プッシュ型・プル型の生産方式とは? メリット・デメリット、導入手順を解説
2024.10.15A0 生産管理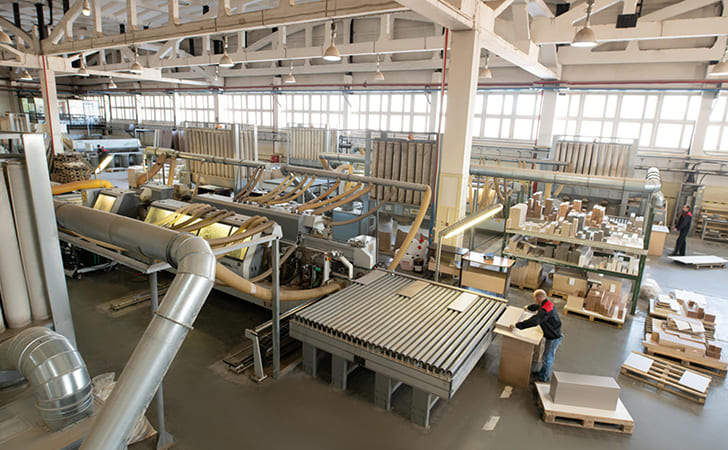
製造業において、効率的な生産管理は企業の競争力を左右する重要な要素です。有名な生産方式と言えばトヨタの「カンバン方式」に代表されるプル型ですが、世界的に広く取り入れられているのは需要予測に基づくプッシュ型。今回は、主にこのプッシュ型生産方式にフォーカスしてメリットやデメリット、導入手順などを解説します。
【目次】
■プッシュ型・プル型とは
■プッシュ型・プル型のメリット・デメリット
■プッシュ型を導入する手順
■まとめ
プッシュ型・プル型とは
製造業における生産システムの基本的な考え方として、プッシュ型とプル型があります。ここでは、それぞれの特徴を詳しく説明します。
プッシュ型生産システムとは
プッシュ型生産システム(押し出し方式)とは、上流の作業工程から下流の作業工程に原材料の調達や作業準備、作業開始のタイミングを通知するシステムです。「プッシュ」という言葉は、生産が需要を「押し出す」ように進められることを表しています。
プッシュ型は、未来に備えて作れる時に作るというスタンスで、過去の販売データや市場調査、経済動向などを分析して将来の需要を予測します。その予測に基づいて生産計画を立て、原材料の調達から製造、在庫管理まで一連のプロセスを管理しているというわけです。生産管理がシンプルなため、後述するプル型生産システムよりも広く導入されている生産方式です。
資材の必要量とタイミングを最初に決めておくため、後工程で問題が発生したとしても前工程では計画通りに生産を続けていくことになります。基本的に、半製品の仕掛在庫は下流工程の使用予定と紐づいています。
プッシュ型の生産方式は、生産数が安定していたり、需要の予測が立てやすい製品の製造に向いています。具体的には、ロットで生産を管理している医薬品や化粧品、食品工場などが挙げられます。
プル型生産システムとは
プル型生産システム(引っ張り方式)は、プッシュ型とは逆の概念です。下流の作業工程から上流の作業工程に原材料の調達や作業準備、作業開始のタイミングを通知するシステムのことです。下流の工程から要求がない場合には、生産できる状態であっても作業は開始されません。必要な時に必要な量だけ生産するという点がポイントです。
プル型生産方式の代表的な例としては、トヨタの「ジャストインタイム(JIT)」と「カンバン方式」があります。ジャストインタイムとは、「必要なものを、必要な時に、必要なだけ作る」という生産方式で、カンバン方式はその考えを実現するための道具です。実際に製品に品名や品番などが記載されたカンバンがついていて、カンバンと製品が各工程を順番にわたります。カンバンが作業の合図の役割になっているため、余分な生産は起こらない仕組みになっているのです。
プッシュ型・プル型のメリット・デメリット
プッシュ型とプル型について、それぞれのメリットとデメリットを紹介します。
プッシュ型のメリットとデメリット
プッシュ型生産システムを導入することで得られるメリットと、注意すべき課題について詳しく見ていきましょう。
プッシュ型のメリット
プッシュ型生産計画は、顧客からの実際の注文を待たずに、あらかじめ決められた計画に基づいて生産量を決定する方式です。大きなメリットは、生産管理のシンプルさに由来する柔軟性です。需要予測に基づいた一定量の在庫を維持することで、想定外に注文が増加した場合にも迅速に対応できます。
特に、人気商品や定番商品の場合、在庫切れを防ぐことができるので、販売機会を逃さずに済みます。また、季節によって需要が変わる商品や、セールなどで一時的に注文が増える場合にも、安定して供給できるのがプッシュ型の利点です。
プッシュ型のデメリット
プッシュ型生産システムが常に良いかと言われると、そうではありません。懸念点もいくつか存在します。
まず、過剰在庫のリスクが挙げられます。需要予測が外れると、売れ残りが発生し、保管コストが増えたり、廃棄ロスが出たりする可能性があります。この課題に対しては、予測精度を上げる努力や、在庫管理システムの導入などで対応できます。
