生産ラインを効率化する設計・レイアウトとは?
2024.11.20A0 生産管理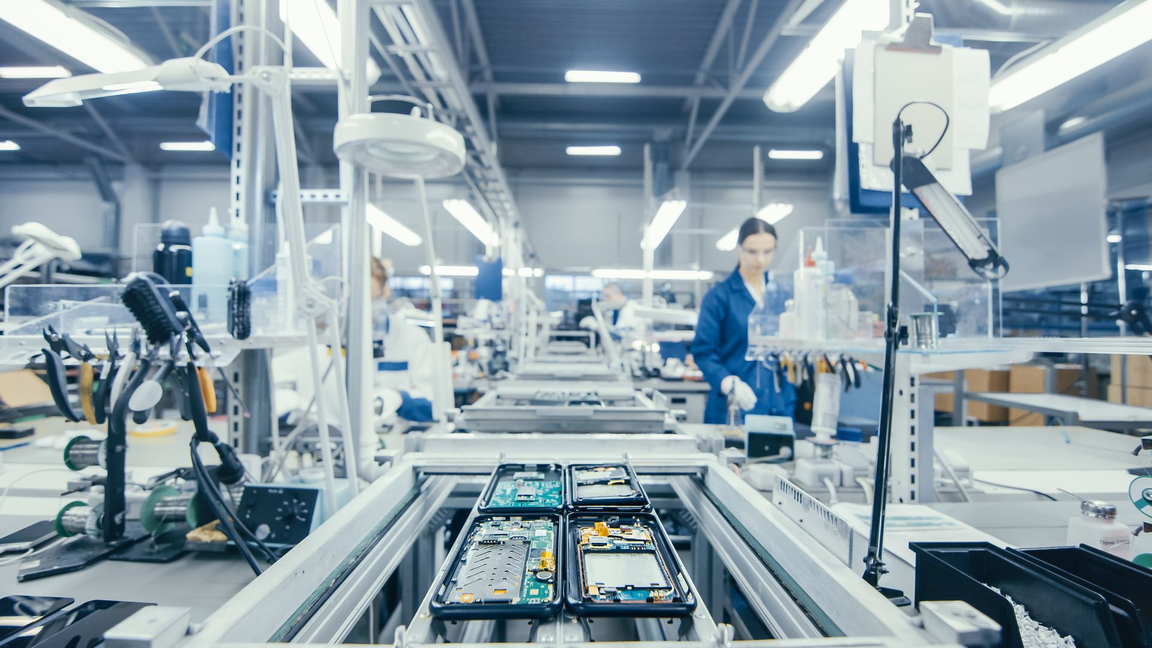
生産現場で製品や部品を製造する時、いかに効率よく稼働させて量産できるかは企業の損益にかかわる大きな要素です。製造業や工場において生産効率を上げるために生まれた生産ラインですが、より効率化する方法はあるのでしょうか?
本記事では、生産ラインの基礎知識をおさらいしながら、効率的な生産ラインに望ましい設計やレイアウトをご紹介しています。
より生産ラインを効率化するための具体的な方法やツールを活用した効率化の手法についても解説していますので、製造業の経営や現場の生産管理に携わる方は、ぜひ業務効率化の参考にお役立てください。
【目次】
■生産ラインとは何か
■生産ラインの設計とレイアウト
■生産ラインの効率化
■生産ラインにおける品質管理とトラブルシューティング
■生産ライン改善の重要性
生産ラインとは何か
生産ラインとは、工場や製造施設において、同じ製品や部品を大量に生産するために行う流れ作業のことです。
製造業では、製品の原材料をもとに人や機械、設備が加工や組み立てを加えて製品を完成させます。
そのため、製品ができるまでには作業者から次の作業者へ作業を渡したり、機械を使って次の作業を行ったりしなくてはなりません。製造業ではそのプロセスを効率化するために、ベルトコンベアを用いてライン上で流れるように作業を進めるのが基本です。見た目の通り、この生産上のラインの様子から「生産ライン」と呼ばれるようになりました。
生産ラインの基本定義と目的
製品や部品を生産するための流れ作業を、ベルトコンベアを用いて行うのが生産ラインです。その目的は、効率的に高品質な製品を大量生産することにあります。
より効率的に大量生産を実現するためには、設備の導入や環境管理、レイアウトの設計や改善を行う必要があります。ラインがよりスムーズに流れるように様々な改善を図り、生産性の向上を目指すのが生産ラインの基本的な考え方です。
生産ラインの歴史と進化
生産ラインが誕生したのは、18世紀後半から19世紀にかけて起こった産業革命以降と言われています。産業革命前までは、労働者を工場の1ヶ所に集めて分業・協業し、手作業によって製造が行われるのが一般的でした。
産業革命以後、工場制機械工業が登場してからは大量生産が本格化します。
1913年にアメリカの自動車メーカー・フォード社は、ベルトコンベアを用いてT型フォードを効率的に大量生産しました。生産時間が大幅に短縮され製品コストも削減されたことから、フォードの大量生産の実現を機に、ライン生産は広く普及していきました。
現代における生産ラインでは自動化が進み、複雑な生産課題も解決できるようになっています。ロボットをラインに並べて作業を自動化できる生産ラインやデータ分析でより効率性の高いレイアウトやプロセスに改善できる高度な機能を持つ柔軟性の高い生産ラインが登場しており、日々進化を続けています。
生産ラインの設計とレイアウト
現場の生産性を高めるには、安全性やコストなどを考慮して、人や設備の適切な配置を考えなくてはいけません。ここからは、効率的な生産ラインを構築するための設計要素とレイアウトの重要性について説明します。
生産ラインの設計要素
生産ラインの主な設計は、レイアウトと工程設計、設備の配置の3要素です。
レイアウトを決める
安全性やコストなどを考慮した適切なレイアウトを決めることが大切です。
工場におけるレイアウトは、装置型工場か組立型工場のどちらかによって大まかなレイアウトが決まります。
装置型工場とは製鉄やセメント製造など、大型の装置を用いて製造する工場です。一度レイアウトを決めると設備配置の変更が難しいため、工場設立初期のレイアウトが肝心となります。
