リードタイムとは?リードタイムの種類や短縮方法を解説
2021.01.14A0 生産管理 , A1:生産計画・スケジューリング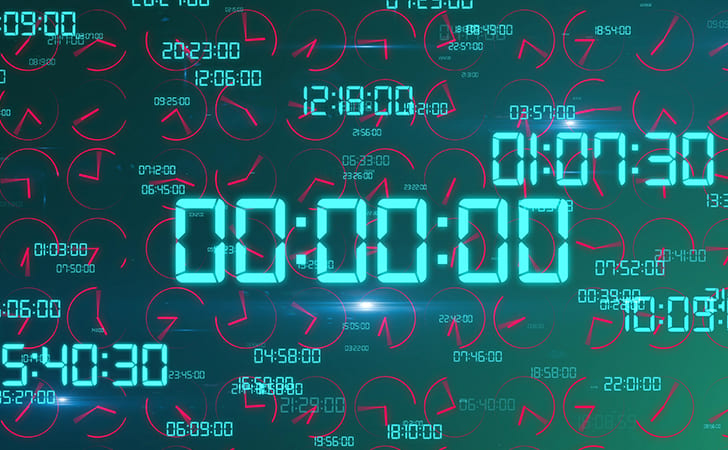
製造業や物流の現場でよく使われるリードタイムを短縮する術を知っておくと、キャッシュフローの改善やサービスの向上につながります。生産計画においてとても重視される項目です。
今回は、リードタイムとは何かについて説明しながら、リードタイムを短縮することによって得られるメリットやリードタイムを短縮する方法をわかりやすく解説していきます。
業務を効率化したい、差別化を図りたい人は、ぜひ基礎から理解して業務改善にお役立てください。
【目次】
■リードタイムとは
・納期との違い
■リードタイムの種類
・開発リードタイム
・調達リードタイム
・生産リードタイム
・配送リードタイム
■リードタイムの関連用語
・タクトタイム
・サイクルタイム
■リードタイムの計算方法
■リードタイムを短縮するメリット
・メリット1:仕掛在庫の削減
・メリット2:キャッシュフローの改善
・メリット3:サービス強化で競争の優位に立てる
■リードタイムを短縮するデメリット
・デメリット1:品質低下のリスク
・デメリット2:小ロット生産による欠品リスク
・デメリット3:採算が合わない
■リードタイムを短縮するための方法・開発リードタイムの短縮
・調達リードタイムの短縮
・生産リードタイムの短縮
・配送リードタイムの短縮
■おわりに
リードタイムとは
製造業におけるリードタイムとは、商品の発注から納品に至るまでの生産や輸送などにかかる時間や日数のことを指しています。製造業で使われている、手番(手配番数)や先行日数、基準日程などと意味合いは同じになります。
大きく、下記の4つに分かれており、リードタイムを短縮するうえではこれらのうちどのリードタイムを短縮するのかを考えていく必要があります。
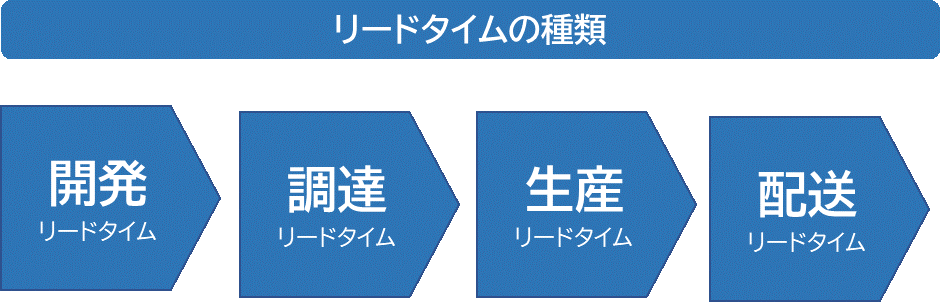
リードタイムの種類
開発リードタイム
製品の企画から製品を開発・設計するまでのプロセスに要する期間です。 設計や試作、実験を繰り返して製品の詳細を決めていく工程や工場、生産ライン、金型などを作り込んで生産準備をする工程も、開発リードタイムに含まれます。 そのため、製品を受注生産でつくる場合、開発リードタイムは大きく異なります。 例えば、顧客からの受注に基づいて開発・設計を始める「個別受注生産」では開発リードタイムが発生しますが、既存仕様に基づいて製品をつくる方式の受注生産「繰り返し受注生産」では、開発リードタイムは発生しません。
調達リードタイム
製造用の材料や部品を発注してから納品・受け入れ検査を経て、製造現場に納入されるまでにかかる全体の時間の合計が「調達リードタイム」です。 部品の選定や交渉、調達先の決定など、調達にはさまざまなプロセスがあり、長期間を要することも少なくありません。 また、発注する材料が製造品の場合、調達先の生産リードタイムも加わるため、より長い日数が必要となります。 そのため、調達リードタイムの短縮は全体のリードタイム(トータルリードタイム)の短縮に直結します。
生産リードタイム
生産リードタイムとは、製造をスタートしてから製品の完成に至るまでの期間で、製造リードタイムと呼ばれることもあります。 生産リードタイムが長期化すると、製造途中の仕掛在庫が発生し、管理の負担を増やすだけでなく、在庫スペースの圧迫といった問題も引き起こします。 そのため、製造業において生産リードタイムの短縮は、業務全体を改善したい際の重要なポイントです。 ちなみに、生産リードタイムには製品の加工や組立作業の所要時間だけでなく、各工程間で生じる待ち時間や運搬時間、検査時間などの「停滞時間」も含まれます。 生産リードタイムを短縮したい場合は、この停滞時間をいかに改善できるかも重要です。
