MPSで生産計画を効率化!実施のポイントを解説
2024.10.15A0 生産管理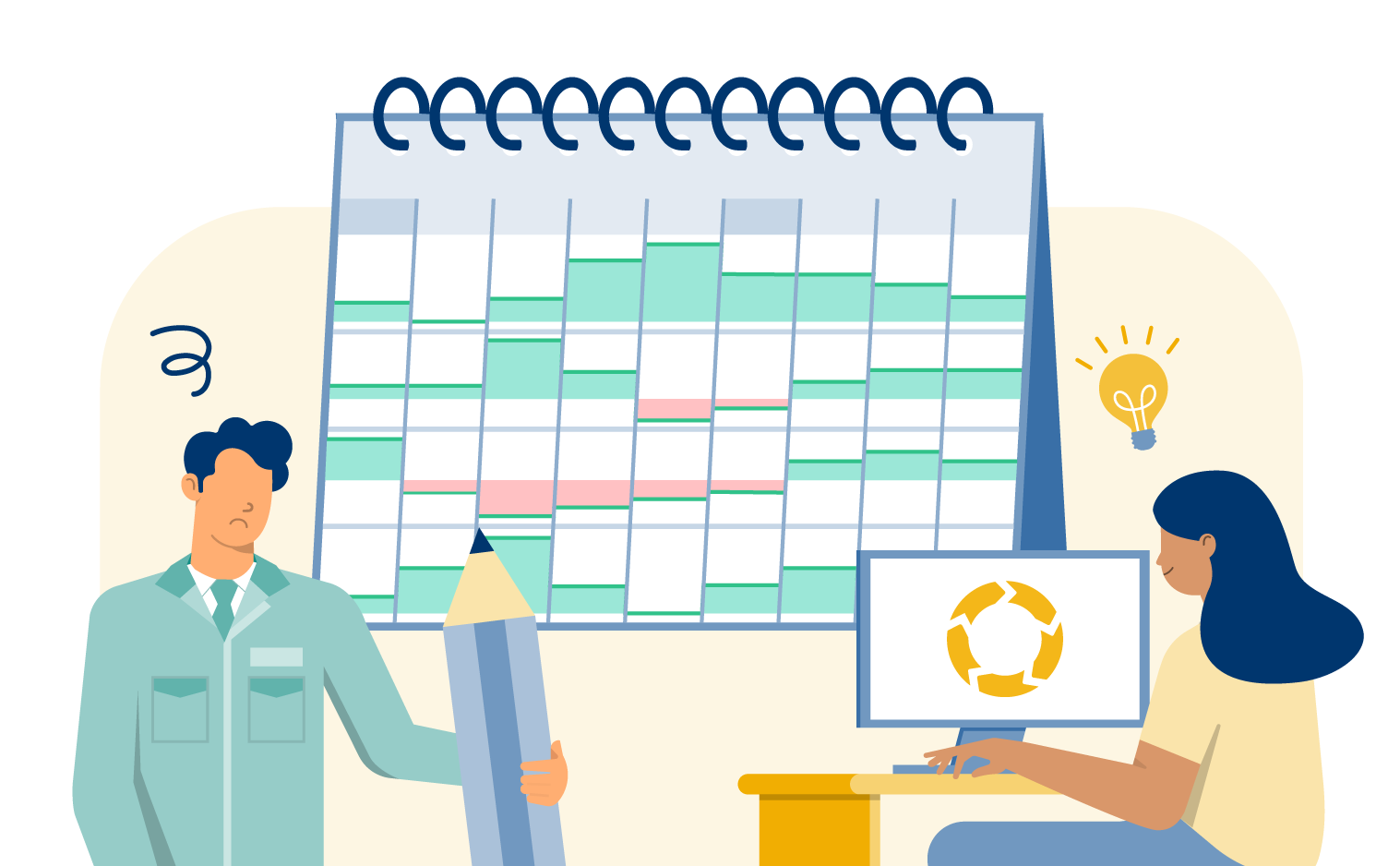
製造業の現場では、日々変化する需要に対応しながら効率的な生産を維持することが課題となっています。この課題を解決するツールとしてMPS(Master Production Schedule)があります。本記事では、MPSの意味や役割、効果的な使い方などを紹介します。
【目次】
■製造現場の効率化を実現するMPSとは
■生産管理におけるMPSの課題
■MPSの実施方法
■MPSを活用して業務効率を最大化する方法
■MPSと生産スケジューラ連携のメリット
■まとめ
製造現場の効率化を実現するMPSとは
MPSとは何か、その定義や重要性、生産計画との違いを紹介します。
MPSとは何か?その定義と役割
MPSは「Master Production Schedule」の頭文字で、日本語では「基準日程生産計画」と訳されます。簡単に言えば、ある製品をいつ、どれだけ生産するかを決める計画のことです。MPSの目的は、労働力や機械、材料資源などの製造リソースを最適に配分して生産をスムーズに進めることにあります。受注数に対応できない事態を回避したり、需要に合わせた先行生産を行ったりなど、生産計画の効率化に役立ちます。
なぜMPSが重要なのか?
