シックス・シグマとは?製造業の品質向上と業務効率化のための手法を解説
2024.10.15A0 生産管理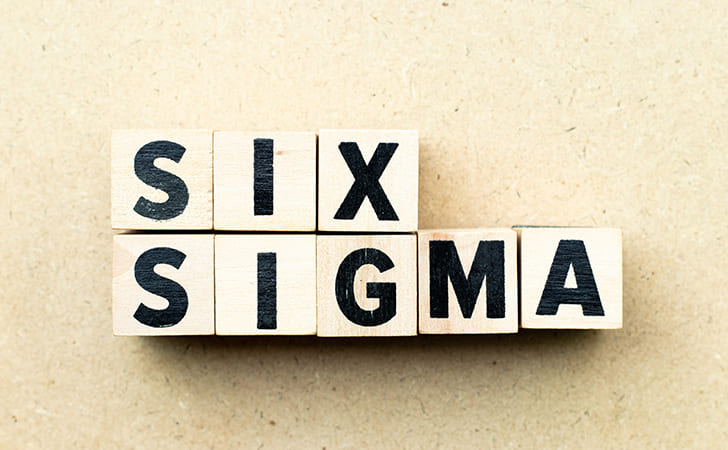
製造業において、品質管理は企業の競争力を左右する重要な要素です。その中でも「シックス・シグマ」は、統計学に基づいたデータ解析と体系的な手法を用いた手段で、品質向上と業務効率化を同時に実現する考え方として広く認識されています。
本記事では、シックス・シグマの基本概念から実施方法、導入のメリットなどを解説します。
【目次】
■シックス・シグマとは
■シックス・シグマの歴史と発展
■シックス・シグマの実施方法
■シックス・シグマ導入の課題とその克服方法
■製造現場の業務効率化の重要性
■まとめ
シックス・シグマとは
製造業における品質管理でよく用いられる手法の一つが「シックス・シグマ」です。ここでは、シックス・シグマの基本概念や目的、導入のメリット、そして他の品質管理手法との違いについて詳しく解説していきます。
シックス・シグマの基本概念と目的
「シグマ」とは、統計学で使われる標準偏差を表す記号で、プロセスのばらつきの度合いを示します。シックス・シグマの「シックス」は6を意味し、製品やサービスの品質が平均値から6シグマ(標準偏差の6倍)以内に収まることを目指します。これは、100万回の機会に対して3.4回未満の不良しか発生しないという、極めて高い品質水準を表しています。
また、シックス・シグマは単なる統計手法ではなく、品質管理のフレームワークとしての役割も果たします。この考え方は「DMAIC(ディーマイク)」と呼ばれ、後ほど詳しく解説します。
シックス・シグマの導入メリット
シックス・シグマを導入することで企業が得られるメリットについて、主要な3つを紹介します。
1.顧客満足度の向上
シックス・シグマの導入により、製品やサービスの品質を一貫して高め、信頼性を獲得できます。たとえば、自動車製造業では、エンジン部品の精度が向上することで、車の性能と耐久性が高まります。結果、顧客の期待を超える製品・サービスの提供が可能となり、顧客満足度が向上します。
2.コスト削減と収益改善
不良品の削減は、直接的なコスト低減につながります。たとえば、電子機器製造業では、基板の不良率を1%から0.1%に下げることで、年間数百万円の材料費と再工程費用を削減できる可能性があります。さらに、プロセスの効率化により、作業時間と資源の無駄が省けるため、生産コストが削減でき、企業の収益性が大きく改善されるでしょう。
3.業務プロセスの安定化と標準化
シックス・シグマの適用により、製造工程や管理方法といった業務プロセスのばらつきが抑えられ、製品の安定化と標準化が行えます。食品製造業を例に取ると、原材料の計量や調理時間のばらつきを最小限に抑えることで、常に同じ味と品質の製品を提供できるようになります。
シックス・シグマと他の品質管理手法の違い
品質管理の分野には、シックス・シグマ以外にも様々な手法が存在します。ここでは、特に注目されている2つの手法、リーンシックスシグマとトヨタ生産方式について、シックス・シグマとの違いを解説していきます。
リーンシックスシグマとの比較
リーンシックスシグマは、シックス・シグマの統計的手法にリーン生産方式の「無駄排除」の考え方を統合したものです。データに基づく意思決定と継続的な改善を組み合わせることで、より包括的なアプローチを提供します。シックス・シグマが主に品質向上に焦点を当てているのに対し、リーンシックスシグマは無駄のなさ、スピードと効率性をより重視しているのが特徴です。
トヨタ生産方式との比較
トヨタ生産方式は、「必要な時に、必要なものを、必要なだけ生産する」というジャストインタイム(JIT)生産を中心とした効率的な生産と在庫管理に重点を置いています。一方、シックス・シグマは統計的アプローチを用いて品質改善とプロセスの最適化を図るのが特徴。トヨタ生産方式が主に製造業での適用を想定しているのに対し、シックス・シグマは多様な業界で活用できる柔軟性を持っています。
シックス・シグマ | 統計学に基づく品質管理手法で、ばらつきを減少させることに重点を置く |
リーンシックスシグマ | シックス・シグマとリーン生産方式を組み合わせた手法で、ムダの排除とばらつきの抑制を通じて業務効率化を図る |
トヨタ生産方式 | トヨタ自動車が開発した生産管理手法で、JITと自働化を基本理念とし、持続的改善を重視する |
シックス・シグマの歴史と発展
シックス・シグマは、1980年代にアメリカのモトローラ社が開発した品質管理手法です。製造過程を分析して問題を特定し、改善して品質向上を目指すという考え方に基づいています。