組み立て型とは、名前の通り部品を組み立てて製品を製造する工場です。一部の工程プロセスが止まっても全体の業務が完全に停止するわけではないため、製造型工場に比べてレイアウトの変更が容易です。
製造する製品や配置する設備の大きさに合わせて、適したレイアウトを決定します。
工程設計を見直す
生産ラインにおいて、特定の工程のみ特に時間がかかっている場合や作業効率が悪い工程があると、生産能力の低下を招きます。生産ラインがスムーズに流れるようにするためには、生産性の低い工程(ボトルネック)を解消できるかが重要です。
生産ラインの工程1つひとつを見直し、どのような業務をどんな風に行っているかを確認し、ボトルネックがあれば改善して、ライン全体の生産性が向上するような設計にしなおしましょう。
設備の配置を決める
製造現場の生産ラインのほとんどに、機械や設備が必要です。工程がスムーズなレイアウトはどれか、いくつかのパターンを考えて比較し、実際の配置を決定します。この時、工場の広さや天井の高さを加味して、同じスペースにどのようにラインがあればよいか・機械や設備を配置すればよいかも考慮します。
効率的なレイアウトの重要性
レイアウトが上手くいっていないと、製造ペースが上がらず生産性を低下させる要因になります。また、作業のしにくさを解消するために余計に人員を割いていては、コスト増大にもつながるでしょう。
装置型工場の場合は一度配置したレイアウトを変更するのは困難ですが、組み立て型工場の場合、必要に応じてレイアウトを柔軟に変えられるかを確認した上で設計することが大切です。適切なレイアウトができていると、作業の流れがスムーズになり、スペースの有効活用もできます。
生産レイアウトの種類
生産ラインのレイアウトは、製造する製品や工場の規模によって複数の種類に分けられます。
少量生産に向いたセル型レイアウトや大型の製品を製造するのに適している固定式レイアウトがあります。
ジョブショップ型
同じような機能を持つ機械・設備を1ヶ所にまとめて配置するレイアウトです。製品に合わせて違うサイズの部品を製造する時や組み合わせ部材を作る時など、多品種の製品を少量生産するのに向いています。
ライン型
製造工程に沿って機器や設備、人を配置する方法で、フローショップ型、製品別レイアウトとも呼ばれます。工程の多くを自動化できる一方で、手順の変更や生産量の調整が難しい特徴があります。自動車や加工食品など、ある程度需要が安定した少品種の製品を大量生産するのに向いています。
U字ライン
コンベアでの搬送を用いずに、工程をU字型に配置し、作業者の手が届く範囲に材料や工具が配置される生産ラインです。多品種の製品を少量生産する際に適しています。作業者の定員変更がしやすいことから、生産性と品質を向上させたい際にも採用されるレイアウトです。
セル生産方式
作業員の周りに必要な設備や機器を配置するレイアウトです。作業テーブルの前に1名の作業員が立ち、機器や工具を使って製造するような、小さなスペースで製造が完成する製品を作る際にこの方式を採用します。数名の作業員を配置するU字ラインと区別するため、1名の作業員で行うレイアウトをセル生産方式と呼ぶことがあります。
生産ラインの効率化
生産ラインは、設計とレイアウトさえ決めてしまえば良いわけではありません。企業の利益を向上するためには、生産ラインがより効率的に稼働するにはどうすれば良いかを考え、改善し続けることが重要です。
ここからは、生産ラインを効率化するメリットや重要性、効率化に向けた具体的手法をご紹介します。
効率化の重要性とメリット
