QCDとは?生産管理において重要な理由や改善方法・踏むべきステップを解説
2024.07.17A0 生産管理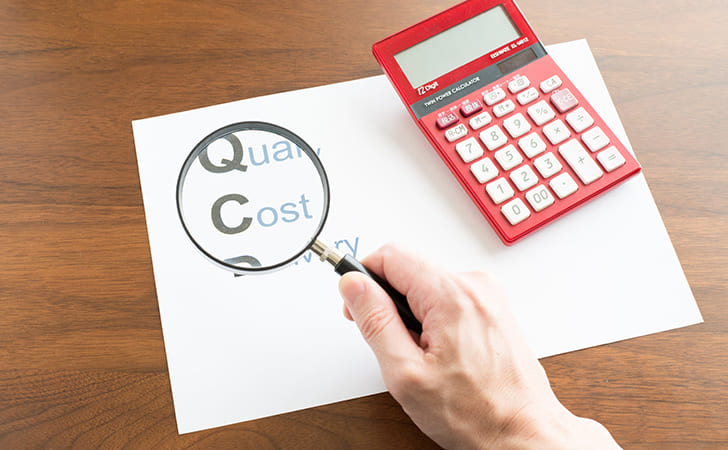
製造業の現場において、業務改善の大きな鍵となるのがQCDです。QCDを成功させるためには、それぞれの要素に必要な施策を把握し、バランス良く改善することが必要です。この記事では、QCDの重要性や改善方法、踏むべきステップを解説します。
【目次】
■QCDとは
■QCDの重要性
■QCDの優先順位
■どのようにして改善するか
■QCD改善のために踏むべきステップ
■おわりに
QCDとは
QCDとは、以下3つの単語の頭文字を取った用語です。
- Quality(品質)
- Cost(コスト)
- Delivery(納期)
3要素のバランスを考慮して経営することで、顧客満足度の向上だけでなく、企業の利益や組織としての信頼性の向上にも期待できます。品質とコスト、納期の3つはどれか1つに偏ると他の要素で支障が出る相互関係にあります。たとえば、品質向上のために最新の機械やシステムを導入すると多くのコストがかかります。また納期のスピードを優先するあまり、品質が落ちるケースがあるかもしれません。健全な経営をおこなっていくためには、QCDの3つの要素のバランス/力関係を適切に保つことが重要です。近年では、QCDに顧客対応の「サービス(Service)」を加えたQCDSの呼び方もあります。また、安全(Safety)やモラル(Morale)、環境などが加えられる場合もあります。製造業では、一歩先まで多角的に見据えた戦略が不可欠です。とはいえ、初めから全ての要素を揃えることは容易ではありません。そのため、手始めにQCDに絞った施策を検討するのが良いといえるでしょう。
QCDの重要性
QCDの目的は、コストを抑えて高品質な製品・サービスを提供することです。目的を達成するためにはQCDを適切に運用・改善する必要があります。QCDに取り組む前に、まずQCDの重要性について明確に理解しておくことは重要です。ここでは、以下4つの重要性について解説します。
- 顧客満足度の向上につながる
- 生産プロセスの見直しにつながる
- 差別化に成功しブランディング強化につながる
- 各種リスクの低減
顧客満足度の向上につながる
QCDが重要な1つ目の理由は、顧客満足度の向上につながることです。QCDのうちの「Quality(品質)」を改善すれば、質の高い商品やサービスを生産できるようになります。またQCDのバランスをとり低コストに提供できれば、顧客にとって高品質かつ手が届きやすい商品となります。結果として、顧客がリピーターになる可能性が高まるでしょう。顧客が企業や商品のファンとなりSNSや口コミを行えば、さらなる販売促進にも期待できます。
生産プロセスの見直しにつながる
QCDが重要な2つ目の理由として、生産プロセスの見直しにつながることが挙げられます。QCD改善の際には、生産から出荷にいたるまでの一連の流れを見直す必要があります。具体的に行える施策の例は以下のとおりです。
- マニュアルの整備
- 仕入れ先の変更
- AIやIoTなどの最新技術の導入
生産プロセスの見直しを行うと、今まで把握できていなかった工程上の無駄が可視化しやすくなります。生産プロセス全体が改善されると、人員や業務時間の削減にもつながります。生産コストが下がると顧客へ安く早く提供できるようになり、満足度向上につながる好循環が生まれるでしょう。
差別化に成功しブランディング強化につながる
差別化に成功しブランディング強化につながる点も、QCDが重要である理由の1つです。QCD改善を行う際は、顧客が3つのうちどの要素を最も重視しているかを把握している必要があります。たとえば、品質を最重視する方がいれば、安いほど良いと考える方もいます。自社のターゲットとなる顧客のニーズを知ることができれば、競合との差別化が可能です。自社のターゲット層が品質を重視しているのであれば、原料や製造過程に力を入れられるかもしれません。他社と比べて明らかに高クオリティな商品が完成したなら、自社の強みとしてアピールできます。一方、安さを重視する層がメインターゲットになっている場合は、材料費や人件費のコストダウンに力を入れられます。競合のどの製品よりも安く提供できれば、価格面が自社の強みとなるでしょう。顧客に合わせた適切な戦略を打ち、ブランディング強化につなげるためには、QCDの取り組みが欠かせません。