MPSは、生産過程における無駄を最小限に抑えつつ効率的な生産を実現できるため、製造業で重視されています。
たとえば、市場の需要を上回る生産は過剰在庫を生み出すため、保管や管理コストの増加につながります。一方、生産が需要に追いつかない場合は顧客のニーズを満たせないため、満足度の低下を招く恐れがあります。MPSを活用することで、このような需給バランスの最適化が図れます。
MPSと生産計画の違い
MPSは生産計画の一種ですが、MRP(Material Requirement Planning)といった他の生産計画とは異なる特徴があります。
MRPは日本語だと「資材所要計画」と訳され、必要となる資材や部品をいつまでにどれくらい必要かを決める計画です。MPSが生産活動全体という広い視点で管理を行っているのに対して、MRPは「資材」の調達や管理の計画を行います。MPSが製品レベルの計画を立て、MRPは部品レベルの計画を立てると考えるとイメージしやすいでしょう。
生産計画では通常、MPSを先に作成し、それに基づいてMRPを立てるという順序で行われます。MPSとMRPが互いに連携し合うことで、効率的な生産管理につながります。
生産計画の種類 | 特徴 |
---|---|
MPS | 基準日程生産計画。生産活動全体の計画や管理の計画を行う。 |
MRP | 資材所要量計画。MPSより範囲は狭く、資材の調達や管理の計画を行う。 |
生産管理におけるMPSの課題
MPSは生産管理に大きな利点をもたらしますが、実際の運用では様々な課題に直面することがあります。ここでは、MPSを導入・運用する際に注意すべき主な課題について見ていきましょう。
計画の柔軟性不足
まず挙げられるのが、計画の柔軟性不足です。MPSは生産計画を幅広く管理するため、詳細かつ複雑な計画立案を必要とします。そのため、市場の動向や顧客の要望による納期変更など、予測不能な変動に柔軟に対応するのが難しくなっています。急な大口注文が入った場合に既存の計画を迅速に調整できないと、貴重なビジネスチャンスを逃してしまう恐れがあります。
データの正確性
MPSを正確に立てるには、最新で正確なデータが必要不可欠です。しかし、実際の現場ではデータが古かったり、誤りがあったりすることがままあります。その結果として、計画の精度が低下して生産効率が悪化してしまいます。たとえば、在庫数が実際と異なっていると、必要な部品が不足して生産が停止したり、顧客の要望に対応できなかったりとトラブルにつながります。
ERPや生産管理パッケージの制約
多くの企業が利用しているERPや生産管理システムには、在庫管理やスケジュール管理など、ある程度決まった機能があります。しかし、実際の現場はより複雑で、システムの機能だけでは対応しきれないことも少なくありません。そのため、システムとは別に管理表を作成したり、手作業で調整したりする必要が生じ、結果的に作業が増えてしまうケースも発生します。
需給計画の難しさ
MPSの基本は「いつ、何を、どれだけ作るか」を決めることです。これを決定する際には、市場の需要を考える必要があります。しかし、単に需要予測と言っても実際には難しく、予測が外れて想定よりも多い、少ないという結果で在庫の過不足が生じることは珍しくありません。余剰在庫を抱えると管理や廃棄などのコストがかかるため、できるだけ余分な在庫を抱えたくないという悩みは生産計画につきものです。だからと言って在庫の数に余裕がないと欠品を引き起こし、販売機会の損失となってしまいます。
生産能力の限界
生産能力の限界も、MPSの運用を難しくする要因の一つです。設備や人員の生産能力を超えた計画を立ててしまうと、生産ラインの負荷が偏ってしまいます。その結果、生産効率が低下して計画通りに進行できなくなってしまいます。納期遅れや品質低下といった問題を引き起こす原因になり得るため、計画の段階でリソースを適切に配分する必要があります。
業務の属人化
生産計画や管理が特定の担当者に依存している場合、その担当者が何らかの理由で不在になった際に、業務が停止するリスクがあります。このような事態を避けるためには、業務の見える化と標準化が大切です。仕事の手順書を作ったり、複数の従業員にスキル面の教育を行ったりするのが効果的です。
MPSの実施方法
ここでは、MPSの基本的な流れと、実施する際の注意点を紹介します。
MPS実施の基本的な流れ