製造業では、低賃金や長時間労働による人材不足が慢性的な課題となっています。少ない人手で生産活動を継続し利益を上げるためには、ライン作業の効率化によって経済的・時間的コストを削減しなくてはなりません。
生産ラインを効率化すると、作業時間が短縮されて生産性が向上します。また、業務の「無駄」をなくすことで全体のコストの削減にもつながります。 生産ラインの効率化は、製造現場の経済的・時間的コストを削減し全体の利益を向上させるためにも重要です。
効率化の具体的手法
生産ラインを効率化する方法は複数あります。具体的には、5S活動と工程の見直し、設備の最適化が有効です。
5S活動を徹底する
5Sとは、製造現場の環境を最適化するための考え方です。「整理・整頓・清掃・清潔・しつけ」の5項目の頭文字のSを取ってそう呼ばれます。
必要なもの・不要なものを区別して不要なものを処分するのが「整理」です。備品や工具など生産に必要なものを必要な時にいつでも取り出せるようにするのが「整頓」で、機材のメンテナンスや汚れの掃除を行うのが「清掃」にあたります。
製造現場を常に「清潔」に保ち、ルール「しつけ」を作成することで効率的な環境が整います。
工程の見直し
一連の業務やプロセスの中で、特に効率の悪いボトルネックの部分を見つけたり段取りを見直したりする作業です。ボトルネックになっているところを放置してしまうと、業務スピードや品質が低下してコストの浪費や従業員の負担増加といったデメリットが生じます。
設備の最適化
製造したい製品に適したライン設備になっているかを確認することも大切です。いくら高性能な機械や設備でも、大きさや台数が合わないと作業員が作業しにくくなってしまいますし、稼働までに時間を要する設備の場合、時間的コストをムダにしてしまいます。配置する設備がボトルネックの要因にならないためにも、設備を最適化できるかを見直しましょう。
ツールを活用して効率化を図る
生産ラインを効率化する方法のひとつに、ツールの活用が挙げられます。
製造現場で採用される代表的なツールは以下の通りです。
MES(製造実行システム)
生産ラインの製造工程と連携してリアルタイムで生産状況を監視し、製造プロセスを管理・最適化するシステムです。
生産計画にもとづいた作業スケジュールの設計や管理者への指示出しを行うことができます。
ERP(統合業務システム)
在庫管理や購買、財務管理などを統合し、一元管理して全体の効率向上を目指すツールです。決まった数値の入力や集計などの規則的な業務を効率化できるので、生産管理コストを大きく削減できます。
IoTセンサー
生産ラインにおける機器の状態や生産状況をリアルタイムでモニタリングし、異常を早期に検出できるシステムです。機械や設備にセンサーを取り付けて、蓄積されたデータを様々な情報に変換し生産効率向上を目指します。生産ラインにおいては、イメージセンサーや光センサーなどが使われています。
BI(ビジネスインテリジェンス)ツール
データ分析を通じて製造プロセスの改善点を特定し、意思決定をサポートします。作業員や管理者の経験や勘に依存せず、効果的な改善策を見いだしたい際に有効です。現場の進捗をより把握したり製品別の実際原価を把握したりする機能も含まれます。
生産スケジューラ
人員や設備などのリソースと生産ラインにおける生産量を照らし合わせ、必要なリソースを割り当てられるシステムです。設備や人員の資源能力を最大限に引き出す計画を提案します。
生産ラインにおける品質管理とトラブルシューティング
適切なライン設計やレイアウトができていても、品質管理(QC)に問題があると、不良品が増えて生産効率を下げてしまいます。生産ラインでは、適切な品質管理ができるか、トラブルが起きた際に迅速に解決できるかも大切です。
品質管理の基本と重要性
