製造業の段取り改善とは?具体的な改善案やフレームワークについて徹底解説
2024.06.24A0 生産管理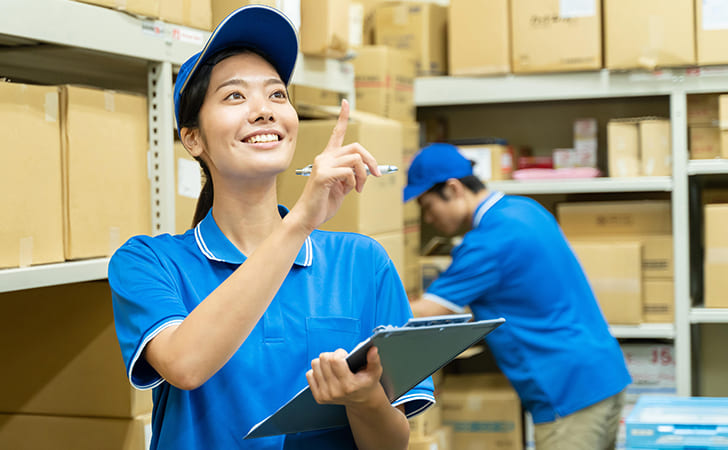
製造業において業務改善を目的に、生産現場の段取りを見直すことは多いでしょう。仕事をムダなくスムーズに行うためには、事前の段取りとQCDを意識した経営体制を考えていくことが重要です。では、具体的にどのように段取りを決めていけばよいのでしょうか。本記事では、製造業の段取り改善について、段取りの重要性や具体的な方法、押さえておきたいフレームワークなどについてご紹介します。
【目次】
■段取りとは
■製造現場における段取りの重要性
■段取りが上手くいかない要因
■段取りの種類
■段取りの改善
■日常的に行える段取り改善
■段取り改善時に押さえておきたいフレームワーク
段取りとは
段取りとは、物事を行う際の順序や手順をあらかじめ整理し、準備することを指します。日常生活でもなじみのある言葉で、「物事をスムーズに進めたいなら、事前の段取りからしっかり取り組まなければならない」ということは、多くの方が共感できるのではないでしょうか。段取りの良し悪しは、生産性に大きな影響を及ぼすのはもちろん、企業の信頼度向上や競争力強化にもつながるので、製造業においても重要です。段取りの際には以下の2つがポイントとなります。
- 「段取り八分、仕事二分」
- QCDを意識する
「段取り八分、仕事二分」
「段取り八分、仕事二分」とは、物事が成功するかどうかが仕事の準備段階で8割は決まるということを表しています。実際の作業に取り掛かる前に、具体的に仕事を進める手順を決めておけば、それだけ質とスピードが上がります。製造業においても同じで、確実に時間内に目的を達成したり、より多くの製品を生産したりするためには、実務に取りかかる前の段取りが不可欠です。
QCDを意識する
製造現場では、QCDが重視されています。QCDとは、Quality(品質)、Cost(コスト)、Delivery(納期)の頭文字を並べたものです。3つの要素のバランスを取りながら作業を進めることで、利益だけでなく信頼性やコスト面にも大きな変化があります。例えば、品質を高めるためのシステム導入などを行えば、コストは上がりますが、品質を向上させることが可能です。納期を早めることに注力すれば、その分品質が落ちやすくなります。このように、どの要素か1つだけを向上させると、他の要素が崩れてしまうかもしれません。バランスの良い経営体制を整えていくのであれば、QCDのバランスを取ることが重要であると言えるでしょう。製造現場における段取りの重要性
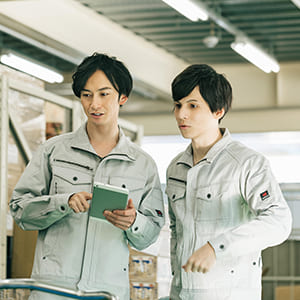
製造現場の段取りとは、生産工程に合わせて必要となる道具や材料を事前に準備しておくことを指します。段取りが重要な理由は以下の通りです。
- 生産効率を高めるために必要
- 製造コストの削減効果も見込める
- 従業員のタイムマネジメントのスキルも高められる
- 経営ニーズや市場ニーズの多様化に応えられる
生産効率を高めるために必要
製造業の生産工程における段取りを最適化することで、機械や装置の稼働率を向上させることが可能です。事前に段取りができていないと、材料の供給待ちで機械の稼働が停止してしまうケースや、工具や治具などの生産工程で必要なものが準備できていないというようなことが起こります。また、段取りを行って無駄な作業を洗いだすことで、業務時間を短縮でき、重要度の高い業務に費やす時間が増やせます。その結果として仕事の質や生産効率の向上が期待できるでしょう。
製造コストの削減効果も見込める
製造工程のコスト削減は、材料原価の見直しや不良品ロスの削減を中心に取り組みます。しかし、段取りや工程の見直し、立ち上げ時間の短縮などといった改善も必要です。製造工程には直接関係しない無駄な部分を見直すことで、結果として製造コストの削減効果が期待できます。削減したコストは新たな設備の投資などに使えるようになり、企業の成長へとつなげることが可能です。さらに、人の手で行っている作業を自動化できるシステムやツールの導入を行うことで人件費の削減にもつながります。
