ライン生産方式とは?セル生産方式の違いやメリット
2024.12.11A0 生産管理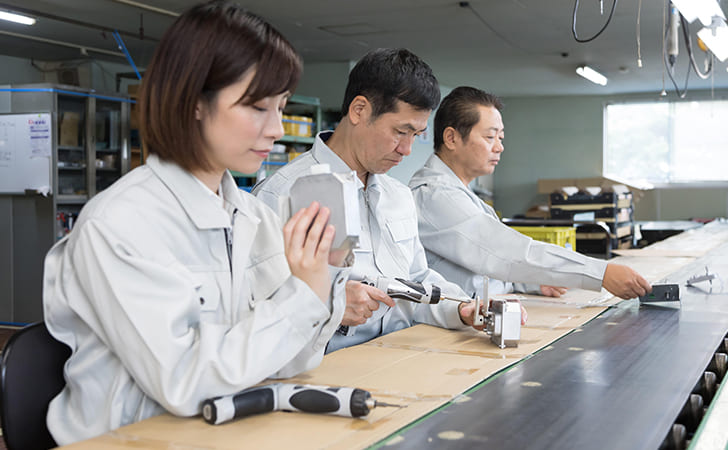
大量生産を前提とした製造工業で広く採用されてきた「ライン生産方式」は、工程ごとに配置された作業者が部品を組み立てていき、流れ作業的に製品を生産する方式です。近年では、多品種少量生産の需要が増えていることから、少人数の作業者で製品を組み立てる「セル生産方式」も活用されるようになりました。
本記事では、2つの生産方式の詳しい説明やメリットデメリット、業務効率化のためのポイントを解説しています。
【目次】
■ライン生産方式とは
・ライン生産方式のイメージ
■セル生産方式とは
・グループで行う U字型ライン生産方式
・グループで行う 分割ラインセル生産方式
・一人で行う 一人屋台方式
・一人で行う 巡回方式
■ライン生産方式とセル生産方式の違いとメリット
・それぞれの違い
・ライン生産方式のメリット
・セル生産方式のメリット
■ライン生産方式とセル生産方式のデメリット
・ライン生産方式のデメリット
・セル生産方式のデメリット
■生産スケジューラと生産方式の相性
・ライン生産方式との相性
・セル生産方式との相性
■おわりに
ライン生産方式とは
ライン生産方式とは、生産ライン上にある各作業ステーションに作業を割り付け、ライン上を品物が移動するにつれ加工が進む生産方式のことです。 ライン生産方式では、流れ作業により製品が完成していきます。
流れ作業により、効率的に数多くの製品をつくることができるため、少品種多量生産に向いた生産方式だと言われています。 イメージで考えてみると、ライン生産方式がどのような生産方式なのかが分かりやすくなります。
ライン生産方式のイメージ
ベルトコンベヤーの上に、多くの半製品が規則的に並んでいます。
そのベルトコンベヤーに沿って、作業場があります。
作業場では、それぞれの作業者が半製品に部品を取り付けていきます。
これによって、半製品がベルトコンベヤーを流れ終わるころには、完成品ができあがっているというわけです。
セル生産方式とは
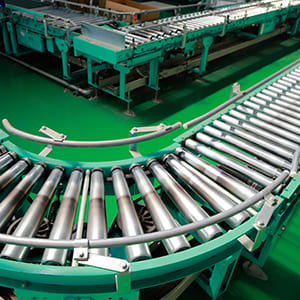
直線状のベルトコンベヤーの上を製品が流れるライン生産方式とは違い、セル生産方式ではL字型やU字型のラインを使用します。 ライン生産方式よりも、少人数で作業を行うことも特徴の一つです。
グループで行う「U字型ライン生産方式」「分割ラインセル生産方式」一人で行う「一人屋台方式」と「巡回方式」などがあります。
グループで行う U字型ライン生産方式
文字通り、U字型の形状をとる生産方式です。
U字型やL字型などの形状をとることで、直線状よりも一人の作業者に割り付ける作業の組み合わせが豊富になることがメリットです。
数人の担当者が、それぞれ複数の工程を受け持ち作業を行います。
作業者が後ろを振り返れば、別の工程の作業にすぐに取り掛かることができるというメリットがあります。
グループで行う 分割ラインセル生産方式
ベルトコンベヤーを使わず、作業者同士が手渡しで半製品を受け渡しする生産方式です。
一人で行う 一人屋台方式
屋台と呼ばれる一人用の作業ステーションで、一人ですべての生産を行うのが一人屋台方式です。
一人で行う 巡回方式
作業者が自ら仕掛け品を運びながら、すべての工程を巡回するのが巡回方式です。
ライン生産方式とセル生産方式の違いとメリット
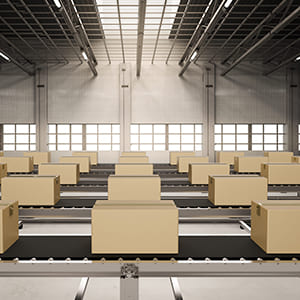
ここでは、生産方式の違いやメリットについて解説します。
ライン生産方式 | セル生産方式 | |
---|---|---|
特徴 | 生産ライン上にある各作業ステーションに作業を割り付け、ライン上を品物が移動するにつれ加工が進む生産方式 | L字型やU字型のラインを使用し、セル単位で行う生産方式 |
業務内容 | 少ない | 多い |
作業場所 | ベルトコンベヤー前の所定の位置 | 所定の位置、もしくは適宜移動 |
必要な人数 | 多い | 少ない |
ロット | 少品種多量生産向き | 多品種少量生産向き |
ライン生産方式のメリット
