産計画の立案を迅速かつ正確に行え、リソース配分の最適化も実現します。3,000工場を超える製造現場で導入されており、現場の業務改善やコスト削減に貢献しているシステムです。アスプローバの生産スケジューラによる業務改善の事例をもっと詳しく知りたいという方は、こちらのページをご確認ください。

コラム編集部

最新記事 by コラム編集部 (全て見る)
- 納期管理:生産スケジューラの活用 - 2025年4月14日
- スケジューリング技術の応用による生産性の改善 - 2025年4月14日
- Lean Manufacturing~生産スケジューラの活用で最適な生産を - 2025年4月14日