従業員のタイムマネジメントのスキルも高められる
働き方改革の導入によって、多くの企業が残業時間を減らすよう業務改善に努めています。全体の労働時間を減らすためには、企業内の改善だけでなく、就業時間内に業務を終えることができる個人のタイムマネジメント力も必要です。段取り力がある方は業務を可視化し、優先順位を付けて業務を行うなど、タイムマネジメント力に関するスキルを身につけています。
経営ニーズや市場ニーズの多様化に応えられる
近年では、多品種少量生産や短納期化の要求の高まり、在庫リスクの回避といった、市場ニーズや経営ニーズが多様化しています。厳しい競争下を生き抜いていくためには必要な時に必要な分だけ造るという考え方が重要です。必要以上に時間をかけず、作業を短時間で行えるようにすることで、多様化する時代にも対応できるでしょう。
段取りが上手くいかない要因
事前に準備をしていたにも関わらず、段取り通りにいかない要因として、以下の2つがあげられます。
- 段取り替えの準備が不十分
- 現場の整理整頓ができていない
- それぞれについて説明します。
段取り替えの準備が不十分
製造業の段取り替えは生産工程の中でも欠かせない作業の一つです。生産ラインを停止して行う段取り替えの場合、停止時間が製品ロスの時間となり、その分収益に大きな影響を与えます。段取り替えの準備が不十分でないか、検査仕様書・手順書・図面といった書面が揃っているかを事前に確認しておくことが大切です。
現場の整理整頓ができていない
製造業の現場でムダな時間を削減するためには、整理整頓を徹底しなければなりません。しかし、繫忙期になると、業務が煩雑になり整理整頓まで行き届かないケースや、備品や工具の場所を全員が把握していないケースなどがあります。結果として、内段取りと外段取りのほかにも「ムダな段取り」が生まれている可能性があると言えます。
段取りの種類
製造業における段取りには「内段取り(うちだんどり)」と「外段取り(そとだんどり)」の2種類があります。
内段取り
内段取りとは、機械や作業を一旦止めないと作業できない段取りです。例えば、機械を停止しないと部品を交換できない、作業を一旦止めないと確認できない段取り作業を指します。機械や作業の中断は生産性に直結しやすいため、段取り改善では、内段取りから優先的に取り組みます。
外段取り
外段取りとは、ラインや機械設備を稼働させたまま、または作業者が作業を続けたまま行える段取りです。例えば、型や刃具、治具など道具の準備や資材の運搬、後片付けなどが挙げられます。
内段取りは生産性に直結しますが、外段取りは生産性に直接的に影響を与えることはありません。そのため、段取り改善では内段取りの「外段取り化」ができるかを考え、移管するのも対策の一つとなります。
ムダな段取り
ムダな段取りとは、金型や治具、工具などのモノを探すことを指します。備品の場所の把握と整理整頓がされていれば、ムダな段取りはなくせるはずです。しかし繁忙期になると、管理が行き届かず、結果として時間のロスとムダな段取りが発生してしまうというケースも少なくありません。よって、ムダな段取りをなくし、生産効率を高める仕組みづくりをすることが段取りを改善するための第一歩だと言えます。
段取りの改善
段取りの基礎や重要性を理解できたところで、さっそく段取り改善に取り組んでいきましょう。 ここでは、段取り改善をステップごとに詳しく解説します。
1.段取り時間の現状を把握する
まずは、段取りに使っている時間の現状を把握しましょう。作業者の就業時間のうち、段取り作業に占めている時間を割り出します。
次に、各工程で実際にかかっている段取り時間の調査を行います。段取り時間を把握すると、特に時間がかかっている作業を発見できるようになり、なぜ時間がかかっているかの原因究明や課題抽出がしやすくなります。