品質管理は、不良品の減少と顧客満足度の向上に重要な役割を果たします。生産ラインにおいては、工程管理や品質検証、品質改善を通じて製品の品質を保証しなくてはなりません。
品質管理は、以下の4つのステップに沿って行います。
- 品質計画……品質基準を設定し、達成するための計画です。
- 品質保証……製品やサービスが設定された基準を満たしていることを確認します。
- 品質管理……製造プロセスを監視し、品質基準を維持するための対策を実施します。
- 品質改善……製品やプロセスの品質を継続的に向上させるための活動です。
トラブルシューティングの方法と分析手法
生産ラインの生産性を低下させないためには、問題発生時には迅速に原因特定し、スムーズに解決することが重要です。
トラブルシューティングの手順や適切なツール、メンテナンス計画のポイントを知っておきましょう。
トラブルシューティングの手順
- 問題の特定……問題の症状を確認し、詳細な情報を収集します。
- 原因の分析……問題の根本原因を特定するために、データを分析し、仮説を立てます。
- 解決策の検討……根本原因に対する解決策を複数検討し、最適な方法を選びます。
- 実施と検証……選定した解決策を実行し、問題が解決されたかを確認します。
- 再発防止策の実施……同様の問題が再発しないように、プロセスやシステムの改善を行います。
トラブル時に活用できる分析手法
FMEA(故障モード影響解析)
製品やプロセスにおける潜在的な故障原因(故障モード)を分析し、その影響を評価する手法です。故障モードは、工程・設計・機能の3つの対象に分けてFMEA評価フォーマットを活用して分析します。
5Why分析
問題の根本原因を徹底的に追求するために「なぜ」を5回繰り返して問う手法で、「なぜなぜ分析」とも呼ばれます。原因を洗い出し、再発防止や改善策を見つけます。カイゼンやジャストインタイム方式を生み出したトヨタが発案した分析方法であることから、製造業界を中心に活用されています。
特性要因図
問題の原因を視覚的に整理するためのフレームワークで、その見た目からフィッシュボーン図とも呼ばれます。問題が起こりそうな要因を洗い出し、事前に管理できるようになります。特性要因図を活用し、作業マニュアルを策定することも可能です。
生産ライン改善の重要性
生産ラインを改善するには、製品の特性や製造量、規模に合わせた適切な設計やレイアウトの配置が重要と分かりました。
生産ラインを改善すると生産性が向上するだけでなく、コスト削減や業務効率化から全体の利益向上にも好影響を与えます。
5S活動や工程の見直し、設備の最適化やツールの導入によって生産性を向上できます。
生産ラインを効率よく改善したいなら、ある程度の作業を自動化できるツールとの連携も有効です。
製造現場にツールを導入し、実際に生産ラインの改善を実現した企業も多くいます。
>>PETボトル充填ラインへの生産スケジューラ導入事例
>>多品種少量生産ラインへの生産スケジューラ導入事例
>>医薬品製造ラインへの生産スケジューラ導入事例
Asprovaの生産スケジューラは、生産ラインの業務を改善するために最適なリソースの活用方法を提案します。 生産スケジューラ導入によって具体的にどのような業務改善が実現したのかはこちらのページをご確認ください。

コラム編集部

最新記事 by コラム編集部 (全て見る)
- なぜこの2社は計画のブレを最小限にできたのか?精度向上のカギを解説 - 2025年7月2日
- “半日が10分に短縮”も可能に!属人化を脱し、計画作成を効率化した方法とは? - 2025年7月2日
- “なんとなく管理”からの脱却!デンカが語る、見える化による現場改善ストーリー - 2025年7月2日