【可動率(べきどうりつ)の基礎知識】稼働率との違い・可動率を向上する方法とは
2024.11.19A1:生産計画・スケジューリング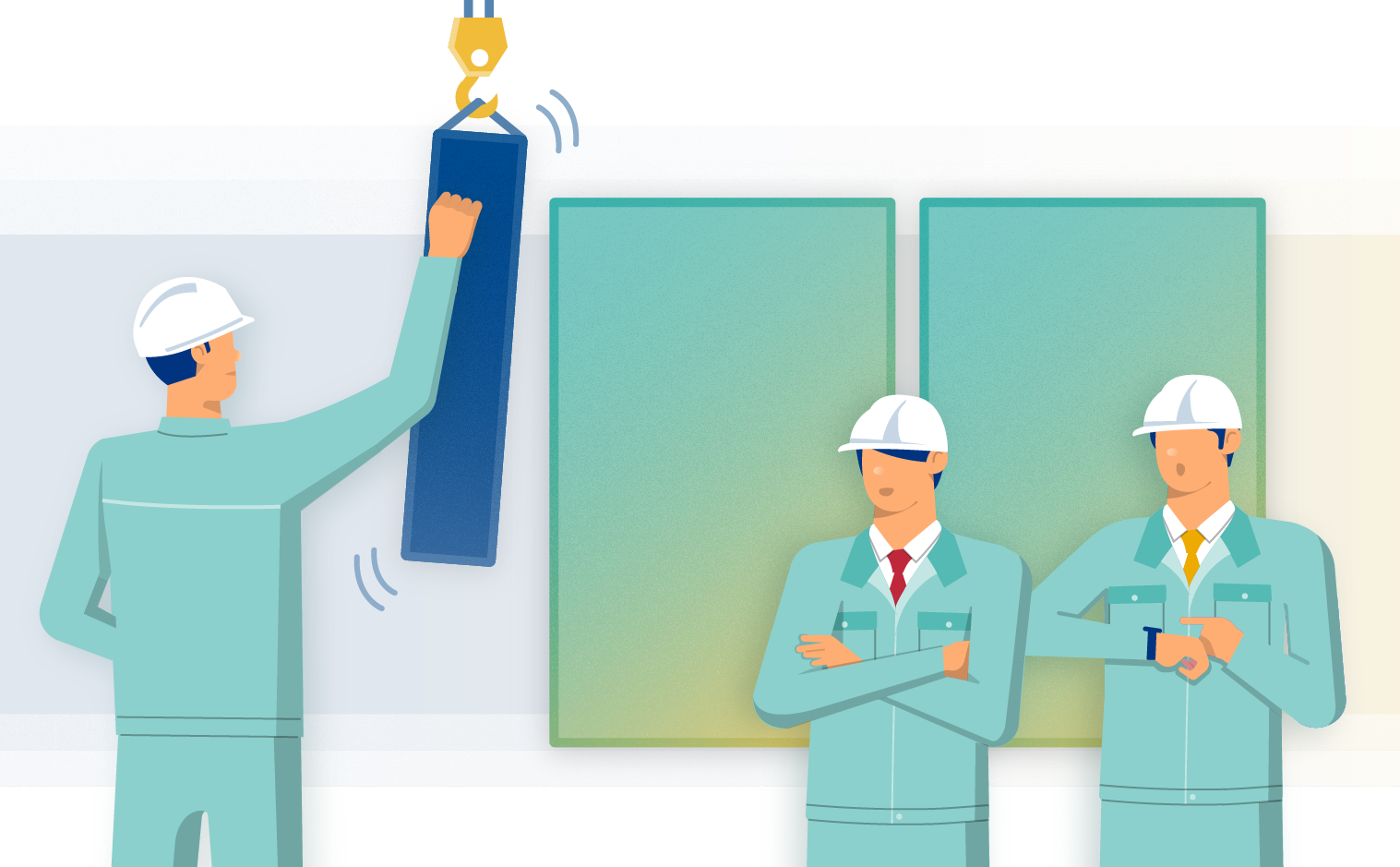
この記事では、可動率(べきどうりつ)を向上させる基本的な取り組み方を理解するために、可動率の定義や稼働率との違い、具体的な改善方法を詳しく解説しています。 可動率と稼働率のどちらの指標を目指すべきか、両者をしっかり区別して、効果的な生産管理につなげられるようにしましょう。
【目次】
■可動率とは?
