生産管理の体制を整える「5S」とは?5Sのメリットと具体的な進め方を徹底解説!
2024.07.17A0 生産管理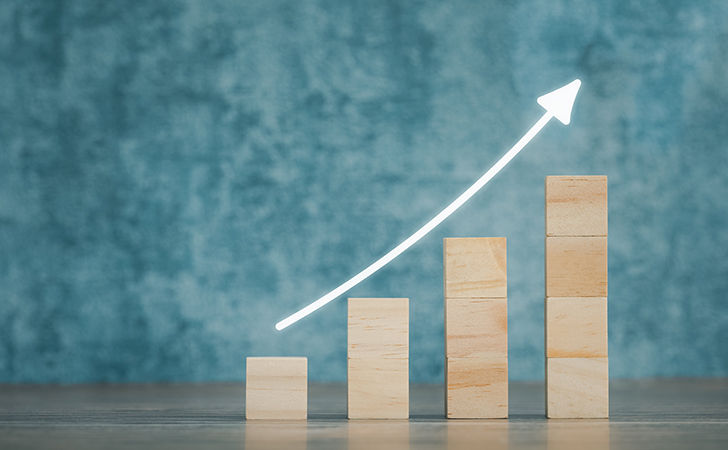
「5S」という言葉をよく耳にはするが、具体的な内容は知らない、導入したいが進め方が分からないという方も多いでしょう。5Sとは整理・整頓・清掃・清潔・しつけの5つの頭文字Sからとった、職場環境を整備する活動です。しかし、単なる美化活動ではありません。5Sを継続することで、社員の意識改革や業務の改善につながります。5S活動を通じて、継続的に改善できる組織を目指しましょう。
【目次】
■5Sとは
■5Sを行う目的は
■5Sを実践するメリット
■5Sの具体的な進め方
■5Sを効率的に進めるためのポイント
■5S活動をさらに促進するための生産スケジューラの導入
5Sとは
5Sとは整理・整頓・清掃・清潔・しつけの5つの頭文字Sからとった、職場環境を整備する活動です。
1)整理
必要なものと不要なものを区別して、不要なものを捨てること
2)整頓
必要なものを決められた場所に置き、表示をすること
3)清掃
職場や道具をきれいな状態に保つこと
4)清潔
整理、整頓、清掃を徹底し、常にその状態を維持すること
5)しつけ
清潔な状態を保てるよう従業員に習慣化させること
5Sは単なる、整理整頓や美化活動ではありません。生産管理の基本の考え方であり、かなりの時間と労力を費やして徹底的に取り組み、作業効率化や社員の意識改革へとつなげることが重要です。
5Sを行う目的は
5Sの目的は、次の3段階に大きく分けられます。
段階 | 目的 |
---|---|
第1段階:直接的な効果 | 5S活動そのものにより、安全性や生産性の向上、在庫削減効果など直接的な成果を得る |
第2段階:間接的な効果 | チーム単位の5S活動により、良好なチームワークを築き、職場の活性化を促す |
第3段階:最終的な効果 | 自律性の高い人材の育成、継続的な管理・改善活動を実践できる組織の育成 |
5Sの目的は、美化活動ではないことに注意しましょう。徹底した美化活動の先にある、直接的・間接的な効果だけではなく、自律性の高い人材の育成と継続的な改善が可能な組織の育成という最終目的を常に意識しておくことが重要です。
5Sを実践するメリット
5Sを実践するメリットは、職場が整理整頓されるだけではありません。組織に5S活動を取り入れるメリットとして、主に次の3つが挙げられます。
- 生産性の向上
- 安全性の担保
- 従業員の意識の変化
それぞれのメリットを説明します。
生産性の向上
5S活動の直接的なメリットは、生産性の向上です。製造業における生産性の向上とは、無駄な時間を削減して製造の時間を増やすことです。現場が整理整頓されておらずものが乱雑に置かれていると、必要な工具や資材などを探す手間が発生します。ものを探すだけに費やす手間と時間は、何も製造されていないので無駄です。現場が整理整頓されていれば、作業に必要な工具や資材などを探す手間がなく、スムーズに作業を始められます。また、作業自体に費やす時間も短縮できるうえ、作業を行う従業員のモチベーションアップやストレスの軽減にも役立つでしょう。1回当たりの作業時間の短縮がわずかであっても、積もり積もれば膨大な時間になります。5S活動を行い、無駄な時間を削減して効率的に作業が進むことで、生産性を向上させられます。
安全性の担保
安全性の担保もメリットの1つです。5S活動の清掃は職場や道具を定期的に清掃・点検して、きれいな状態を保つ活動です。工具や機械を定期的にメンテナンスしていれば、不具合や故障・劣化にいち早く気付き、事故を未然に防げる可能性が増します。また、作業場が整理整頓されていれば、従業員に思わぬ事故が起きるリスクも下がるでしょう。5S活動が適切に行われていなければ、機械や工具の状態や職場の衛生状態が良くないことに気付かず、従業員の心身の健康を損ねる危険性があります。5S活動には、職場の安全性の担保、労働災害の防止にも役立つというメリットがあります。
従業員の意識の変化
5S活動を徹底して継続すれば、最終的には従業員の意識の変化が期待できます。ゴミが落ちていても拾わず放置するのが当然の職場では、ますます職場が荒れていく悪循環に陥ります。乱雑な職場では、大きな事故が起こる危険性も上がるでしょう。また、従業員のモチベーションが上がらないことによる生産性の低下も懸念されます。5S活動を徹底して行えば、従業員が団結して5Sを徹底する企業風土が生まれます。従業員一人ひとりの整理整頓への意識や職場の整備に対する意識の変化が感じられるでしょう。5S活動は、作業環境を整えるだけではなく、従業員全体に規律を守る風土や職場への問題意識を芽生えさせられるため、主体性の向上にもつながります。
