工程管理:生産スケジューラと連携して納期遅れを防止
2025.04.22A0 生産管理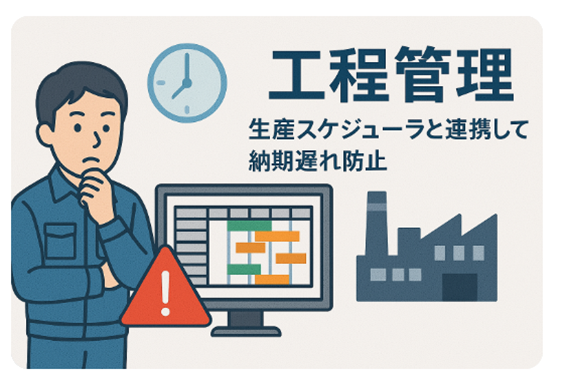
工程管理とは
1.1 工程管理の目的はQCD(Quality, Cost, Delivery)
工程管理とは、製品が完成するまでに通る各生産工程のQCD、つまり、品質・コスト・納期を総合的に管理し、生産効率を高めるための業務です。
- 品質 : 製品の品質を一定に保ち、クレームや再加工を防止します
- コスト : 作業時間や段取りのムダを削減し、コストを最小化します
- 納期 : 各工程の滞りをなくし、生産のスムーズな流れを維持し、納期遅れを防ぎます
1.2 管理項目の具体例
工程管理で重点的に見るべき指標は次の通りです。
- 標準作業時間:作業を効率的に進めるための基準となる時間
- 段取り時間:機械の切り替えや工具交換などにかかる時間
- 仕掛品在庫:各工程間の中間在庫の量
- 設備稼働率:生産設備の稼働状況
これらの数値を継続的に把握・分析し、必要に応じて改善を図ることが求められます。
工程管理のメリット
適切な工程管理を行うことで、以下のような多くのメリットが得られます。
-
生産の見える化 : 進捗状況が可視化されることで、どの工程で遅れや滞りが発生しているかをすぐに把握できます。これは現場の改善活動にとって非常に重要な情報です。
-
リードタイムの短縮 : 作業の重複や段取りのムダを排除することで、全体のリードタイム(受注から出荷までの時間)を短縮できます。これは顧客満足度の向上にも直結します。
- 品質の安定 : 工程ごとのチェックポイントを設けることで、不良品の発生を早期に抑えることができます。結果的に、後工程への影響を最小限に抑え、トータルの品質を向上させます。
実務での工程管理の進め方
まずは現場をよく観察し、各工程でどれだけ時間がかかっているか、ボトルネックはどこかを明らかにします。同時に、作業時間や稼働率などのデータを継続的に記録・蓄積していきましょう。
作業ごとの標準作業時間を明確にし、それを基準として作業のバラつきを抑える取り組みが重要です。また、段取り作業を簡素化・短縮することで、機械の停止時間を減らし、作業負荷の平準化にもつながります。
生産スケジューラは、さまざまなシナリオをシミュレーションできる点も大きな特徴です。たとえば「A工程の機械が故障した場合」「急な大口注文が入った場合」など、現実に即した柔軟な対応力が求められる場面で納期厳守に大きな効果を発揮します。
生産スケジューラによる工程管理の高度化
生産スケジューラとは、製造業における工程の流れや資源の割り当てを最適化するためのITツールです。具体的には、工程間のタイミング調整や、機械・人員の作業計画を自動的に立案・修正します。
工程ごとに作業時間や必要な資源が異なるため、連携がうまくいかないと停滞が発生します。生産スケジューラを用いることで、各工程の情報をリアルタイムで把握し、最も効率的な順序とタイミングで作業を配分できます。
例えば、ある工程の遅延が生じた場合でも、スケジューラが他工程への影響を分析し、代替案を提示します。これにより、手作業では困難だった複雑な判断をスピーディに行うことができます。
各工程の標準作業時間や段取り時間をもとに、最適な作業割り当てやライン構成を導き出すことができます。工程管理と生産スケジューラを組み合わせることで、より高度な生産性向上が可能となります。
まとめ
工程管理は、生産現場の効率と品質を支える基盤となる業務です。各工程の作業時間、段取り、負荷、進捗、品質といった情報を的確に把握し、継続的に改善を図ることで、企業全体の競争力を高めることができます。また、生産スケジューラのようなツールを活用すれば、より精度の高い計画と柔軟な現場対応が可能になります。工程管理を正しく理解し、実践することは、生産管理担当者にとって必要不可欠なスキルです。
最適化AIを搭載した生産スケジューラに関しては、こちらをご覧ください

コラム編集部

最新記事 by コラム編集部 (全て見る)
- MRPの真価を引き出す!生産計画・在庫管理・スケジューラ連携 - 2025年4月22日
- 工程管理:生産スケジューラと連携して納期遅れを防止 - 2025年4月22日
- 段取り時間削減:AI生産スケジューラの活用 - 2025年4月22日