平準化とは?標準化との違い・実現するためのステップや成功のポイントを解説
2024.07.17A0 生産管理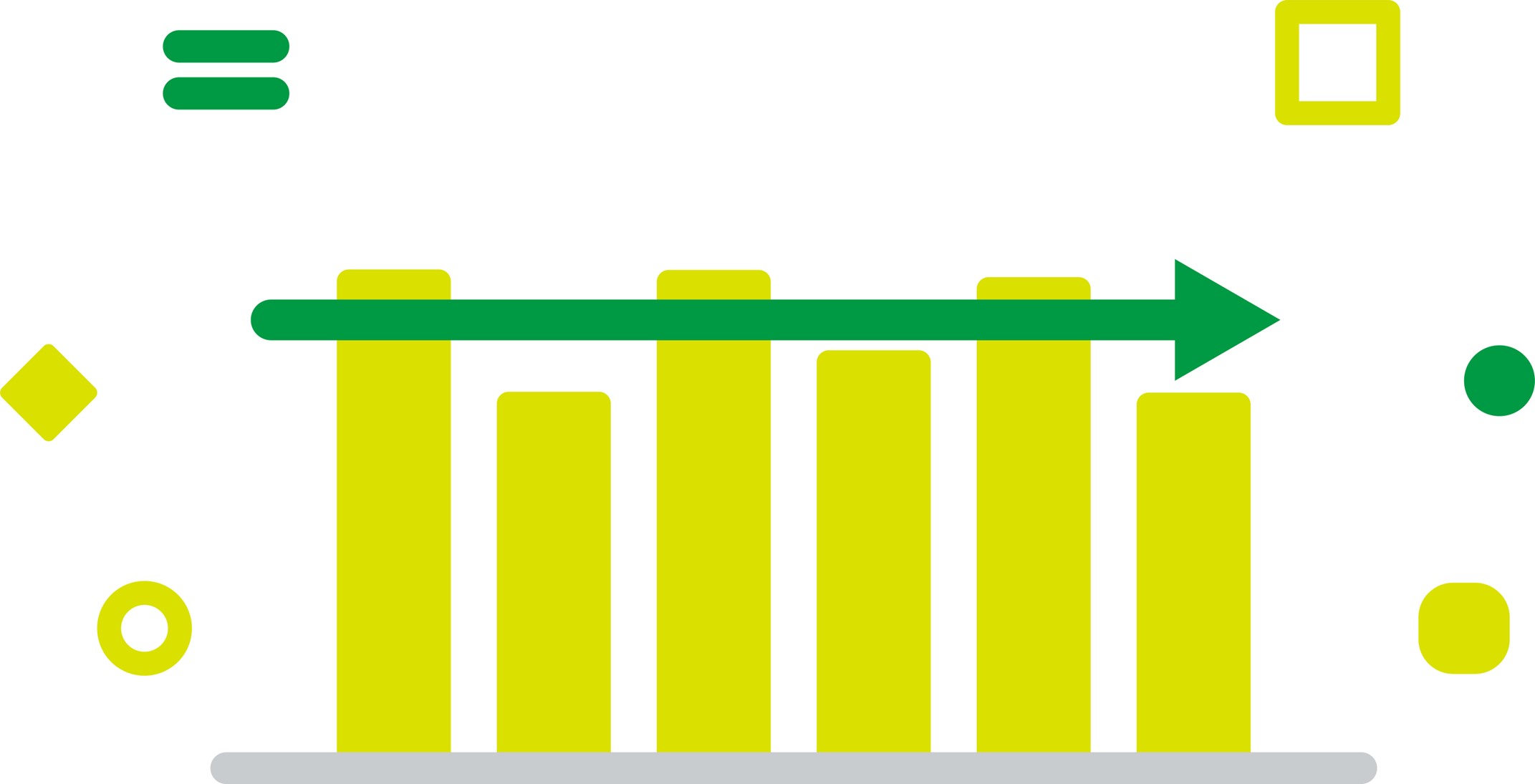
生産管理を語るうえで避けて通れないのが「平準化」です。多品種少量生産が主流の現代の製造業において、効率的な生産を可能にする平準化は重要な技法といえます。この記事では、平準化で得られる恩恵や実現するステップ、成功させるためのポイントを解説します。
【目次】
■そもそも平準化とは
■平準化と標準化は何が違う?