配送リードタイム
製品の出荷指示から納品先へ配達・納品までに要する期間を示すのが、配送リードタイムです。物流リードタイムと呼ばれることもあります。 配送リードタイムを短縮したい場合、工程をさらに細分化して考えることが必要です。 出荷を指示してからピッキング・検品、梱包などを経て出荷されるまでを「出荷リードタイム」、出荷してから配達が完了するまでを「配達(輸送)リードタイム」といい、各リードタイムを短縮するためにさまざまな対策が施されます。 例えば、出荷リードタイムを短縮したい場合、出荷作業を効率化するために物流業務のDX化を推進する、配達(輸送)リードタイムを短縮したい場合、配達作業を効率化するために、高頻度で小口配送を行うなどが有効な対策です。
リードタイムの関連用語
リードタイムを考えるうえで重要なのが「タクトタイム」や「サイクルタイム」です。これらの時間を具体的に把握していると、生産の効率化や実際の作業時間を短縮するための改善点を導きやすくなります。
タクトタイム
製品1個あたりの製造にかかる時間を示すもので、ピッチタイムとも呼ばれます。タクトタイムの計算方法は、以下の通りです。
・タクトタイム=稼働時間÷必要製造数 |
タクトタイムが短いと、稼働時間に対してより多くの製品を製造できますが、タクトタイムが長いと少量しか製品を製造できません。製造ペースを可視化できるタクトタイムの把握は、業務改善において重要な役割を果たします。
サイクルタイム
サイクルタイムとは、製品を製造するのに工程を開始してから完了するまでの1サイクルで、実際にかかる時間です。製造の正味時間を把握するために、工程の余裕(バッファ)や損失を考慮せずに求められます。
計算式は以下の通りです。
・サイクルタイム=稼働時間÷実際の生産数 |
タクトタイムとサイクルタイムが同じだと、1サイクルで必要な数を効率よく製造できていることになります。よって、タクトタイムとサイクルタイムは同等な状態が理想的です。
もし、タクトタイムよりもサイクルタイムのほうが長い場合、生産能力が生産目標に追いついていない状態を表します。このままの状態で製造を続けても、納期までに必要な製造数はつくれません。
反対にサイクルタイムよりもタクトタイムのほうが長い場合、目標よりも早く生産できていることになりますが、過剰在庫が発生しないような注意が必要です。このように、タクトタイムとサイクルタイムの両方を求めることで、製造現場の作業効率を見直すことにつながります。
「タクトタイム」や「サイクルタイム」をさらに詳しく知りたい方はこちらの記事をご覧ください。
リードタイムの計算方法
リードタイムの計算には、「固定リードタイム」と「変動リードタイム」の2つがあります。
■固定リードタイムの計算
品目ごとに設定したリードタイムを固定のものと考えて、納期から予定開始日を求める計算方法です。固定リードタイムは、以下の計算式で求められます。
・予定開始日=納期-(リードタイム+安全リードタイム) |
■変動リードタイムの計算
ロットの大きさにより、リードタイムを変動させる方法です。品目に設定された段取りや移動などの時間は固定で考えて、1個当たりの実作業時間を用いて計算します。
・予定開始日=納期-{(待ち+段取り+後処理+移動)+オーダーの所要量×1個当たりの実作業時間} |