■可動率を向上させる基本戦略
■可動率を向上させるメリット
■可動率が向上しない原因
■業務効率を上げるために、可動率を見直しましょう
可動率とは?
可動率とは生産設備が正常に動作している時間の割合を示す指標で、設備の「運転効率」を測るために使用されます。
可動率が高いと生産スケジュール通りに作業が進み、設備などにトラブルもなく生産が効率よく行われていると分かります。逆に可動率が低い場合、生産スケジュールや設備にトラブルや故障が多く、運転効率に問題があるということです。製造時間の中でなるべく多く生産物を増やすために、100%を目標にすることが必要です。
一方、稼働率は、製品の「生産効率」を表しており、生産計画の達成度や設備の利用効率を評価するための指標です。 両者の違いを理解することで、効果的な生産管理が可能になります。
可動率の定義と稼働率との違い
可動率は、設備の正常な「稼働時間の割合」を示すもので、スケジュールの不備や設備の故障、メンテナンスなどによって作業が停止した時間の影響を受けます。
一方、稼働率は、生産計画に対する「実際の稼働の割合」を示すもので、生産能力に対してどのくらい生産できたかを測るために使用される指標です。そのため、可動率を求める場合は時間が基準になるのに対し、稼働率は生産量と時間の両方で示すことができます。
可動率の計算式
可動率は製造時間に対する設備の運転効率を表す指標のため、時間を基準にして求めます。操業時間におけるメイクスパン(作業のリードタイム)のうち、実際に製造した時間がどのくらいかで数値が異なります。
たとえば、メイクスパンが6時間の製造現場において、段取り替えや材料待ち、金型待ちなどの理由により製造時間が3時間だった<>場合、可動率は3÷6時間×100%で50%となります。
可動率……実際の生産時間÷正常時の生産時間×100%
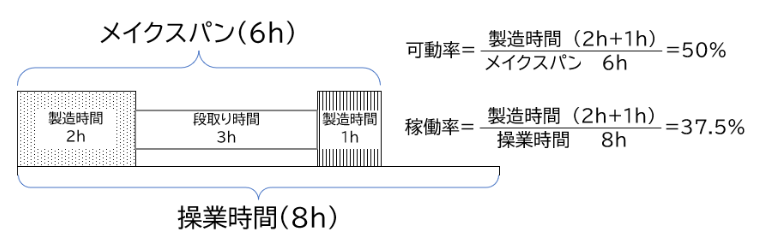
稼働率の計算式
稼働率を求めたい時、以下のように「製造量基準」と「時間基準」の2つで測ることができます。
- 生産量基準の稼働率……実際の製造数÷生産能力の生産数×100%
- 時間基準の稼働率……実際の製造時間÷操業時間×100%
稼働率を製造量基準であらわす時、たとえば、1日に100個の製品を作れる設備で95個を作った場合の稼働率は95%となり、110個作った場合は稼働率110%となります。
時間基準であらわす場合は、操業時間に対する実際の製造時間から求めます。操業時間が8時間の工場において、設備や人員が実際に動いていた生産時間が7時間だった場合、この時の稼働率は7時間÷8時間×100%=87.5%です。
このように、稼働率は受注が増えた場合に100%を超えることもあり、設備やスケジューリング以外にもオーダー数量によって影響を受ける指標です。 製造現場のメイクスパン(リードタイム)における製造効率を上げるためには、受注の増減に影響を受けない可動率のほうを高めることが重要だと分かります。
可動率を向上させる基本戦略
可動率を向上させるには、生産現場の運転効率を上げる必要があります。そのためには、常に人や設備が稼働している、スケジュールに遅れやムダがなく、スムーズに生産を進めることが大切です。
設備メンテナンス
設備や機械のトラブルは可動率だけでなく稼働率の低下原因にもなるため、設備の定期的な点検とメンテナンスは生産性向上の基本です。設備の故障やエラー、老朽化や劣化を防ぎ、常に正常稼働させるためにも、メンテナンス計画を策定しましょう。
設備メンテナンスには「定期」「予防」「事後」の3種類があります。不具合や故障が起きやすいことが分かっている部品や場所は、こまめな定期メンテナンスで稼働停止を防げます。
予防メンテナンスには設備の劣化を防ぎながら予期せぬトラブルを防ぐ効果があり、それでも設備に故障や停止が起きた際には事後メンテナンスで対応します。
メンテナンスで実施する作業を決定・分類し、それぞれのメンテナンスマニュアルを作成したら、各メンテナンス時間を決定します。リードタイムにメンテナンス時間が使われることにならないよう、前もって実現可能な作業時間を決定しておきスケジュールに反映しましょう。
データ分析の導入