ライン生産方式のメリットには、以下のようなものがあります。
メリット1:生産効率の向上
ライン生産方式の利点の一つは、生産効率の向上です。各工程が専門的に分担され、担当者がそれぞれの作業に精通しやすくなるため、作業の効率化が進みます。また、各工程の最適化によりって無駄な動きが減ることで、全体の生産プロセスがスムーズに進行するでしょう。
さらに、自動化技術を導入しやすい点もメリットです。結果、人的エラーを削減して、全体的な効率がさらに向上します。
メリット2:品質の安定性
ライン生産方式は、各工程が標準化されているのが特徴。そのため、作業者間での品質のばらつきが抑えられ、品質水準を一定に保ちやすくなるのがメリットです。また、各工程にはチェック機能が備わっているため、不良品を早期に発見して対応できます。さらに、品質管理システムの導入が進むと、データに基づいた品質改善も行えるようになるでしょう。
メリット3:コスト削減
ライン生産方式では、作業の効率化と標準化が進むことで、人件費や材料費の低減が期待できます。製品ごとのコストは、大量生産することで抑えられるでしょう。また、不良品の削減や在庫管理の最適化によって、無駄な費用も減らせます。さらに、設備投資を効率よく進めることで、長期的な視点でもコストの圧縮が見込めます。
初期の導入コストはセル生産方式の方が低いものの、ライン生産方式では作業者の教育にかかる費用を削減でき、結果的に長期的なコスト削減が可能です。
メリット4:生産速度の向上
ライン生産方式では、各工程が連続的に配置されているため、作業の流れがスムーズです。製品の移動時間や待機時間が抑えられ、全体の生産サイクルが短縮できます。ボトルネックとなる工程の特定と改善も容易になるため、生産速度の向上が図れます。また、自動化技術を導入すれば、24時間稼働も可能です。
メリット5:在庫管理の効率化
ライン生産方式では、生産の流れが均一化されるため、必要な材料や部品の予測がしやすくなります。これにより、ジャストインタイム方式の導入が可能となり、過剰在庫や在庫切れのリスクを減らせます。生産状況をリアルタイムで把握することで、在庫管理がスムーズになり、資材の調達もタイミングよく行えるでしょう。この結果、在庫関連コストの削減や資金効率の向上が期待でき、全体的な資材管理をより効率化できます。
セル生産方式のメリット
ここでは、セル生産方式のメリットについてまとめました。
メリット1:柔軟な生産対応
セル生産方式は、生産ユニットごとに作業が完結するため、市場の変化に応じた生産調整が容易です。需要に応じてセルの数を増減させたり、配置を変更したりすることで、スムーズに対応できます。また、製品ごとにセルを設定することで、多品種少量生産にも対応可能です。さらに、新製品の導入や設計変更にも迅速に対応できるため、製品サイクルが短い業界でも効率的です。このように、生産ユニットの変更が容易なため、パソコンや家電製品など、モデルチェンジの多い業界で採用が進んでいます。
メリット2:初期コスト削減
セル生産方式では、大規模な設備投資が不要なため、初期コストを抑えられる点がメリットです。ライン生産方式では、ベルトコンベヤーや自動化設備、さらに作業スタッフの確保にコストがかかる傾向があります。一方で、セル生産方式は主に手作業で対応できるため、機械設備への投資を抑えることが可能です。また、必要な量だけを生産するため、過剰生産や在庫の無駄を削減できます。さらに、作業者が多能工化されることで、人員の配置が効率化され、人件費も最適化されます。
加えて、各セルで品質管理を行うため、不良品の早期発見が可能であり、品質に関わるコストも削減できます。セルごとに改善活動がしやすく、継続的なコスト削減も期待できるでしょう。
メリット3:作業者のスキル向上
セル生産方式では、一人の作業者が複数の工程を担当するため、自然と多能工化が進むのがメリット。これにより、作業者は幅広い技能を習得し、製品全体を理解できるようになります。また、セル内で問題解決や改善活動に取り組むことで、作業者自身の主体性も高められるでしょう。
品質管理や生産管理を担当させれば、マネジメント能力も身につきます。柔軟で高度なスキルを持つ人材が育つことは、企業にとって大きなメリットです。