その後、GEのジャック・ウェルチ氏が、この手法を全社的に導入したことでシックス・シグマは世界中で注目されるようになりました。現在では、製造業だけでなく、サービス業や金融機関なども、シックス・シグマを活用しています。日本企業の例では、ソニー株式会社や医薬品会社がこの手法を導入し、製品やサービスの品質向上に取り組んでいます。
このように、シックス・シグマは時代とともに進化し、様々な業界で活用される重要な品質管理手法となっています。
シックス・シグマの実施方法
シックス・シグマは、DMAIC(ディーマイク)と呼ばれる5つのステップで構成されています。DMAICとは、Define(定義)、Measure(測定)、Analyze(分析)、Improve(改善)、Control(管理)の頭文字を取ったものです。それぞれのステップについて詳しく見ていきましょう。
Define(定義):プロジェクトの目的と範囲
まず、顧客の声から取り組むべき課題を明確にしましょう。たとえば、「製品の不良が多い」という意見があれば、「不良率を5%から1%に減らす」といった具体的な目標を設定します。
次に、目標が決まったら、それを測る指標(KPI)も決めます。「生産にかかる時間を30%短縮する」や「良品率を95%から98%に向上させる」など、数値化した目標を立てるようにしてください。
最後に、プロジェクトを進めるチームを編成します。現場で働く方から管理職まで、様々な視点を持つメンバーに参加してもらうと良いでしょう。
【POINT】 目標を現実的な数値で設定すること
Measure(測定):現状のパフォーマンス
先ほど設定した目標を達成するための課題がどこにあるのか、数字で把握するステップです。現状を知るために必要な、正確な数値データを収集することが重要です。たとえば、1日の生産量、不良品の発生率、機械の稼働時間など、数値で得やすいデータを集めます。 また、数値データを集めたら表やグラフで可視化することで問題点を発見しやすくなります。
【POINT】 目標を達成するため、現状を数値で設定すること
Analyze(分析):データ分析と根本原因の特定
収集したデータを詳細に分析し、問題の根本原因を探ります。 たとえば、特性要因図(フィッシュボーンダイアグラム)を使って、問題の原因を整理してみましょう。特性要因図(フィッシュボーンダイアグラム)は、「人」「機械」「材料」「方法」「測定」「環境」の6つの観点から考えるため、見落としを減らせます。
また、5Why分析も活用します。「なぜ不良品が発生するのか」と質問し、その答えにさらに「なぜ」を5回重ねていくと、本質的な原因が見えてきます。
【POINT】 目標達成を邪魔している問題の本質を、データ分析によって特定すること
Improve(改善):改善策の実行
分析で特定した問題を解決するための方法を考えるステップです。複数の案を出し、それぞれの長所短所を比較しつつ、コストと効果のバランスを考慮して、最適な方法を選択しましょう。
選んだ方法は、小規模で試験的に実施し、効果を確認します。良好な結果が得られたら、本格的な実行計画を立案しましょう。
【POINT】 目標を達成するための解決策を、比較検討したうえで実行すること
Control(管理):改善の維持管理
改善した状態を維持できるように、常時モニタリングを行います。問題点や課題が出た場合は、プロセスを見直しましょう。また、業務プロセスは標準化することが大切。標準化することで、組織全員が改善に取り組み、状態を維持できるようになります。
【POINT】 目標を達成した状態を維持できるように、定期的にモニタリングしつつ標準化すること
シックス・シグマ導入の課題とその克服方法
シックス・シグマを導入する際には、いくつかの課題に直面します。ここでは、データ収集と分析の複雑さ、組織全体での理解と協力の必要性、適切な教育とトレーニングの重要性などについて解説します。
データ収集と分析の複雑さ
シックス・シグマの成功には、正確なデータ収集が欠かせません。製造工程のパフォーマンス指標や顧客満足度など、様々なデータを収集する必要があります。このためには、適切なITシステムやツールの導入が重要です。
たとえば、製造ラインの自動計測システムや顧客アンケートシステムなどを使って、データ収集を効率化する方法です。また、Minitabやジャンプ(JMP)などの統計分析ソフトは、複雑なデータ分析を行ってくれます。
組織全体での理解と協力の必要性
シックス・シグマを成功させるには、組織全体の理解と協力が不可欠です。全従業員を対象とした基本的な教育や、リーダー層向けの集中的なトレーニングを実施しましょう。
継続的な教育プログラムを用意し、シックス・シグマ手法に基づいたプロセス改善を効果的に行うための人材育成および認定をするベルトホルダー制度を導入することで、組織全体の品質改善力を高められます。また、部門を越えた協力体制を構築し、経営層のサポートを得ることも重要です。
適切な教育とトレーニングの重要性