2.段取り作業を切り分ける
では、具体的に段取り改善ステップをみていきましょう。
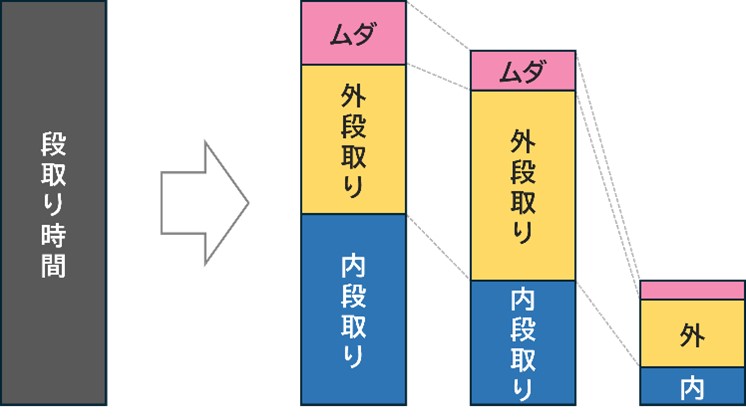
段取り改善では生産性に直結する内段取りを優先的に行います。
まずは、段取り作業の全体をリストアップし、機械設備や作業を止めて行う「内段取り」と作業を止めずに行える「外段取り」に分けていきます。段取りの切り分けは、器具を探している時間といった、「ムダな時間」の発見にもつながります。ムダになっている作業も3つめの区分けとして記録しておきます。
切り分け時に把握しておくべき段取り時間の定義
段取りの時間とは、現在製造中の製品の作業が終わった瞬間から次の製品の製造に切り替えて、1つの製品が完成した瞬間までの時間を指します。段取りを早く終わらせても、製造開始後にやり直し等の作業が発生していては、生産性向上に繋がっているとは言えません。
3.改善案を挙げる
内段取りの改善案(例)
- 作業者1人で行っていた段取りを複数名に変更する
- 属人化を減らし、誰にでもできる段取りに標準化する
- 作業を簡易化する
- 内段取りの教育や訓練を標準化する
- 外段取り化できないか検討する
外段取りの改善案(例)
- 金型や治具、材料などを機械の近くに準備しておく
- 作業手順を見直して時間短縮を図る
「ムダ」の改善案(例)
製造業の段取り改善の中で「ムダ」の改善には、3つの案があります。
- 2S(整理・整頓)の徹底
- 作業場の導線を見直す
- 作業姿勢や環境を改善してムダを減らせないか
ムダな段取りの改善点の洗い出しに行き詰まったら、オズボーンのチェックリストをはじめとするフレームワークを使って視点を変えることもおすすめです。オズボーンのチェックリストには、アイデアを生み出すための「9つの視点」があります。視点に沿って問題点を洗い出せるため、ゼロから考えるより効率的なところがポイントです。
4.内段取りの外段取り化
内段取りは、機械設備もしくは作業者の稼働を止めないと実施できないため、停止している間は付加価値が生まれません。機械や作業者が稼働している状態で段取りを行う、つまり、これまで内段取りで行っていた作業を外段取り化できれば、生産性を落とさずに段取りを進めることができます。 内段取りの外段取り化は簡単ではありませんが、新しいテクノロジーや手法を使えば不可能ではありません。
外段取り化の改善案がコストをかけずに行えるか、ある程度のコストを要するかを見定めて、まずはお金をかけずにできることから始めていきましょう。
5.内段取りの時間短縮
内段取りの改善案で挙げた「作業者1人で行っていた段取りを複数名に変更する」、「属人化を減らし、誰にでもできる段取りに標準化する」などは、内段取りの時間短縮を可能にする手段です。また、内段取りの教育や訓練の標準化も、作業効率アップや属人化の防止につながります。 「この社員でないと内段取りができない」、「内段取りが複雑でわかりにくい」といった課題を抱えている場合は、標準化や平易化を実施し、脱属人化を図ることで効率化や安定稼働につながります。
「段取りのノウハウが特定の社員に集約し、属人化している」
「生産工程が複雑で前後工程のつながりがわかりにくい」 など担当者のお悩みを解決できるのが生産スケジューラです。段取り改善に課題を抱える現場での生産性向上を実現しており、多数の導入実績と蓄積されたノウハウがシステムに反映されています。生産スケジューラについて詳しく知りたい方はこちら。
6.生じている「ムダ」を減らす
次に、段取りで生じているムダを徹底的に減らしていきましょう。例えば、「器具を探すのに時間がかかっている」といったムダな時間は、2S(整理・整頓)の徹底によって改善できます。置き場所をルール化する、保管場所を整理する、ラベリングして見つけやすくするなどの方法があります。