生産計画は、大きく3つの段階に分けて考えます。それぞれ「大日程計画」「中日程計画」「小日程計画」と呼ばれ、長期から短期へと徐々に具体化していくのが特徴です。まず「大日程計画」。これは3ヶ月から1年程度の長期計画で、需要予測を基に立案します。年度単位で考えることが多く、1〜3ヶ月ごとに見直すのがポイント。将来のリソース確保も、この段階で検討します。
次に「中日程計画」。1〜3ヶ月程度の中期計画で、実際の受注状況を踏まえて立案します。製品ごとの生産量や、外注・在庫計画などを決定。1週間から1ヶ月ごとに見直すことで、現場の状況に柔軟に対応できます。
最後は「小日程計画」。1週間から1ヶ月程度の短期計画で、日々の作業レベルまで落とし込みます。品目、数量、完了日などを明記した詳細な作業指示書を作成するのが特徴です。
この3段階アプローチを意識することで、長期的な目標から日々の具体的な作業まで、一貫性のある生産計画が立てられます。また、各段階で定期的に見直すことで、市場の変化や予期せぬトラブルにも柔軟に対応できるでしょう。
MPSを成功させるための作成ポイント
MPSを成功させるには、正確なデータの収集と分析が大切です。
まず、データ収集の正確さが重要です。需要予測や生産計画に必要な情報を、間違いなく集める必要があります。また、集めたデータを正しく分析し、それを生産計画に反映させることも大切です。
さらに、リアルタイムでのデータ活用も重要です。生産現場の状況をリアルタイムで把握し、問題があればすぐに対応できるようにします。このリアルタイムデータを分析し、必要に応じて生産計画を変更することで、より効率的な生産が可能になります。
MPS実施における注意点
MPSを実施する際には、いくつかの注意点があります。 まず、データの正確性と一貫性を保つことが重要です。需要予測や生産計画に必要なデータを正確に集め、一貫して管理する必要があります。 また、品目の管理も大切です。各製品の生産能力や需要予測、在庫状況などをしっかり把握し、管理することが求められます。
MPSを活用して業務効率を最大化する方法
MPSを上手に使えば、生産管理の効率が大きく上がります。ここでは、MPSの基本的な使い方から応用例、そして実際の成功事例まで見ていきましょう。
MPSの活用方法:基本から応用まで
MPSの基本は、製品ごとの需要予測に基づいて生産計画を立てることです。現在の在庫量と受注残を考慮し、必要な生産量を算出します。そして、自社の生産能力を考慮しながら、具体的な生産スケジュールを作成します。この生産計画に基づいて、必要な原材料の調達計画(MRP)も立てます。
MPSの応用では、過去の販売データを詳細に分析し、より精度の高い需要予測モデルを構築できます。また、生産設備の稼働状況をリアルタイムに把握し、生産スケジュールを柔軟に調整することも可能です。グローバル展開している企業では、複数の工場間で生産を最適化するため、グローバルなMPSを立てることも有効です。さらに、顧客の注文変更に柔軟に対応するため、短期的なMPSの変更を行うことで、より顧客満足度の高い生産体制を構築できるでしょう。
業務効率を最大化するためのMPS活用事例
ある工場では、欠品や納期遅れを防ぐために生産計画を前詰めにしていました。しかし、偏ったスケジュールによって週の前半と後半で作業者の負担に大きく差がある、それに対する従業員の不満、残業コストなど様々な問題が発生。この課題を解決するために、MPSの段階で「負荷と量の平準化」に取り組みました。
具体的には、製品ごとの生産数や在庫の平準化で欠品を防ぎ、機械に対しては日毎の負荷を平準化することで生産の集中を避けました。結果として、安定した生産計画が実現し、計画変更の頻度が減少。無駄な調整や作業負荷の偏りが減少したことで、作業員の満足度が向上しました。 このように、MPSを効果的に活用することで、製造現場の業務効率を大幅に向上させることができます。
MPSと生産スケジューラ連携のメリット
まず、MPSと生産スケジューラの基本的な連携方法について説明します。MPSは通常、月単位や週単位の大まかな生産計画を立てるのに使用されます。一方、生産スケジューラは日々の詳細な生産スケジュールを管理します。これらを連携させるには、MPSで立てた計画を生産スケジューラに取り込み、より細かい単位で生産計画を立てる必要があります。
基本的な連携方法の例として以下の流れがあります。