可動率の向上には人や設備が正常に稼働する割合を上げることも大切ですが、その工程に入った時に時間のムダやロスがなくすぐに仕事に取り掛かれるかも大切です。
どの時間がムダになっているか、作業に入るまでの時間をどう効率化できるかを考えるために、データの収集・分析を行います。具体的な分析方法のひとつに稼働分析があります。人や機械がどのような要素にどれだけ時間をかけているかを明確にするための分析方法で、それぞれの要素において時間が変動する要因を分析し、より安定した稼働を維持するために役立ちます。
データ分析を行うなら、専門ツールの活用も効果的です。生産現場のセンサーやカメラ、PLCなどの収集データから生産ラインの状況を見える化し、作業の進捗や非稼働時間、ロス時間を認識して不稼働の要因を自動分析できる製造業向けツールもあります。
予防保全の導入
予防保全は、想定外のトラブルで設備・装置の正常稼働にダウンタイムを生じさせて、生産性が低下することを防ぎます。
適切な予防保全が行われていると、設備が突然稼働中に停止して、生産に悪影響を及ぼすリスクを低下できます。現場で働く従業員の安全性を維持するリスクマネジメントとしても有効です。
予防保全でまず行うのはスケジュール策定です。メーカーが提示する使用回数や期間、現場の保全担当者の知識・経験をもとに適切なスケジュールを策定しましょう。
次に、担当者によって判断にばらつきが生じたり想定外のトラブルが起きたりしないよう、保全基準を明確にします。いつ、誰がどのように予防保全を実施するかを定めてマニュアル化しましょう。作業の抜け漏れを回避するためにも、保全スケジュールの策定と共有、保全基準の明確化、手順のマニュアル化のステップに沿って保全業務を行うようにしてください。
人材のスキルアップ
従業員のスキルアップは、可動率向上に欠かせません。生産現場においては設備と人の連携が必要であり、従業員の対応作業に時間がかかったり対応開始までに時間をとられていたりすると、設備の稼動率を下げてしまうからです。たとえば、機種の扱い方に不慣れな作業者がラインに入ると、設備の動作スピードや作業スピードが遅くなることで速度低下を招きます。
人が原因で設備の動作や作業スピードを落とさないためにも、従業員への教育体制やトレーニング環境を整えましょう。メーカーが実施するセミナーや講習に参加してもらう、1人で複数の業務を遂行できる「多能工」の育成に力を入れるなどが有効です。従業員1人ひとりのスキル管理を行うことも、現場における人材が持つスキルの把握と効率的な育成につながります。
生産スケジューラの活用
生産スケジューラを活用すれば、設備の最適な稼働計画を立案し、メンテナンスのスケジューリングと稼働時間の調整を通じて可動率を最大化できます。
可動率を向上させるためにできる複数の取り組みを一度に進められる他、現場に精通した従業員でなくても生産計画の立案・変更ができるため、施策の立案から実行までの業務も効率的です。
たとえば、現場における部品や金型ごとで異なる上限使用回数なども正確に管理が可能です。金型の欠損や設備の不具合が発生した際には、その情報を反映し、スケジュールを調整することができます。また、事前に予定されたメンテナンスについては、非稼働時間として計画に組み込むことが可能です。
可動率を向上させるメリット
適切なスケジュール管理や保全・メンテナンス管理、人材管理によって可動率が向上すると、以下のようなメリットを得られます。また、これらのメリットを最大限に活用すると企業全体の競争力強化にもつながります。
コストを削減できる
可動率を向上するために、定期的なメンテナンスや予防保全を行うことによって、故障やメンテナンスによるダウンタイムが減少します。設備の突発的な修理費用や生産停止による損失が抑えられるため、結果としてコスト削減につながります。
品質が向上する
常に設備が安定稼働していることにより、製品の品質が一定に保たれやすくなります。また、安定稼働によって品質管理の効率が上がることで、より品質を向上させるためにリソースを割けるようになるでしょう。
従業員の満足度が向上する
安定した設備稼働は作業環境の改善にもつながり、従業員の作業負担を軽減します。設備の故障やトラブルによる追加作業や残業なども減らせる他、現場管理者の生産スケジュール計画や管理もスムーズになるでしょう。これにより、従業員のモチベーションが向上します。