段取りでよく使う器具はキット化して、いつでもすぐに使える状態にしておくのも効果的です。移動や運搬に無駄な時間がかかっている場合は、配置場所や導線を見直してみましょう。
段取り改善をしていると、内段取りからも外段取りからも廃止できる作業を発見できる場合があります。装置や自動化の進歩によって、段取り替え時にそのままの状態で問題なく稼働できるケースが存在するのです。「やめる」ことを見つけるだけでも、大幅なムダ時間の削減につながります。
ムダの洗い出しに役立つトヨタ生産方式
ムダの洗い出しに、トヨタ生産方式の基本思想を元にした「7つのムダ」について考える方法もあります。多くの製造業は在庫を抱えて販売しながら利益を得る方式ですが、トヨタはムダを徹底的に排除することで在庫を抱えずに、必要なものだけを滞りなく生産するJIT方式を確立しています。トヨタ方式のように、あらゆるムダについて深く究明することで、不良品を出してしまうリスクをなくし、品質向上にもつなげることが可能です。
日常的に行える段取り改善
現場の不平・不満の声を洗い出す
段取り改善を考えるにあたり、現場の不平不満の声を聞くことが有効な場合があります。小さな不満であれば流してしまうこともありますが、改善策として取り込むことで、現場で働く従業員の満足感や、仕事に対するモチベーションの向上につながります。
必要な段取りのピックアップ
段取りを個々のやり方に任せていると、作業者によって能力に差が出やすくなりますし、抜け漏れやミスが起こりやすくなります。必要な段取りをピックアップして標準化し、段取りの品質に差が出ないようにしましょう。
優先順位付けとムダの排除
作業順序が特に決まっておらず、段取りの進行を個々に任せていると、作業者によって時間にばらつきが出やすくなってしまいます。 初めにやること、必ず行うことなど、作業内容に優先順位をつけて標準化しましょう。また、作業や移動、待ち時間などのムダの排除も重要です。これらのムダが生じていないかを個々やチーム単位でチェックして、ムダをなくすにはどうすれば良いか、仕事の方法を見直します。
マニュアル化する
段取りをマニュアル化しておくと、誰もが作業のムダを省きながら優先順位ややるべきことを把握し、生産性を意識して作業を進めることができます。新しい人員が配置された際には、教える手間が省けるのもメリットです。
また、段取り改善前と実施後の結果を比較してブラッシュアップにつなげる、他チームへの共有で全体の効率化を図れるなどさまざまな場面で役立ちます。
最適化された段取りに慣れる
最適化した段取りが共有された際、事前に新しいやり方に慣れるトレーニングをしておけば、本番の稼働時間ですぐに取り掛かることができます。段取り改善でより良い案を導くだけでなく、チーム全員がいち早く取り組めるようすぐに共有することも大切です。
外段取り化する
内段取りの外段取り化は、大がかりな設備や機械を導入しなくても、個々で意識的に取り組めば行えるケースも存在します。 例えば、スケジュールの立案や事前のスケジュール確認です。時間意識が高まり、時間内に完了すべき項目がわかるので作業効率や生産性アップにつながります。1日の作業の流れを事前に把握しておくだけでも効果があるので、空き時間や準備時間に確認する習慣をつけましょう。
段取り改善時に押さえておきたいフレームワーク
段取り改善時に押さえておきたいフレームワーク案を6つ紹介します。
- 5S活動
- QCD
- トヨタのシングル段取り
- 4M/6M
- ECRS
- MECE
5S活動
経済産業省の中小企業向けサイトによると、5S活動とは以下のように定義されています。
- 整理(Seiri):必要と不要を区別すること
- 整頓(Seiton):置き場所を明確にすること
- 清掃(Seisou):掃除とともに点検すること
- 清潔(Seiketsu):きれいな状態を維持すること
- しつけ(Shitsuke):ルールを守り習慣にすること