(1)データや情報を準備する まず、MPSの全体的な計画や製品の製造方法、設備や資材の情報など、生産計画に必要な情報・データを準備します。このデータは生産スケジューラに必要であり、計画の精度を向上させるために大切です。
(2)MPS計画の取り込み 次に、MPSの計画、生産数量、納期、必要なリソースなどの情報を生産スケジューラに取り込みます。生産計画が具体的なスケジュールとして生産スケジューラに反映されます。
(3)生産スケジューラの設定 生産スケジューラでは、MPSから取り込んだデータを基に実際の生産スケジュールを作成します。この際、設備の稼働制約や作業員のシフトなど、より詳細なスケジュールを考慮します。
(4)フィードバック 生産スケジューラで作成した詳細計画をMPSにフィードバックし、必要に応じて調整を行います。
連携のポイントは、データの正確性と更新頻度です。MPSと生産スケジューラ間でやり取りされるデータに誤りがあると、生産計画全体に影響を及ぼす可能性があります。また、市場の需要変化や生産ラインの状況変更などに応じて、適切なタイミングでデータを更新することが重要です。
MPSと生産スケジューラの連携によって得られるメリットとして、まず第一に生産計画の精度が向上する点が挙げられます。MPSで立てた大まかな計画を、生産スケジューラでより現実的かつ詳細な計画に落とし込むことで、生産能力と需要のバランスを取りやすくなります。
また、リードタイムの短縮も期待できる点です。MPSと生産スケジューラの連携により、生産の全体像を把握しつつ、日々の生産調整を迅速に行えるため、生産の遅れを最小限に抑えられます。
さらに、在庫管理の最適化にもつながります。MPSで立てた計画を基に、生産スケジューラで細かい生産タイミングを調整することで、必要以上の在庫を持たずに済むようになります。
他にも、生産ラインの稼働率向上も見込めます。MPSで立てた計画を生産スケジューラで細分化することで、各生産ラインの能力を最大限に活用するスケジュールを組めます。設備の遊休時間を減らし、生産効率の向上につながるでしょう。 このように、MPSと生産スケジューラの連携は、製造業の効率化と競争力強化に大きく貢献します。
MPSを正確に立てられるSolver
これまでのMPSは生産能力の限界を考慮できませんでしたが、そこに焦点を当てたのがAsprovaのオプションであるSolverです。
Solverは製造現場のキャパシティを考慮しながらMPSを自動的に最適化します。具体的には納期遅れや欠品を起こさないように日々の生産数を最適化し、負荷の平準化と量の平準化まで行います。具体的には、以下のようなことが実現できます。
- 需要に対して欠品させない
- 安全在庫を確保する
- 品目ごとの生産数量を平準化
- 期間内の日ごと・資源ごとの負荷を平準化
- 資源間の負荷平準化
- 残業時間最小化
- 段取り最小化
ソリューションセミナーやナレッジセンターで詳しい解説をしていますので、MPSから最適な生産計画を立案したい方はご確認ください。
まとめ
製造業において、MPS(基準日程生産計画)は効率的な生産管理の要となります。適切なMPSの運用により、需要予測の精度向上、在庫の最適化、そして生産リードタイムの短縮が可能となります。さらに、MPSと生産スケジューラを連携させることで、その効果は倍増します。
しかし、従来のMPSでは生産能力の限界を十分に考慮することが難しいという課題がありました。この問題を解決し、より正確なMPSを立てるためのソリューションとして、生産スケジューラ「Asprova」がおすすめです。
Asprovaは、高度なアルゴリズムを用いて生産能力を考慮しながらMPSを最適化します。リアルタイムスケジューリング機能により、常に最新の状況に対応した生産計画を提供し、高精度な負荷計算で最適な生産スケジュールを実現。多品種少量生産にも柔軟に対応し、ボトルネックの特定と解消により生産効率を最大化します。
製造業や生産計画のお悩み解決につながるツールとして、導入を検討してみてはいかがでしょうか。生産スケジューラ導入によって具体的にどのような業務改善が実現したのかはこちらのページをご確認ください。

コラム編集部

最新記事 by コラム編集部 (全て見る)
- 困ったこと35~作業指示と無関係に作業する人がいて困った - 2025年4月23日
- 困ったこと35~一生懸命やっているのに、理解してもらえなかった - 2025年4月23日
- 困ったこと35~「何でもできる」と思い込んでいる人に困った - 2025年4月23日