5Sの具体的な進め方
5Sの目的やメリットは理解できたけれども、どうやって進めたらいいのだろうか?とお悩みの方も多いでしょう。5Sは強制的にさせられるのではなく、全社員が一丸となって徹底的に取り組むことが重要です。ここでは、整理・整頓・清掃・清潔・しつけ、それぞれの具体的な進め方を詳しく説明します。
整理の進め方
整理とは、必要なものと不要なものを区別して、不要なものを捨てることです。要・不要を区別するための方法として、「赤札作戦」が広く知られています。赤札作戦では、まず要・不要の基準を設定します。基準は何でも構いません。たとえば、使用期限や状態、使用頻度や必要な個数などで決めましょう。基準を満たさず不要と判断されたものには、担当者や処置期限日を記入した赤札を貼るのがおすすめです。赤札を貼った不用品は一カ所にまとめ、処置期限日がくるまで保管しておきます。期限日までに一度も使用せず、誰からも処分に異議が出なかったものは、不要なものと判断して処分しましょう。この赤札作戦によって、不要なものを減らし、必要なものだけを残すことが可能です。
整頓の具体例
整理をして必要なものだけを残したら、次に整頓をしましょう。整頓とは、必要なものを決められた場所に置き、表示をすることです。必要なものが常に同じ場所にあり、その場所に何があるかが表示されていれば、ものを探す手間や時間が省けます。新しいものが追加された場合は、仮置き場を作って対応するのがおすすめです。
置き場所
置き場所は、使用頻度に応じて決定します。ドライバーのような日常的に使うものは、身の回りに置いたり、身につけたりしておくと使い勝手がよいです。そうでないものは頻度に合わせて職場内、工場内、別倉庫内といった形で、徐々に遠くに配置しましょう。
置き方
次に、探しやすくて取り出しやすい置き方を考えましょう。使用頻度の高い工具などを積み重ねた箱の下の段に入れてしまうと、取り出すだけでも一苦労です。工具であれば、平置きにしてサイズや種類ごとに区切った定位置を決めると、見つけやすく取り出しやすくなります。壁面や棚などを利用した垂直収納もスペースが最大限に活用できるので、おすすめです。垂直収納を利用すれば、多くのものが収納できるだけでなく、下の段にあるものも取り出しやすくなります。また、使用頻度が低くても、危険なものは安全な位置に保管することも重要です。
表示方法
置き場所と置き方が決まったら、工具とその置き場所の両方にラベリングをしましょう。両方にラベリングをすることで、使用後の返却場所が明確になります。返却場所を明確にすれば、使用後にいろいろな場所に好き勝手に置くことがなくなり、従業員全員がもとの位置に戻すことを意識するようになるでしょう。さらに、使用者の名簿をつくることもおすすめです。その道具をいつ誰が使ったかを分かるようにしておけば、紛失のリスクも回避しやすくなります。
清掃の進め方
清掃とは、単に掃除をするだけでなく、職場や道具を安全で衛生的な状態に保ち、異常を発見しやすくすることを指します。ここで重要なのは、機械や工具、職場をきれいにする仕組みそのものをつくることです。いつ、誰がどこを担当し、どのような方法で、どの程度行うかの明確なルールや基準を決め、可視化しておくとよいでしょう。また、汚れやすいところを点検して、ものが散らかったり汚れたりする原因を特定し、対策を考えることも清掃のひとつです。
清潔の進め方
清潔とは、整理・整頓・清掃の3Sを徹底し、常にその状態を維持することです。清潔は3Sがある程度社内で浸透した時期に、継続的に実践するためのプロセスです。定位置に置かれていないもの、清掃が行き届いていない場所など、いつもと異なる状態にすぐ気付けるよう、写真や画像を用いて「清潔な状態」を記録しておくとよいでしょう。また、清潔な状態を具体的に記載したチェックシートをつくって、基準を可視化することもおすすめです。清潔な状態の基準が統一されれば、誰でも同じような状態を維持することができます。清潔な状態が維持できるようになると、従業員一人ひとりに規律を守る意識が芽生え、意識の向上も期待できるでしょう。また、安全管理がしやすくなり、事故のリスクも減少していきます。
しつけの進め方
5Sの仕上げ段階であるしつけとは、清潔な状態を保てるよう従業員に習慣化させることです。ここまでのプロセスを明確にルール化し、それを従業員全体に周知しましょう。研修の機会を設けるなど、5Sの重要性や効果を定期的に全社で共有する機会をつくることで、組織的な実践が可能になります。また、整理・整頓・清掃・清潔を保つことで、組織風土や従業員の意識に変化が生まれ始めます。自ら課題を見つけ、対策や改善を行うことで、自律性が向上し、企業の組織力や競争力が強化されていくでしょう。