各種リスクの低減
QCDが重要な4つ目の理由は、各種リスクを低減できる点です。QCDの改善により低減できるリスクの例として以下のようなものが挙げられます。
- 不良品発生による手戻り
- 顧客からのクレーム
- コスト増加
- 不透明なキャッシュフロー
QCDの見直しにより、表面化されていなかったリスクが発見できる場合もあるでしょう。リスクに対し適切な施策を取れば、企業としての信頼性をより高められます。
QCDの優先順位
QCDの中でも最も優先順位が高いのが、「Quality(品質)」です。納期が短くコストが安い製品であっても、顧客が望んでいる品質でなければ、顧客満足度の向上にはつながりません。QCDを改善する際には、「品質ファースト」を意識しましょう。
どのようにして改善するか
QCDの3つの分野では、それぞれ取り組むべき事柄が異なります。QCDの各要素は、お互いに影響しあうトレードオフの関係性になっています。そのため、単体の個別改善ではなくQCD全体をバランス良く解決していくことが大切です。ここでは、QCDそれぞれの改善方法について具体的に解説します。
- Quality(品質)
- Cost(コスト)
- Delivery(納期)
Quality(品質)の改善
Quality(品質)を改善するためには、明確な基準の設定が重要です。既存の基準がある場合でも、品質向上に向けた見直しが必要となることがあります。合格基準に達する製品を安定生産するためには、運用方法の改善を行いましょう。以下は品質改善に役立つ施策の例です。
- 作業手順のマニュアル化
- 業務の標準化
- 設備の維持管理体制の見直し
- 検品の徹底
一定の品質の製品を納期内に生産するためには、作業者ごとのばらつきを防ぐための手順のマニュアル化や業務の標準化が欠かせません。また、現場の工程で生じている無駄を洗い出し、工数を低減すれば業務へ集中しやすくなり、品質改善につながります。設備の維持管理も品質改善と密接な関連があります。設備の定期点検により、異常をいち早く発見でき、不良品の発生を防ぐことが可能です。さらに、基準に達しない製品が生じた場合のルールも策定する必要があります。不良品は廃棄する、差し戻すなどの対処をあらかじめ決めておきましょう。万一不良品が顧客の手元に届いてしまった場合、返品・交換などの対応を迅速に行うシステム作りも重要です。
Cost(コスト)の改善
Cost(コスト)には、人的コストや金銭的コストが含まれます。納期や一定の品質を保つための予算の策定が必要です。また、予算を決める際は、ある程度余裕を持たせることも重要です。予算に余裕がないと、生産のための十分なリソースが避けず、品質を低下させてしまう可能性があります。また、原材料の価格高騰や欠員補充による余分な人件費などが生じる場合もあるため、調整のために余裕を持たせておきましょう。コスト削減は、製品の生産に影響を与えない範囲から始めるのがおすすめです。カットしやすいコストの例として、以下が挙げられます。
・各種消耗品(清掃用品、紙、筆記用具品など)
- 各種消耗品(清掃用品、紙、筆記用具品など)
- 通信料金
- 各種光熱費
- 古い機材
- 古いシステム
古い機材やシステムは、パフォーマンスが低下し、不具合や故障が生じる可能性が高いです。場合によっては新しいものに入れ替えることでコスト削減につながるかもしれません。コスト削減は従業員が一丸となって行う時に高い効果を発揮します。そのため、コスト削減を実施する際はその目的を周知させることが重要です。また、正確な原価計算を行い、無駄なコストが生じている部分を明確化しましょう。コスト削減の開始時は、多くの分野に着手するよりも効果が出やすい部分から取り組むのが効果的です。
Delivery(納期)の改善
Delivery(納期)の改善として、納期までに必要な工数・時間を設定しスケジューリングを行うことが重要です。また、スケジューリング通り生産が進んでいるかのモニタリングもしましょう。遅れが生じている工程については、リソースの追加や生産数の見直しなどの柔軟な対応が求められます。また、生産が早すぎるのも顧客に不信感を与えたり、保管スペースを圧迫したりする要因となります。あくまで、当初のスケジューリングに沿って生産を行える仕組み作りを意識しましょう。
QCD改善のために踏むべきステップ