■平準化することで得られる恩恵とは
■平準化を実現するステップ
■平準化を成功させるためのポイント
■平準化における生産スケジューラの重要性
そもそも平準化とは
平準化の一般的な定義は、物事を均一化し、偏りをなくすことです。製造業や物流業においては「生産量や商品・部品種類を平均化すること」や「生産性(リードタイム・コストなど)を揃えること」を指します。現在の製造業では、多品種少量生産が主流となっています。そのため、日ごと月ごとの生産量・生産品目を一定にする「平準化」が必要です。平準化は、大きく分けると「量」と「種類」の2つに分かれます。ここでは、量と種類の平準化が何を意味するのか、さらに詳しく解説します。
量の平準化とは
量の平準化とは、生産数量のばらつきを抑え、一定に保つことを意味します。どんな製品でも日・週・月ごとの注文量にはばらつきが出るものです。そのため、顧客からの注文量をそのまま生産計画に反映させると、ロスが生じやすくなります。たとえば、生産数の最大時に必要な人員を常時確保していると、ピーク時以外で過剰人員が生じます。量の平準化では、ピーク時ではなく月の平均生産数に応じた人員を投入するため、ロスの改善が可能です。量の平準化を行うことで、注文の変化に柔軟に対応できる、バランスの取れた生産計画が立てられます。
種類の平準化とは
種類の平準化とは、生産する製品の種類を平均化することを指します。従来の生産方法では、製品ごとにひとまとまりで生産し、たとえばAの生産がすべて完了してからBの生産に取り掛かります。しかし、種類の平準化では、一定のパターンで異なる種類の製品を繰り返し生産します。例えば、ABCの3種類の製品がある場合、ABACABACのように小ロットに分解して平均的に生産します。この方法には段取り替えの回数が増加するという側面がありますが、その一方で、多品種少量生産に対応でき、過剰在庫のリスクを軽減させることができます。さらに、種類の平準化により1日の生産順序が標準化され、人員や設備を効率的に活用できるため、生産全体の柔軟性が向上します。
平準化と標準化は何が違う?
平準化と似て異なるのが、標準化です。この2つの違いを明確に理解し、それぞれを適切に実施すると見落としの少ない管理計画が立てられます。平準化と標準化の違いについて簡単にまとめると、以下のとおりです。
用語 | 意味 | 内容の詳細 |
---|---|---|
平準化 | 生産量や生産する品目を一定にする作業 |
|
標準化 | ルールを定めて製品の品質を一定に保つこと |
|
平準化は主に、生産量や種類を一定にすることに焦点を当てています。一方、標準化は品質の統一化を目的とするものです。製造業において、高クオリティな製品を効率的に生み出し続けるためには、平準化と標準化の両方が必要です。
平準化することで得られる恩恵とは
製造業の生産管理を平準化することで得られる恩恵は数多くあります。平準化を実践するためには準備や調整が必要です。ここでは、平準化で得られる以下の5つの恩恵を解説します。
- 人件費の削減につながる
- 製品の品質を保てる
- 在庫の適正化につながる
- 生産性の向上が期待できる
- 顧客の要求の変更にも対応しやすい
人件費の削減につながる
生産量を平準化することで、人員計画を立てやすくなり、人件費削減もしやすくなります。平準化していない場合、人員数はピーク時の生産数に合わせがちです。しかし、人員数をピーク時に合わせると生産数が少ない時には余剰人員が発生してしまいます。そこで生産量と人員を一定にする平準化を行えば、無駄な人件費が生じず、コスト削減につながります。
製品の品質を保てる
平準化をすると無理のない生産計画が立てやすくなり、生産工程に余裕が生まれるため、製品の品質を保てるようになります。平準化をしていない場合、繁忙期には残業を増やすなど、人員に無理を強いる計画になりがちです。作業者が過労状態に陥ると、生産する製品の品質低下を招いてしまうかもしれません。また、稼働時間が長くなると設備への負荷も大きくなります。設備が故障すると不良品が発生する可能性も高くなるでしょう。そのため、高品質な製品を作り続けるためには、平準化により余裕のある計画を立てることが有効です。