5Sを効率的に進めるためのポイント
5Sを進めるには、組織全体で一丸となって継続的に取り組むことが重要です。しかし、5S活動は結果がすぐには目に見えて現れないため、途中で挫折する企業も少なくありません。5S活動を効率的に進めるために、次の4つのポイントを意識してみましょう。
- 具体的な目標設定を行う
- 5Sの目的を全社内で共有する
- 各種ルールや従業員全員で決める
- チェックシートでルールを見える化
具体的な目標設定を行う
5Sに取り組む第1段階の目的は、徹底した美化活動の先にある品質、生産性や安全性の向上です。その目的を達成するためには、具体的な目標を設定しましょう。たとえば、「不良品発生率◯%以下」「作業工数◯分削減」「月の残業〇時間以内」など、数値化できる身近な目標であれば、従業員も活動に取り組みやすくなります。
5Sの目的を全社内で共有する
5Sの目的をミーティングなどで共有しましょう。目的を共有しておかなければ、単なる美化活動で終わりかねません。5S活動は、徹底的に継続して行う必要があり、強制的にさせられていると感じる従業員が一人でもいれば、目的達成は困難です。5S活動の価値と活動から得られるメリットを全社内で共有することで、取り組みへのモチベーションが上がります。作業場や共有スペースなどに5Sの目的や目標を掲示し、いつでも確認できるようにするとよいでしょう。また、定期的に目的の確認だけではなく、実際に得られたメリットを共有することも重要です。実際にメリットを得られれば、継続して活動するモチベーションにつながります。目的が達成された場合は、それを共有し、新たな目的を設定し続けることが重要です。
各種ルールは従業員全員で決める
5Sに関する各種ルールは、役割や部署を超えて、従業員全員で決めることが重要です。特定の人だけでルールを決めて、強制的に決まりを守らせていては、5Sの目的や意義を従業員に理解してもらうことは難しいでしょう。5S活動を行うのは、現場の従業員自身です。従業員一人ひとりに自分ごととして、納得して取り組んでもらう必要があります。価値や目的を共有したうえで、どのようなルールや基準が必要かについて、可能な限り全ての意見を組み込む努力をしましょう。アンケートやメールなどを利用すれば、効率的に意見を集められます。
チェックシートでルールを見える化
チェックシートを使用することで、ルールをいつでも確認できるようにしておきましょう。いつ、誰が、どこを、どのような方法で、どの程度行うかを具体的に設定し、それを可視化することで、全員の認識が統一できます。整理・整頓・清掃・清潔・しつけの各プロセスを徹底するためには、全員が基準を満たし続けられるような仕組み化が重要です。チェックシートのテンプレートがWEB上で公開されていますので、確認してみてください。
5Sとは、整理・整頓・清掃・清潔・しつけの5つの頭文字Sからとった、職場環境を整備する活動です。必要なものと不要なものを区別して、必要なものを決められた場所に置き表示をします。職場や道具をきれいな状態に保ち、徹底してその状態を維持しましょう。最後に、その状態を保てるよう従業員に習慣化させることが重要です。これらを徹底して行うことで、生産性や安全性が向上します。継続すれば、社員の意識改革による職場の活性化や自律性の高い人材と継続的な改善が可能な組織の育成にもつながります。
5S活動をさらに促進するための生産スケジューラの導入
5S活動を効果的に進めるためには、目標の達成状況や改善点を明確に把握することが重要です。ここで役立つのが、生産スケジューラ(Asprova)です。生産スケジューラを導入することで、生産計画を適切に立てることができ、作成した計画と実績を比較することで具体的な改善点を見つけやすくなります。
生産スケジューラを活用することで、計画立案にかかっていた時間を短縮し、計画立案時の誤りによるリカバリの工数や時間を削減することができます。これにより、浮いた時間を5S活動に充てて職場環境の整備と改善に取り組むことができます。
さらに、生産スケジューラ導入によって、具体的にどのような業務改善が実現したのかを、導入企業の事例を通じてご紹介しています。ぜひこちらのページをご確認ください。

コラム編集部

最新記事 by コラム編集部 (全て見る)
- なぜこの2社は計画のブレを最小限にできたのか?精度向上のカギを解説 - 2025年7月2日
- “半日が10分に短縮”も可能に!属人化を脱し、計画作成を効率化した方法とは? - 2025年7月2日
- “なんとなく管理”からの脱却!デンカが語る、見える化による現場改善ストーリー - 2025年7月2日