また、実際の需要と計画生産の間にズレが生じることがあります。これは需給のミスマッチと呼ばれ、顧客が欲しい商品が在庫切れだったり、逆に売れない商品が大量に残ったりする状況を引き起こします。この問題を解決するには、市場動向をこまめにチェックし、生産計画を柔軟に調整することが大切です。
常に在庫を抱えているため、在庫管理や保管にかかるコストが高くなる点も、プッシュ型のメリットと表裏一体な課題です。効率的な倉庫管理や在庫の適正化を図ることで、この問題を軽減できるでしょう。
プル型のメリットとデメリット
次に、プル型生産方式のメリット、デメリットも紹介します。
プル型のメリット
プル型生産計画の最大のメリットは、在庫の最適化とコスト削減にあります。顧客からの受注数量や納期に応じて生産計画を立てるため、余剰在庫が発生しにくくなります。また、在庫を最小限に抑えることができるので、物流倉庫などの余分な設備を抱える必要がなくなります。在庫保管のためのスペースが不要になり、ライン稼働のための電力・人件費なども削減できます。結果として、製品の原価を下げることにもつながります。
また、顧客満足度の向上も期待できます。プル型生産方式では必要な時、つまり顧客の需要に直接応じて生産を行うため、顧客が必要とするタイミングで製品を提供できます。
プル型のデメリット
一方で、プル型生産計画にはいくつかのデメリットも存在します。最も顕著なのは、需要変動への対応力の弱さです。あらかじめ確保しておく在庫が少ないため、需要の急激な増加に対応しにくい傾向があります。急な生産数の増加が難しいため、市場の急激な変化に即座に対応できない場合があります。また、生産ラインにトラブルが発生した場合、その停止時間分だけ製品の出荷が遅れ、直接ユーザーへの影響が発生する可能性が高くなります。 プル型生産計画は、効率的な在庫管理とコスト削減を実現できる一方で、需要の急激な変化や生産トラブルへの対応には課題があります。この方式を採用する際は、これらのメリットとデメリットを十分に考慮し、自社の生産環境や市場特性に適しているかを慎重に検討する必要があります。適切に運用できれば、無駄を最小限に抑えつつ、顧客ニーズに柔軟に対応できる効率的な生産システムを構築することが可能となります。
プッシュ型・プル型どちらにも対応できる生産スケジューラ
採用する生産方式によって、製造の現場は異なる課題に直面しています。在庫過多や需給のミスマッチ、生産計画の複雑化など、プル型もプッシュ型も一長一短。それぞれの課題を解決する強力なツールとして、生産スケジューラ「Asprova」をご紹介します。
Asprovaの特徴は、プッシュ型とプル型の両方の生産方式に柔軟に対応できる点です。効率の良い生産スケジューリングのためにAsprovaが重視しているのは、ボトルネックとなる資源を必要な時に必要な量だけ使用すること。こうした観点から材料や製品の在庫を適切に保ちつつ需要の変化にも迅速に対応できることを目指しています。また、生産リソースの最適化においても優れた性能を発揮します。人員、設備、原材料などの様々な制約条件を考慮しながら、効率的な生産計画を自動で立案します。
Asprovaの使いやすさも大きな魅力です。直感的なインターフェースにより、複雑な生産状況をリアルタイムで把握できます。納期遅れのリスクや設備の負荷状況などが一目で分かるため、迅速な意思決定と問題解決につなげる生産スケジューラです。
プッシュ型を導入する手順
製造業において、プッシュ型生産システムの導入は業務効率化の重要な戦略です。本記事では、需要予測から継続的改善まで、プッシュ型システム導入の5つの重要なステップについて詳しく解説します。
- 需要予測の精度向上
- 生産計画の策定
- 在庫管理
- 生産の自動化とITシステムの活用
- 継続的改善
1.需要予測の精度向上
プッシュ型システムは、いかに精度の高い需要予測ができるかにかかっています。正確な需要予測のポイントとしては、以下の3つが挙げられます。 まず、過去のデータ分析が重要です。販売履歴を詳細に分析することで、季節変動やトレンドを把握できます。たとえば、夏季に売上が伸びる商品や、年末に需要が高まる製品などのパターンを見出すことができるでしょう。