メリット4:生産プロセスの効率化
セル生産方式では、一つのセル内で製品の組立てが完結するため、工程間の待ち時間や移動時間を削減できます。また、作業者が全体の工程を把握しているため、ボトルネックを見つけやすく、迅速な改善が可能です。加えて、各セルで品質チェックを行うことで、不良品の早期発見と対策が進み、手戻りのロスも最小限に抑えられます。セル内で継続的に改善を続けることで、生産プロセスが常に最適化され、結果としてリードタイムの短縮や生産性の向上が期待できます。
ライン生産方式とセル生産方式のデメリット
ここでは、各生産方式のデメリットについて紹介します。
ライン生産方式のデメリット
ライン生産方式のデメリットから見ていきましょう。
デメリット1:単純作業によるモチベーション低下
ライン生産方式では、基本的に作業者は同じ作業を繰り返すことになります。仕事を進めやすい利点もありますが、単調な作業が続くことで作業者の創造性や自主性を制限してしまう点がリスクです。そうした状況が続けば、仕事への興味や意欲を失ってしまうかもしれません。長期的に見ると、職務満足度の低下、生産性の減少、離職率の上昇といった問題につながる恐れもあります。作業者のスキル向上の機会も限られるため、キャリア発展の観点からもデメリットになるでしょう。
デメリット2:柔軟性の欠如
ライン生産方式は、特定の製品や一定の生産量に特化しているため、需要の変動や製品変更に対応するのが難しいという課題があります。生産ラインの再構成には時間やコストがかかり、市場の急な変化にすぐには対応できません。さらに、カスタマイズ製品の生産には適しておらず、多様化する顧客ニーズに応えるのが難しい点がデメリットです。
デメリット3:不良品発生時のリスク
ライン生産方式では、一つの工程で問題が発生すると、その影響が次の工程に波及し、大量の不良品が生じる可能性があります。問題の発見が遅れると、被害はさらに拡大してしまうでしょう。また、不良品の発生源を特定し修正するためには、生産ラインを一時停止せざるを得ない場合もあり、その結果として生産効率の低下や納期遅延といった二次的な問題を引き起こすリスクも高まります。
デメリット4:高い初期投資コスト
ライン生産方式を導入する際には、専用の機械設備や自動化システムへの多額の投資が必要です。このため、初期段階では特に中小企業にとって大きな負担となることが多いです。また、技術の進歩や市場の変化に合わせて生産ラインを更新する場合、再度コストが発生します。投資を回収するには一定の生産量と時間が必要であり、需要が不安定な場合は、リスクがさらに高まります。
セル生産方式のデメリット
セル生産方式のデメリットには、以下のようなものがあります。
デメリット1:高い育成コスト
セル生産方式では、作業者が複数の工程を担当するため、幅広いスキルや知識が必要です。そのため、新人育成には多くの時間とコストがかかる点が課題です。また、技術の進歩や製品変更に対応するため、継続的なトレーニングが不可欠であり、常にスキルアップが求められます。さらに、熟練作業者が離職した場合、企業にとっては大きな損失です。人材の定着や技能の継承にも別途投資が必要であり、結果的に育成コストがさらに増加します。
デメリット2:作業の属人化
セル生産方式では、作業者の技能や経験に強く依存するため、作業が属人化しやすい点がデメリット。特定の熟練作業者に頼りすぎると、その人が不在の場合、生産性の低下や一定の品質が保てないといったリスクがあるでしょう。また、ノウハウの共有や標準化が難しくなり、生産システム全体の安定性や一貫性を欠く可能性もあります。属人化は、長期的には組織の柔軟性や成長を阻む要因となるため、早期の対策が重要です。
デメリット3:大量生産に不向き
セル生産方式は少量多品種生産に適している反面、大量生産には向きません。各セルの生産能力には限界があり、需要が急増した際に短期間で生産量を増やすことが難しいのがその理由です。
セル生産方式では、一つの製品を完成させるまでに多くの工程を担当するため、ライン生産方式のように一つの作業に集中する方式に比べて、生産時間が長くなります。このため、単位あたりのコストが高くなり、大量生産時にはコスト効率が悪くなりがちです。