在庫の適正化につながる
在庫の適正化につながる点も平準化の恩恵の1つです。平準化を行えば、前もって需要を予測し適切な在庫量を計画でき、在庫切れや過剰在庫が防げます。注文量が一時的に増える繁忙期に前もって備えることも可能です。
生産性の向上が期待できる
平準化の 4つ目の恩恵は、生産性の向上です。平準化により、業務量とそれに必要なリソースの調整がしやすくなります。業務フローから無駄な工程を外すことでチーム全体の作業総量が増やせるため、生産性が向上します。無理のない作業ができるようになり、作業者一人ひとりの生産性の低下を防げる点もメリットです。
顧客の要求の変更にも対応しやすい
平準化の 5つ目の恩恵は、顧客の要求の変更に対応しやすい点です。平準化により、在庫やリソースの無駄が排除でき、変化に対応しやすい生産体制を作りやすくなります。平準化されていない生産工程では、追加注文が入った場合、現在生産中の製品の作業が終わるまで顧客を待たせる必要があります。一方、種類の平準化を行うと、顧客の要求に変化があっても迅速な切り替えができ、対応しやすいです。顧客のニーズに柔軟に応えられるため、顧客満足度を高めることにもつながります。
平準化を実現するステップ
平準化を実現するためには、段階的な取り組みが大切です。実現までに必要なステップを1つずつ確認しておけば、効率的に平準化を進められます。ここでは、平準化実現のためのステップとして以下の5つを解説します。
- 平準化したい工程全体を分析する
- 分析した工程を分類
- ムダ時間の削減を徹底する
- 内段取りの時間を短縮する
- 外段取り時間の見直し・改善を行う
平準化したい工程全体を分析する
初めに、平準化したい作業内容の全体を分析・可視化します。多品種生産のラインでは、種類の切り替えに伴う段取り時間が多くなる傾向があります。工程全体を分析することで、段取り時間に属する作業内容や時間の把握が可能です。作業を分析すると、想定作業時間以外に要している時間が多くあることに気づくはずです。細かい点でもタイムロスになっている状況はすべて書き出し、可視化しましょう。
分析した工程を分類
次に、可視化した作業内容を内段取り・外段取り・ムダ時間の3種類に分類します。内段取りとは型や工具の交換など、機械の稼働を停止して行う作業を指します。外段取りは次の製品の型の作成など、機械稼働中に並行して行える作業です。定位置にあるはずの部品が見当たらず探す時間など、本作業に含まれない時間はムダ時間に分類します。
ムダ時間の削減を徹底する
そして、前ステップで分類した時間のうち、ムダ時間を削減します。ムダ時間の削減は平準化の過程の中でも初期段階に当たる作業です。整理整頓を改めて徹底するだけで高い効果が得られる場合があります。また、従業員ごとに自己流で行っていた作業のマニュアル化や統一化なども効果的です。基本的な内容であっても指摘される機会がなく、効率の低下を招いていたムダ時間を洗い出せるステップともいえるでしょう。
内段取りの時間を短縮する
4番目のステップは、内段取りの時間を短縮することです。内段取りは機械を停止させる必要のある作業であり、このステップでは「本当に機械を止めないとできない作業か」を検証することが重要です。事前準備やデジタル化を活用することで、一部の作業を機械稼働中に行えるようになる可能性があります。内段取りの時間を短縮すれば、作業フロー全体の時間短縮や生産性の向上が見込めます。特に内段取りの作業は徹底的に見直すことが求められます。また、平準化を実現するためには「内段取りをシングル段取りにする」取り組みが重要です。段取り回数が増加しても段取り時間が増加しなければ、スループットに影響を与えることなく生産性を向上させることが可能です。したがって、内段取りの外段取り化を進めるだけでなく、シングル段取りへの移行も積極的に検討しましょう。
外段取り時間の見直し・改善を行う
内段取りの時間の短縮を行うと、外段取り時間に行っていた作業が間に合わなくなる可能性があります。そのため、最後のステップは外段取り時間の見直し・改善です。具体的な施策として、ヘルプ要請がしやすい体制を作る、動線を整備するなどの方法が挙げられます。