QCD改善には、業務に関係する全ての従業員の理解と協力が求められます。そのため、実施の際は段階を踏んで進めていくことが大切です。また、検証と改善を繰り返していく必要もあります。QCD改善のためには、以下の3ステップで考えましょう。
- ステップ1:現場の状況を把握する
- ステップ2:改善策の計画と実践
- ステップ3:効果検証とさらなる改善
ステップ1:現場の状況を把握する
まずQCD改善に取り掛かるにあたり、現場の状況を把握する必要があります。現場の実情を一番良く理解しているのは、従業員です。そこで、ヒアリング・モニタリングを実施し、現場の声を集めましょう。収集した情報をもとに、データ分析を行うことも有効です。現場の状況を理解する際には、以下のような情報を数値化し、整理しましょう。
- 返品数
- クレーム数
- 設備稼働率
- 在庫回転率
- 残業時間
- 納期遅延件数
ステップ2:改善策の計画と実践
現状把握のフローで課題を洗い出したら、ステップ2では改善案を計画・実践しましょう。課題の優先順位を定め、投資可能な費用と効果のバランスを検討することで、改善策を立てられます。大規模にコストをかけられる場合には、工場全体の自動化などを行えるかもしれません。一方で、コストが限られている場合には、必要ツールのみの導入を選択する企業も多いです。生産システムの改善に役立つITツールには、「生産スケジューラ」や「工程管理システム」があります。従業員の意識向上のために、「5S(整理、整頓、清掃、清潔、しつけ)」の徹底をすることも役立つでしょう。
ステップ3:効果検証とさらなる改善
QCDでは、効果検証と改善を繰り返すことも重要です。一定の期間QCDを実施した後、目標に照らし合わせた効果検証を行います。検証する際は、可能な限り効果を数値化するのが望ましいです。効果を数値化し可視化しやすくすることで、再現性を高められます。また、思うほど効果が上がらなかった場合には、明確な原因を検証しましょう。検証と改善を続けていくことで、自社にとって最適なQCD推進を達成できるようになります。
おわりに
この記事では、生産管理の基本である「QCD」についてご説明しました。QCDとは、以下の3つの単語の頭文字から成る用語です。
- Quality(品質)
- Cost(コスト)
- Delivery(納期)
QCDの中で最も優先順位が高いのは、「Quality(品質)」です。顧客満足度を向上させるためには、「品質ファースト」を意識しましょう。また、QCDの3つの要素は互いに影響し合うトレードオフの関係にあります。どれかに比重が偏り過ぎると、他方に弊害が出る場合もあります。そのためQCDは、全体をバランス良く改善することも重要です。
QCD改善の具体的な施策として、業務効率化のためのツールを導入するのも良いでしょう。その中でも特に有効なツールの一つが「生産スケジューラ」です。
生産スケジューラとは、人員や設備などのリソースと生産量とを照らし合わせ、必要なリソースを割り当てるシステムです。品質(Quality)の面では、生産スケジューラを活用することで生産計画を精緻に立てることができ、これにより品質のばらつきを減少させ、安定した製品品質を維持することが可能になります。計画通りの生産が可能となることで、品質の向上が期待できます。
次に、コスト(Cost)の面では、生産資源の最適配置が可能となり、無駄なコストの削減が実現します。たとえば、在庫の適正化や稼働率の向上により、運用コストが削減されることが期待できます。
さらに、納期(Delivery)の面では、生産スケジューラはリアルタイムでのスケジュール調整が可能であるため、突発的な変更にも柔軟に対応できます。これにより、納期遵守率が向上し、顧客満足度の向上につながります。
弊社の生産スケジューラ「Asprova」は、30年以上の実績とノウハウをもとに制作した、国内最大級の導入実績を誇るシステムです。多くの企業様から、導入後に生産計画の効率化とQCDの向上に成功したとの声をいただいております。生産スケジューラ導入によって具体的にどのような業務改善が実現したのかは、こちらのページをご確認ください。

コラム編集部

最新記事 by コラム編集部 (全て見る)
- 納期管理:生産スケジューラの活用 - 2025年4月14日
- スケジューリング技術の応用による生産性の改善 - 2025年4月14日
- Lean Manufacturing~生産スケジューラの活用で最適な生産を - 2025年4月14日