リードタイムを計算して具体的な数値を把握することは、作業を効率化したい際に有効ですが、個別に計算して導き出すのは手間も時間もかかります。生産スケジューラなら、生産スケジュールを最適化して段取り時間を短縮できるため、リードタイムの削減につながります。また、在庫や納期、人的要因、市場の動向や顧客ニーズの変化など、各方面で変更があった際の計画の見直しも瞬時に対応が可能です。
下記のページでは生産スケジューラについてわかりやすく解説していますので、ご興味のある方はぜひこちらをご覧ください。
リードタイムを短縮するメリット
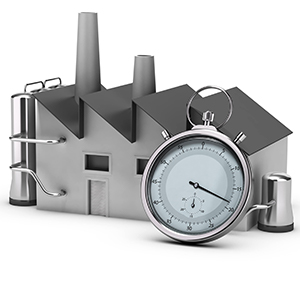
リードタイムを短縮できると、仕掛在庫減少によってコスト削減を実現できるのはもちろん、業務改善による短納期化によって、他社との差別化の強化も可能です。ここからはリードタイムの短縮によるメリットを詳しく解説します。
メリット1:仕掛在庫の削減
仕掛在庫とは保有在庫の内数で実際に倉庫から払い出され、上位品目を製造するために工程で在庫すること、またはその在庫数を示します。一般には外注業者も外注工程として捉え、支給品を仕掛在庫として把握します。
製造工程において「停滞時間(待ち時間や運搬・検査時間)」を短縮できると、仕掛在庫が削減されます。仕掛在庫の削減によって管理工数や人員を適正化できると、管理費をはじめとした人的コストも削減が可能です。 また、余剰在庫に割り当てていた保管用のスペースもなくなるため、在庫の管理コストの削減にも役立ちます。
メリット3:キャッシュフローの改善
リードタイムを短縮できると、受注から納品までの期間が短くなります。つまり、キャッシュを受け取るまでの期間も短くなるので、従来よりもキャッシュフローが向上します。キャッシュフローの改善は、十分な運転資金の確保につながるものです。これまでは対応できなかった突然の増産依頼にも、余裕を持って対応できるようになります。
メリット3:サービス強化で競争の優位に立てる
リードタイムの短縮により、製品を短納期で生産できるようになります。特に製造業において、納期は、品質やコストと並び、競争優位性を獲得するための大事な要素として位置付けられているものです。品質での差別化が困難な場合、短納期サービスが他社との差別化につながり、強みになります。特に部品製造や部材生産を行う企業の場合、短納期は大きな武器です。
リードタイムを短縮するデメリット
リードタイムの短縮は、業務効率を高め、収益性や顧客満足度を向上させるために行うものです。
ところが、リードタイムの短縮そのものを目的にしてしまうと、品質やコストのバランスを崩し、結果として業績や業務効率の悪化を招いてしまう恐れがあります。
リードタイムの短縮によって考えられるリスクやデメリットは、以下の通りです。
デメリット1:品質低下のリスク
リードタイムを短縮したいからといって、品質維持に必要な作業までを削ってしまうと、品質の低下を招いてしまいます。また、やみくもにリードタイムの目標を短くしてしまうのも注意。無理な人員配置や気の焦りから、ミスを招いてしまいます。工程が変わっても製品の品質は変わらないか、ミスが起こらないかを考慮しながらリードタイムを見直すことが大切です。
デメリット2:小ロット生産による欠品リスク
無理なリードタイムの短縮が欠品を招くケースもあります。余剰在庫を減らすのはよい面もありますが、小ロット生産の場合、トラブルを機に生産がストップしてしまう可能性があるからです。
近年は豪雨や台風など天候の影響で被害を受けてしまい、業務が滞ってしまうことも珍しくありません。ストップしている間は、在庫で賄わなければならないこともあるでしょう。