平準化を成功させるためのポイント
組織内で変化をもたらす試みをするのは簡単なことではありません。平準化を進める際も、関係する従業員全体の理解を求めながら行う必要があります。ここでは平準化を成功させるためのポイントを4つ解説します。
- 計画はスモールスタートを心がける
- 生産計画を柔軟に立てる
- 従業員の力量を踏まえて平準化を進める
- 平準化すること自体を目的に据えない
計画はスモールスタートを心がける
平準化成功のための1つ目のポイントは、スモールスタートを心がけることです。平準化の効果を得るためには、検証・改善を繰り返す必要があります。スモールスタートであれば、失敗した時のリスクを抑えつつ、計画の軌道修正がしやすいです。また、関わる人員が少ないため共通理解が早くなるメリットもあります。一部の製品で平準化の成功を収めた後、段階的に組織全体の業務へ浸透させていくと良いでしょう。
生産計画を柔軟に立てる
平準化の2つ目のポイントは、生産計画を柔軟に立てることです。平準化を行う際には、需要の変動に対応することが重要です。具体的には、現時点での需要を正確に予測し、その予測に基づいて生産計画を立てることが求められます。 また、定期的な見直しも大切です。生産計画を立てた時点と現状では、顧客からの注文量が変化している可能性もあります。生産計画は短いサイクルで作成し、常に需要に合わせられる体制を整えましょう。
従業員の力量を踏まえて平準化を進める
平準化を進めるためには、従業員ごとの技量の差が出ないようにすることも大切です。従業員の力量を踏まえた無理のない生産計画を立てるようにしましょう。また、従業員への教育の徹底やマニュアル整備などの対策も効果的です。誰が担当しても同じ品質・スピードで作業できるよう明確なルールを作れば、作業の属人化を防げます。
平準化すること自体を目的に据えない
4つ目のポイントは、平準化自体を目的に据えないことです。平準化の実施に固執すると、現状に即さない施策を取り入れ、コストが増大したり生産品質が下がったりする逆効果になりかねません。平準化のゴールは、人員の最適化や在庫の適正管理によりコスト削減・品質向上を達成することです。企業や業種によって適した施策は異なるため、自社にとって最善な施策を見つけ出すことが最も重要です。施策を検討するうえで、平準化の当初の目的を忘れないようにしましょう。
平準化における生産スケジューラの重要性
製造業における平準化は、「生産量や商品・部品種類を平均化すること」や「生産性(リードタイム・コストなど)を揃えること」を意味します。平準化を成功させるためには、現場の実情に即した生産計画を立て、検証と改善を繰り返していくことが鍵となります。そのために、生産計画の精度と柔軟性を上げることは欠かせません。
平準化の実現に向けた生産計画の立案と管理には、従来の方法だけでは限界があります。特に、多品種少量生産が主流となっている現代の製造業では、より高度な計画策定が求められます。ここで役立つのが生産管理ツールです。こうしたツールの導入によって、計画の精度と柔軟性を飛躍的に向上させることができます。
弊社製品「生産スケジューラ」は、そのようなツールの一例です。このスケジューラは、生産計画を自動化・最適化し、計画策定時間の短縮を実現します。また、生産スケジューラはリアルタイムでの計画修正が可能なため、需要変動や突発的なトラブルにも柔軟に対応できます。これにより、平準化を進めるために不可欠な精度の高い計画策定と、柔軟な対応が可能になります。
多くの企業で導入されている「生産スケジューラ」により、平準化の目標達成に向けた実践的なサポートが得られます。導入事例や具体的な効果については、こちらのページをご確認ください。

コラム編集部

最新記事 by コラム編集部 (全て見る)
- なぜこの2社は計画のブレを最小限にできたのか?精度向上のカギを解説 - 2025年7月2日
- “半日が10分に短縮”も可能に!属人化を脱し、計画作成を効率化した方法とは? - 2025年7月2日
- “なんとなく管理”からの脱却!デンカが語る、見える化による現場改善ストーリー - 2025年7月2日