「急に内示が変更になった!」それでも在庫が増えないスケジュール調整
2022.10.04A1:生産計画・スケジューリング在庫管理を徹底しようにも不測の事態は起きるものです。たとえば内示にもとづいて作り始めたときに、注文数が減ったとします。この場合は減った分の製品を在庫にせざるを得ません。
在庫が過剰になる状況はキャッシュフローを悪化させる要因になります。会社としては在庫削減に取り組みたいところです。
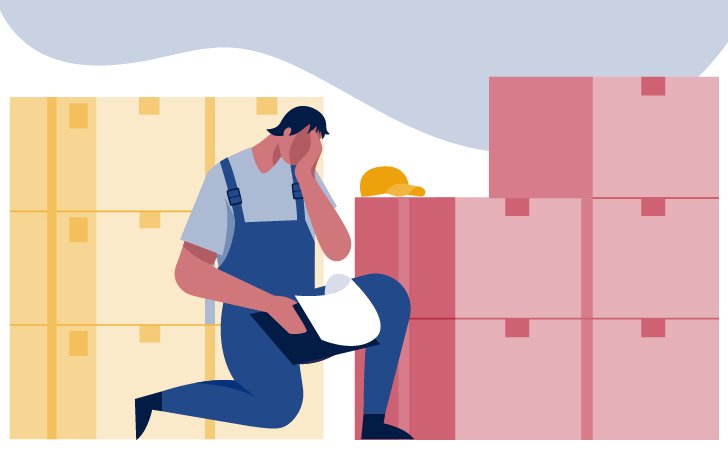
在庫の中でも削減するべきものとは
冒頭のケースでは、そもそもの内示変更が在庫増の直接的な原因です。とはいえ、内示自体は取引先にも関係することであり、自社だけで解決できる問題ではありません。
そこで、生産計画の側に問題はなかったかを考えます。
仮に電子部品を製造する企業で、A製品の注文量3万個、納期が1ヶ月後という内示があったとします。注文量からA製品のリードタイムは5日と計算。納期の3週間前に生産を開始するよう指示しました。
ところが、着手日から1週間後に内示が変更となり、2万個に減りました。A製品はすでに最終工程まで終わっていますから、当初の予定どおり3万個を在庫にするしかありません。1万個は受注に紐づかない在庫となるわけです。
この問題の引き金は内示変更ですが、見方を変えれば、必要以上に早く生産に着手したために、在庫が過剰になったとも考えられます。
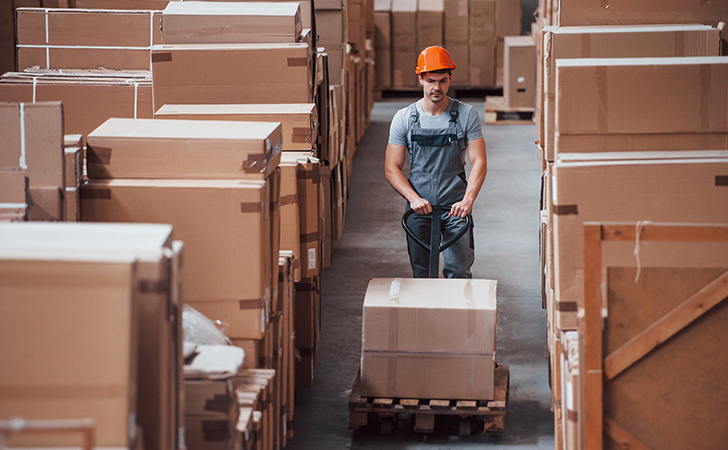
在庫問題と言った時にまず対策すべきは、例のような「計画的に作っていない在庫」をいかに減らすかです。そのために欠かせないのが、綿密なスケジュール調整となります。
在庫を増やさない生産スケジューラ
計画的に作っていない在庫を減らすには、納期に近いタイミングで生産に着手することです。しかし、人間でこれをやろうとするとうまくいきません。余裕を見すぎるあまり、前詰めで生産計画を立ててしまうからです。
人間だけでさまざまな要件を考慮して計画を立てるのは難しいもの。であればシステムに頼るのも一つの手であり、その一つが生産スケジューラの導入です。
生産スケジューラは、後工程から前工程へとさかのぼって生産計画を立てていきます。これを「バックワードスケジューリング」と言い、一方の着手可能日から前詰めで計画を立てることを「フォワードスケジューリング」と言います。
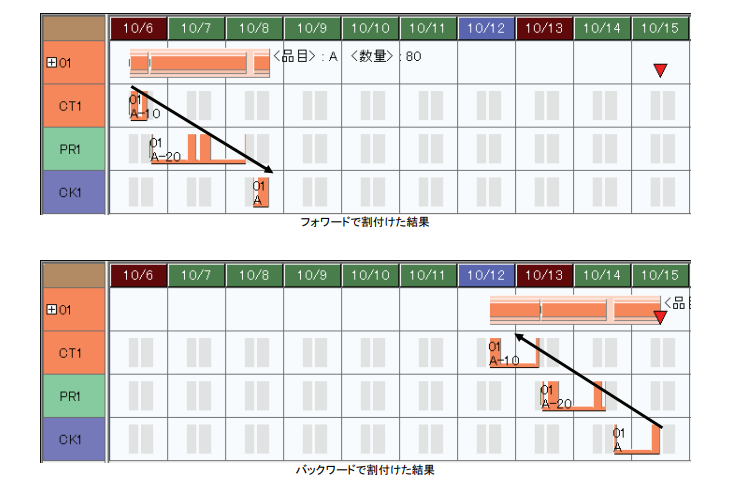
バックワードスケジューリングの場合、納期から逆算して最適な着手日を決めるので、納期に近いタイミングで生産に着手することが可能です。前述の例ではリードタイムが5日ですから、着手日は納期から7日前あたりが適しているでしょう。生産スケジューラはこのような計画を、多種多様な製品の組み合わせから瞬時に決めてしまいます。
また、生産スケジューラを用いて生産計画を組んでいくと、リードタイム短縮にもつながります。工程の待ち時間が短くなることで、仕掛け品を削減することもできるのです。
在庫管理が難しいのは、内示変更や営業からの注文量変更などの不測の事態にも対応しなければならないところです。生産スケジューラなら柔軟なスケジュール調整が可能なので、その一助となるでしょう。
- 在庫に関するさまざまな記事をナレッジセンターにてご覧いただけます。
(会員登録が必要です)

コラム編集部

最新記事 by コラム編集部 (全て見る)
- 納期管理~生産スケジュールの最適化による納期厳守率の向上 - 2025年4月14日
- スケジューリング技術の応用による生産性の改善 - 2025年4月14日
- Lean Manufacturing~生産スケジューラの活用で最適な生産を - 2025年4月14日