MESシステム~生産スケジューラ連携でPDCAサイクルを最適化
2025.04.09A0 生産管理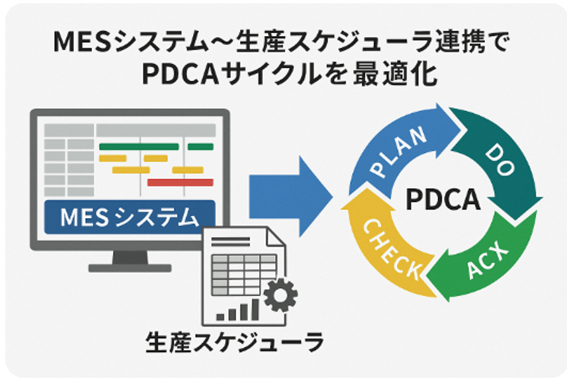
現場での生産管理は、日々の業務を円滑に進めるために重要な役割を果たします。特に、MESシステム(Manufacturing Execution System)は現場の実績データをリアルタイムで取得し、各工程の詳細な管理や最適化を可能にするツールとして注目されています。本記事では、MESシステムの基本的な仕組みや、その活用方法、さらには生産スケジューリングとの連携について解説します。
MESシステムの基本と役割
MESシステムは、工場内での製造プロセスにおける各種データを収集し、リアルタイムでモニタリングする仕組みです。これにより、各工程の進捗や稼働状況、品質に関する情報を即座に把握できます。たとえば、作業開始から完了までの時間や、使用した資材、作業員のパフォーマンスなどがデータとして記録され、次の工程へのフィードバックとして活用されます。
また、MESシステムは、計画と実績のギャップを明らかにし、計画の見直しや改善策の立案をサポートします。現場の生産状況が即座に反映されるため、計画に対する実績の乖離が発生した場合でも、すぐに対策を講じることができます。
現場実績データと生産プロセスの最適化
MESシステムの大きな特徴は、現場実績データをリアルタイムで取得できる点です。これにより、各工程の進捗状況や設備の稼働率、品質の変動などを把握することができます。こうしたデータは、現場の作業効率の向上や不具合の早期発見につながり、結果的に全体の生産プロセスの最適化に寄与します。
たとえば、特定の工程で作業が滞っている場合、その原因を迅速に特定し、必要なリソースの再配置や工程の見直しを行うことが可能です。これにより、ムダな待ち時間や手戻りを減らし、スムーズな生産活動を実現します。
生産スケジューラ連携によるPDCAサイクルの強化
現場での改善活動は、計画(Plan)、実行(Do)、評価(Check)、改善(Act)のPDCAサイクルに基づいて進められます。MESシステムと生産スケジューラの連携により、現場で収集されたデータを基に、PDCAサイクルを迅速に回すことができます。生産スケジューラの活用は特に以下の点で重要です。
- ボトルネックの特定
各工程の中で、作業の停滞や遅延が発生するポイント、すなわちボトルネックを見逃さずに把握することが求められます。ボトルネックを最大限に活用することにより工場全体のスループットが向上します。 - 計画と実績のギャップ
計画段階では理想的なスケジュールが立てられますが、現場の状況は予測と異なることが多く、MESシステムの活用によりそのギャップを把握し、生産スケジューラが迅速に計画を見直します。 - トラブル時などにおける計画変更
急な設備トラブルや人員の不足など、予測できないトラブルが発生した場合に、計画を柔軟に変更するのが難しいケースがあります。MESシステムはこれらの状況をリアルタイムで把握し、生産スケジューラが、即座に計画見直します。
まとめ
MESシステムは、現場の実績データを活用し、生産プロセスの最適化を実現するための強力なツールです。現場での課題である計画と実績のギャップやボトルネックの特定、情報共有の不足などに対し、迅速かつ柔軟な対応が求められる中で、MESシステムと生産スケジューラの連携は非常に有効な手段となります。特に、PDCAサイクルを強化することで、現場の改善活動が効率的に行われ、全体の生産性向上に寄与します。これらの点を理解し、日々の業務に取り入れることで、生産管理の現場はさらに安定し、効率的な運営が期待できるでしょう。

コラム編集部

最新記事 by コラム編集部 (全て見る)
- S&OP(Sales and Operations Planning)~生産スケジューラ連携 - 2025年4月9日
- 在庫管理:ムダを削減し、欠品を防ぐ最新手法 - 2025年4月9日
- MESシステム~生産スケジューラ連携でPDCAサイクルを最適化 - 2025年4月9日