シックス・シグマの資格制度は、プロジェクトの成功に大きく貢献します。特に、ベルトホルダー制度においてブラックベルトやマスターブラックベルトの資格保持者は、高度な統計手法やプロセス改善の知識を持ち、プロジェクトを効果的に推進できます。
各ベルト(ホワイト、イエロー、グリーン、ブラック、マスター)にも異なる役割があり、それぞれに適したトレーニングプログラムが必要です。これらのプログラムを通じて、従業員はシックス・シグマの原則を理解し、積極的に改善活動に参加できるようになります。
生産スケジューラAsprovaの活用方法
シックス・シグマを用いた生産管理に役立つのが、生産スケジューラ「Asprova」です。Asprovaには、資源ガントチャートによる生産計画の最適化や、在庫グラフによる在庫管理の改善など、様々な機能が搭載されています。
Asprovaを導入する際は、まず要件定義を行い、その後デモンストレーションや試用版での検証を通じて、具体的な導入計画を策定します。また、導入後も継続的なサポートを用意していますので、ITシステムの導入に不安がある現場でもご安心ください。Asprovaは、製造業の生産管理プロセスの悩みに寄り添い、業務効率化を実現するお手伝いをいたします。
製造現場の業務効率化の重要性
ここでは、製造現場における業務効率化のメリットや、効率化のための具体的な方法について紹介します。
業務効率化のメリットと影響
業務効率化は、コスト削減、生産性向上、品質向上という3つの主要な面で企業に大きなメリットをもたらします。
コスト削減
シックス・シグマの手法を用いた業務プロセスの改善と自動化の導入により、人手を介する作業を減らせます。これは直接的に労働コストの削減につながるでしょう。また、ジャストインタイム生産の導入による在庫の最適化は、過剰在庫の解消や材料費の削減を可能にします。
生産性向上
シックス・シグマのDMAIC手法を使って生産ラインのボトルネックを特定して改善することで、生産性が大幅に向上するでしょう。また、設備の故障データを分析し、予防保全と予測保全の仕組みを構築すれば、設備の稼働率が向上し、生産ラインの停止時間を最小限に抑えられます。
品質向上
シックス・シグマのDMAIC手法は、製造プロセスにおける品質の安定化と不良品率の低減に効果的です。品質向上は顧客満足度の向上にもつながり、企業の競争力強化に寄与します。
効率化のための具体的な方法
業務効率化を実現するため方法である、リーンシックスシグマ、デジタル技術の導入、メンテナンスの最適化について説明します。
リーンシックスシグマの手法
リーンシックスシグマは、プロセスの最適化と品質向上のどちらも目指す手法です。この手法は、ムダの排除と効率化を重視する「リーン」と、品質のばらつきを抑える「シックス・シグマ」を融合させています。
具体的には、5S活動(整理、整頓、清掃、清潔、躾)による職場環境の改善、カイゼンによる継続的な改善活動、そしてセル生産方式による効率的な生産システムなどが関連しています。
デジタル技術の導入
デジタル技術の導入は業務効率化に大きく貢献します。IoTを活用した機器のネットワーク化によるデータ収集と分析、AIを用いた予測分析、リアルタイムデータ分析による迅速な意思決定などが行えるでしょう。これらの技術は、シックス・シグマの各フェーズにおいて、より精度の高い分析や改善に役立ちます。
メンテナンスの最適化
予防保全による定期的なメンテナンス、設備の定期点検と保全計画の策定、データに基づく故障予知と保全(予測保全)は、設備の稼働率を向上させ、生産性を高めます。シックス・シグマの手法を用いてこれらのメンテナンス活動を最適化することで、さらなる効率化が期待できます。
まとめ
シックス・シグマは、製造現場の品質向上と効率化を実現する強力な手法です。データ分析と継続的改善を通じて、生産性の向上やコスト削減などにつながります。
また、この効果をさらに高めるには生産スケジューラの導入が効果的です。Asprovaの生産スケジューラは生産計画の最適化、自動立案、各工程のリソースの可視化といった機能が搭載されているため、本記事で紹介したシックス・シグマの各ステップをサポートします。両者を組み合わせることで、データに基づいた意思決定や業務効率化に役立ちます。 生産スケジューラ導入によって具体的にどのような業務改善が実現したのかはこちらのページをご確認ください。

コラム編集部

最新記事 by コラム編集部 (全て見る)
- なぜこの2社は計画のブレを最小限にできたのか?精度向上のカギを解説 - 2025年7月2日
- “半日が10分に短縮”も可能に!属人化を脱し、計画作成を効率化した方法とは? - 2025年7月2日
- “なんとなく管理”からの脱却!デンカが語る、見える化による現場改善ストーリー - 2025年7月2日