デメリット3:採算が合わない
リードタイムを短縮するために、生産体制を全体で最適化する業務のDX化の取り組みが各企業で進められています。ところが、製造現場によっては設備導入の費用対効果が見合わないケースもあるため、十分なリサーチや分析は必要です。 自社の製造現場には大規模な設備導入が必要か、投資が費用対効果に見合うか、採算を取れるかを考えたうえで進めましょう。
リードタイムを短縮するための方法
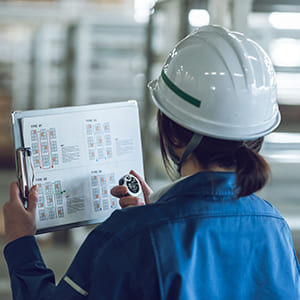
リードタイムの短縮は、細分化したリードタイムごとに取り組みを行います。
ここからは、細分化した工程ごとのリードタイム短縮方法をご紹介しています。
開発リードタイムの短縮
開発リードタイムを短縮するには、以下のような取り組みを行います。
- 開発工程の優先順位付け
- 開発工程の簡略化
- 原材料や部品の共有化
- 仕入れ先の変更
開発リードタイムの短縮は、製造業のみならずさまざまな業種において重要なポイントです。 リードタイムが長くなると、トレンドの変化や顧客のニーズに合わせた販売ができなくなり、製品の持つ販売力が弱まってしまいます。
調達リードタイムの短縮
調達リードタイムの短縮方法は、非常にシンプルです。
- 外部調達にかかる時間の調査
- 仕入先へのリードタイム短縮の交渉
部材の仕入れ先が海外の場合、想定以上の時間がかかる場合もあります。外部調達が多い製品ほど、綿密な事前のリサーチが必要です。
自社で部品や原料を調達している場合には、社内で調達の見直しや改善を行います。 仕入先のリードタイムが長い場合、発注計画の見直しを提案するといったように、仕入先と一緒に改善点を探しながらリードタイムを短縮していきます。
生産リードタイムの短縮
生産リードタイムを短縮するのに有効なのは、以下のような方法です。
- 最新設備の導入
- 人員配置、人員数の最適化
- 労働時間や作業時間の短縮
- 仕掛在庫の適正管理
- 生産計画の見直しと適正化
配送リードタイムの短縮
配送リードタイムは、専用機器やツールの導入によって短縮を目指すケースが多いです。
- 倉庫管理システムの導入
- 配送管理システムの導入
- ハンディーターミナルの導入
- ピッキングの導線整備・自動化
- 検品、梱包作業の効率化
- 配送の外注
生産スケジューリングを最適化できれば、製造リードタイムの削減や起こり得るさまざまなリスクへの柔軟な対応ができるのはもちろん、競争力の強化にもつながります。生産スケジューラは、前後工程のつながりを考慮した高精度の生産計画を立案できるので、各工程のリードタイムの短縮はもちろん、トータルリードタイムの短縮を実現できます。 生産スケジューラを使った活用法や、導入により得られるメリットについては以下のページで詳しく解説しています。
おわりに
商品の発注から納品に至るまでの生産や輸送にかかるリードタイムを短縮できれば、業務効率化によるコスト削減や人員配置の最適化だけでなく、キャッシュフローの改善や競争力の強化も目指せるようになります。 リードタイムの短縮は、品質や顧客満足度を維持できるか、採算を取れるかを検討したうえで慎重に進めることが大切です。

コラム編集部

最新記事 by コラム編集部 (全て見る)
- なぜこの2社は計画のブレを最小限にできたのか?精度向上のカギを解説 - 2025年7月2日
- “半日が10分に短縮”も可能に!属人化を脱し、計画作成を効率化した方法とは? - 2025年7月2日
- “なんとなく管理”からの脱却!デンカが語る、見える化による現場改善ストーリー - 2025年7月2日