5S活動は元々、自動車メーカーを中心とした製造業に定着していた活動ですが、現在では小売業やサービス業まで浸透しています。常に整理整頓され、清掃が行き届いた職場環境で仕事を行うことは、良い成績を出すことにもつながります。5S活動を導入するためには、従業員全体が良い状態を保つ意識を持ち、ルールやチェックシートなどを用いて習慣化することが大切です。
QCD
先述した通り製造業にとって、QCD(品質・コスト・納期)のバランスを保つことはとても大切です。良い製品を納得のいく価格設定で納期までに完納するためには、努力と実行力が求められます。QCD全てを向上させた状態で継続していくことは難しいため、常に相関関係を見直し、調整をかけながら進めていかなければなりません。また、QCDの中で一番優先すべき要素は、「品質」だと言われています。どんなに安くて早い納品物であっても、品質が悪いものであっては結果として顧客の不満へとつながってしまいます。そのため、コストや納期は顧客の要求や状況をすり合わせた上で調整を行いましょう。
トヨタのシングル段取り
トヨタ自動車はシングル段取りの仕組み化を採用し、段取り時間の短縮に成功しました。通常、段取り替え時に内段取りであれば生産活動を止めて、段取りを行う必要があります。その場合、生産活動を停止させるため、稼働率を下げないためには段取り替え時間の短縮が必要です。トヨタのシングル段取りは、1品1仕様の個別生産の連続ラインを目指し、内段取りを外段取りにできないかを考え、次に内段取り時間を短縮できないかを考えました。結果として、4時間かかっていた段取り時間を3分にまで短縮することに成功したのです。
4M/6M
製造業で品質管理の要素を表す「4M/6M」と呼ばれる考え方があります。製造業における生産の4要素である4Mとは次の通りです。
- Man(人):作業担当者
- Machine(機械):現場の機械
- Material(材料):製品に使用する材料
- Method(方法):作業工程
6Mは、上記4つの要素に2つの要素を加えます。
- Measurement(検査・測定):製品の品質検査と測定
- Management(マネジメント):生産工程全般の管理
これらの要素を順にひとつひとつ確認することで、作業効率の改善や安全性の向上が期待できます。段取りを改善するためには、それぞれの要素を元に品質をより良くするポイントを見つけていく力が必要です。
ECRS
ECRS(イクルス)は「業務改善の4原則」のことで、製造業の段取り改善を行う上で押さえておきたいフレームワークです。業務改善の4原則は以下の通りです。
- Eliminate(排除):業務目的を再考し、不要な作業がないか洗い出す
- Combine(統合):類似業務を一体化し、複雑な業務の分離を検討する
- Rearrange(順序入れ替え):作業の順序や場所、担当者の変更などを行う
- Simplify(簡素化):作業のパターン化や自動化、省力化を行う
業務改善を行うには、4つの頭文字の順に確認を進めていくことが一般的です。
MECE
MECE(ミーシー)とは、「Mutually Exclusive and Collectively Exhaustive」の頭文字を取った言葉で、漏れとダブりをなくすといった意味合いを持っています。MECEの思考を持つことで、総合的に必要事項を分類し、問題点や課題解決への正しいアプローチを導き出すことが可能となります。まずは、大きな目的を設定し、その要素を洗い出し細分化することから始めてみましょう。分類する中で重複はないか、漏れはないかを考えることが正確な答えを導きだすために必要なポイントです。

コラム編集部

最新記事 by コラム編集部 (全て見る)
- S&OP(Sales and Operations Planning)~生産スケジューラ連携 - 2025年4月9日
- 在庫管理:ムダを削減し、欠品を防ぐ最新手法 - 2025年4月9日
- MESシステム~生産スケジューラ連携でPDCAサイクルを最適化 - 2025年4月9日