セル生産方式で生産量を増やすには、作業者の増員や設備の追加が必要です。こうした変更は時間とコストを伴うため、急な生産増加への対応は難しいでしょう。
デメリット4:習熟度による生産性の差
セル生産方式では、作業者の技能や経験が生産性に大きく影響します。熟練作業者と新人の間で、生産性や品質に差が出ると、生産計画の立案が複雑化し、納期管理が難しくなるでしょう。また、このような差が生じることで、作業者間に不公平感が生まれ、チームの士気低下につながる恐れもあります。さらに、特定の高スキル作業者に依存することで、人材の偏りや固定化が進み、組織の柔軟性が失われる点もデメリットです。
生産スケジューラと生産方式の相性
生産スケジューラは、製造現場における生産計画を効率化し、リソースの最適配置を行うためのツールです。ライン生産方式とセル生産方式のそれぞれにおいて、生産スケジューラは異なるメリットを発揮します。
ライン生産方式との相性
生産スケジューラは、ライン生産方式の特徴を最大限に活かせるシステムです。ライン生産方式は、工程が順序立てて配置されており、各工程が密接に連携するため、生産全体を一括で管理しやすいという特徴があります。生産スケジューラは、この連携を効率化するために、各工程の作業時間や資源の利用状況を考慮し、最適なスケジュールを提供します。
- 工程間の同期:各工程の処理時間を調整し、スムーズに連携できるよう最適化します。
- 段取り替え時間の短縮:類似製品をまとめて生産することで、段取り替えの時間を短縮し効率を向上
- 納期管理:受注情報と生産能力を基に、納期を守りつつ効率的な生産順序を決定
- 資源の最適配分:人員や設備を適切に配分し、ラインの稼働率を向上
セル生産方式との相性
生産スケジューラとセル生産方式は、柔軟性と効率性のバランスを取れる点で非常に相性が良いです。セル生産方式の特徴である多品種少量生産や作業者の多能工化に対して、生産スケジューラは以下の点で効果的に機能します。
- 作業割り当ての最適化:作業者のスキルや経験を考慮して適切に割り当て、生産性を向上
- 柔軟な生産計画:需要変動や急な注文に対応し、セルごとの生産能力を考慮して調整
- リソース管理:人員や設備を最適化し、残業や空き時間を減らして効率化
- 納期管理:多品種生産の納期を管理し、優先度の高い製品を適切に生産
- データ分析と改善:生産データを収集・活用し、計画調整や改善提案を支援
セル生産方式の柔軟性を活かすためには、スケジューラにも一定の柔軟性が必要です。作業者の判断を尊重しつつ、全体の最適化を図るバランスが重要となります。また、作業者の習熟度の差や属人化といった課題に対応できる機能も求められるでしょう。
適切に設計された生産スケジューラを導入することで、セル生産方式の長所を最大限に活かしながら、短所を補い、効率的で柔軟な生産システムを構築できます。
おわりに
ライン生産方式とセル生産方式は、製造業で広く使われており、それぞれに異なる特性があります。ライン生産方式は、生産ライン上で品物が移動しながら加工が進む方式で、セル生産方式はL字型やU字型のラインを使って、セル単位で作業を進めます。初期コストや需要変化への対応速度などに違いがあるため、自社や製品に合った方式を選択することが業務効率化のポイントです。
どちらの方式でも、生産計画の効率化やリソースの最適化には、生産スケジューラの導入がおすすめです。アスプローバの生産スケジューラは、複雑な生産計画を自動化し、属人的な負担を軽減します。計画の立案を迅速かつ正確に行うだけでなく、リソースを適切に配分します。
具体的な業務改善事例については、以下ページでご紹介しています。業務効率化をお考えの方はぜひご覧ください。

コラム編集部

最新記事 by コラム編集部 (全て見る)
- 納期管理:生産スケジューラの活用 - 2025年4月14日
- スケジューリング技術の応用による生産性の改善 - 2025年4月14日
- Lean Manufacturing~生産スケジューラの活用で最適な生産を - 2025年4月14日