環境への配慮になる
効率的な生産計画と設備運用により、待ち時間やムダな稼働時間が削減されて、現場のエネルギー消費が最適化されます。余分なエネルギーの削減は、環境負荷の低減につながります。
可動率が向上しない原因
可動率が向上しないのは、設備の故障やトラブルによる稼働停止だけではありません。可動率が向上しない生産現場では、以下のような様々な要因が絡んでいるケースがあります。
無駄な業務の存在
生産プロセスに無駄な作業や非効率な工程、例えば段取りの多さなどが含まれていると、それがボトルネックとなり、設備の可動率が低下します。段取りが増えることで稼働が停滞し、作業時間が長くなる場合があります。このような現場では、無駄な作業が発生していないか、非効率な業務になっていないか、作業手順や計画を見直し、原因を明確にすることが重要です。改善点が見つかった場合は、すぐにチーム間で共有し、現場全体の改善に取り組みましょう。特に生産スケジューラを活用することで、段取り時間を減らすように効率的な計画立案を行うことで、可動率の向上につながります。
コミュニケーション不足
部門間の連携が不足していると、情報共有が滞り、計画通りの生産が難しくなります。たとえば、生産部署と部品を調達する部署間のコミュニケーションが不足していると、不要な部品の過剰発注などにつながり、コスト増大や利益低下を招く原因にもなります。このような現場では、定期的なミーティングやデジタルツールの活用によってコミュニケーションを改善する施策が必要です。
資源の不足
必要な資材や人材が不足していると、当初の計画通りの生産ができず設備の稼働率が低下します。材料不足によって追加発注を余儀なくされると、材料が届くまでの待ち時間が生じて時間のロスにつながるためです。
このようなロスが何度も発生すると、現場のみならず事業単位での生産計画に大きな影響を与えてしまいます。
常に安定した資源を維持するためにも、適切な資源管理と調達計画を立てることが重要です。
標準化不足
作業手順や管理方法が標準化されていないと、作業のばらつきが生じやすくなります。作業手順があいまいなままになっている現場では、配置される要員が変わるごとに設備の動作や作業スピードが低下するため、効率的とは言えません。ベテラン社員が離職し、経験が浅く設備の扱いに慣れていない社員の割合が増えた場合、品質が安定せず生産性が低下するおそれもあります。
作業のばらつきや人材による生産のムラが起きている現場では、作業が標準化されているかを確認し、作業手順書がないようであれば作成して、全員が同じ手順でスムーズに作業できるような環境を整えることが必要です。
業務効率を上げるために、可動率を見直しましょう
業務効率を向上させるためには、設備の可動率を見直すことが不可欠です。可動率が低いと、設備のダウンタイムが増えて生産性が低下し、無駄なコストが発生するだけでなく業務全体の効率が悪化してしまいます。
また故障やエラーを防ぐためには、定期的なメンテナンスが欠かせません。
さらに、人や設備が滞りなく稼働するには、メンテナンスによる設備の安定維持以外にもスケジュールに遅れやムダがなく、スムーズに生産できているかも重要です。
設備メンテナンスを含めた全体の生産スケジューリングと稼働時間を調整することで、可動率をより最大化することにつながります。
アスプローバの生産スケジューラは、製造現場における生産スケジュールを包括的にサポートするシステムです。可動率を向上させるために取り組むべき施策が複数ある場合でも、各プロセスのスケジュールを踏まえた上で最適化し、効率よく実施できるよう提案します。
メンテナンスにかかるスケジュールも見越した上で生産計画を立てられるので、依存関係にある工程の改善や業務のムダの発見・見直しにも役立ちます。
生産スケジューラ導入によって具体的にどのような業務改善が実現したのかは、こちらのページをご確認ください。

コラム編集部

最新記事 by コラム編集部 (全て見る)
- 困ったこと35~作業指示と無関係に作業する人がいて困った - 2025年4月23日
- 困ったこと35~一生懸命やっているのに、理解してもらえなかった - 2025年4月23日
- 困ったこと35~「何でもできる」と思い込んでいる人に困った - 2025年4月23日