次に、市場調査を行います。顧客のニーズや市場動向を直接調査することで、予測の精度を高めることができます。アンケートやインタビュー、競合分析などを通じて、市場の実態を把握しましょう。
最後に、これらのデータを基に需要予測を行います。統計モデルや機械学習モデルを使用することで、より精緻な予測が可能になります。ただし、モデルの選択や運用には専門知識が必要なため、必要に応じて専門家のサポートを受けることをおすすめします。
2.生産計画の策定
精度の高い需要予測ができたら、次は具体的な生産計画を立てます。以下の3点がポイントです。
・生産スケジュールの作成 いつ、どれだけ生産するかを決めます。この際、設備のキャパシティや人員の配置、納期などを考慮に入れる必要があります。
・資材調達の計画 必要な原材料や部品を確保できるよう計画します。提携するサプライヤーとの良好な関係構築も大切です。
・人員の計画 生産に必要な人員を適切に配置することで、生産効率を最大化します。繁忙期には臨時スタッフの採用なども検討しましょう。
3.在庫管理
常に在庫がある状態のプッシュ型システムでは、適切な在庫管理が非常に重要です。
まずは、適切な在庫量を設定しましょう。過剰在庫はコストの無駄ですが、一方で在庫不足は販売機会損失を招きます。製品ごとの需要変動や生産リードタイムを考慮し、バランスの良い在庫数を設定します。
次に、定期的な棚卸です。実際の在庫と帳簿上の在庫を定期的に照合することで、在庫の正確性を保ちます。突然の欠品や過剰在庫といったトラブルの未然防止につながります。
最後に、在庫回転率の分析を行いましょう。在庫回転率は、在庫の効率的な利用を示す重要な指標です。この数値を定期的にモニタリングし、必要に応じて在庫政策の見直しを行いましょう。
4.生産の自動化とITシステムの活用
生産効率を飛躍的に向上させるには、自動化とITシステムの活用が欠かせません。
まず、自動化設備の導入を検討しましょう。ロボットや自動化ラインを導入することで、生産効率が大幅に向上します。初期投資は必要ですが、長期的には人件費の削減やミスの減少につながります。
次に、IoT(Internet of Things/モノのインターネット)の活用です。センサーを用いてリアルタイムで生産状況を把握することで、異常の早期発見や予防保全が可能になります。また、収集したデータを分析することで、さらなる改善点を見出すこともできるでしょう。
5.継続的改善
プッシュ型システムの導入は、一度で完了するものではありません。継続的な改善が重要です。
改善のための基本的な考え方として、PDCAのフレームワークを活用しましょう。計画(Plan)、実行(Do)、チェック(Check)、改善(Act)のサイクルを回すことで、システムの継続的な改善を図ります。
次に、従業員の教育に力を入れましょう。新しいシステムや設備の使用方法、効率的な作業手順などについて定期的な教育と訓練を行うことで、従業員のスキルアップと生産性の向上が期待できます。
最後に、現場の声を積極的に取り入れることが大切です。実際に作業を行う従業員の意見は、システムやフロー改善の貴重な情報源となります。定期的なミーティングやアンケート、ヒアリングなどを通じて、現場の声を吸い上げる仕組みを作りましょう。
まとめ
生産管理には、プッシュ型とプル型という2つの主要方式があります。プッシュ型は需要予測に基づいて計画的に生産を行い、プル型は実際の需要に応じて生産を調整することがポイント。どちらの方式も、在庫管理と生産効率の向上に重要な役割を果たします。
生産スケジューラを導入することで、これらのシステムの効果を最大限に引き出し、ビジネスの競争力を強化することができます。適切な生産計画を立て、継続的な改善を進めるために、生産スケジューラの導入をぜひご検討ください。生産スケジューラ導入によって具体的にどのような業務改善が実現したのかはこちらのページをご確認ください。

コラム編集部

最新記事 by コラム編集部 (全て見る)
- なぜこの2社は計画のブレを最小限にできたのか?精度向上のカギを解説 - 2025年7月2日
- “半日が10分に短縮”も可能に!属人化を脱し、計画作成を効率化した方法とは? - 2025年7月2日
- “なんとなく管理”からの脱却!デンカが語る、見える化による現場改善ストーリー - 2025年7月2日