欠品をなくすための対処法とは?欠品で起こるデメリットや起きた際の対処法まで解説
2024.06.24A1:生産計画・スケジューリング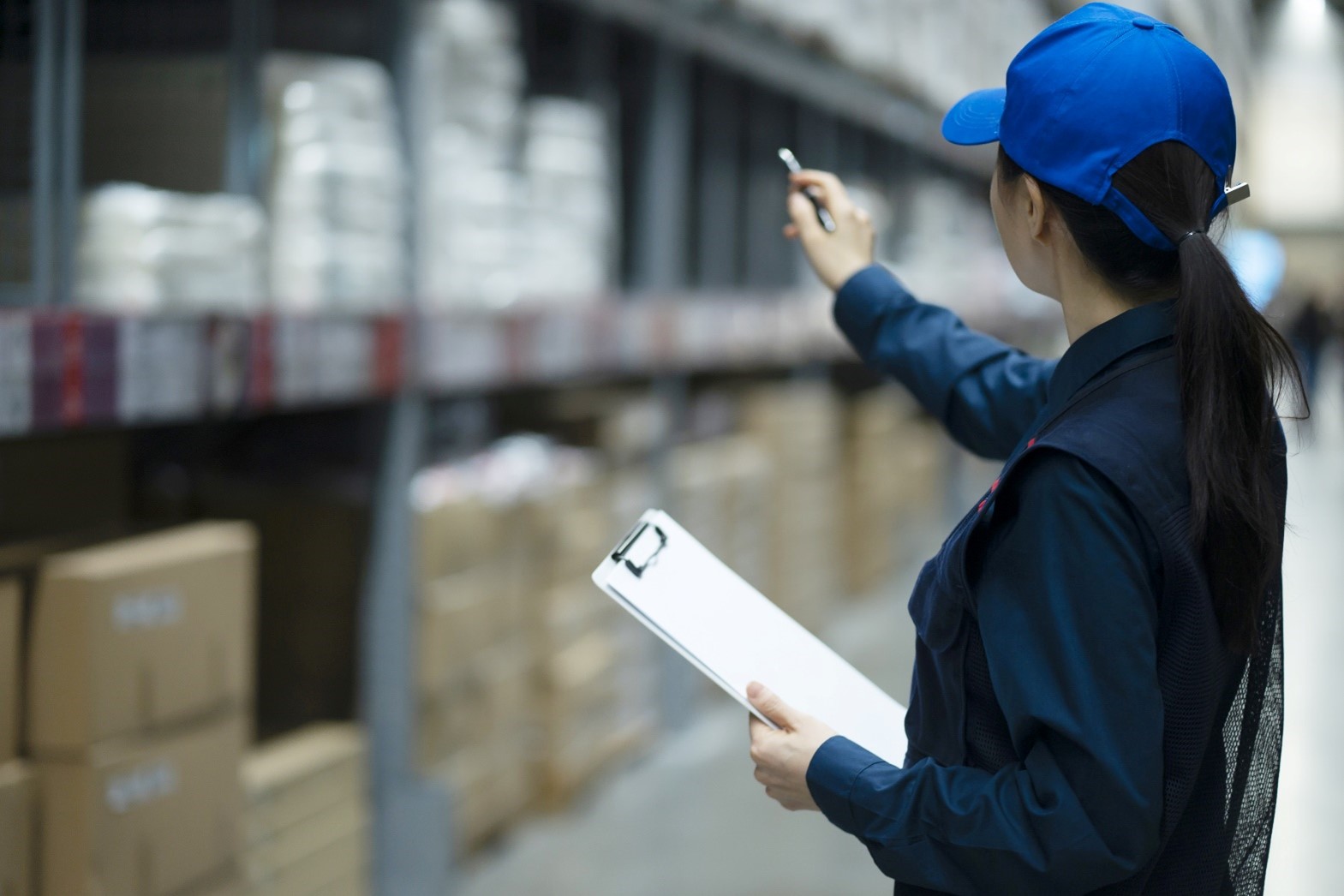
製造現場では「なぜ欠品が起きてしまうのか」「どう対処すれば欠品をなくせるのか」というように頭を悩ませている責任者も多いでしょう。本記事では、製造現場での欠品をなくすための在庫管理の徹底や、欠品するとどのようなデメリットが起こるのか、欠品が起きてしまった時の対応法などもご紹介していきます。ぜひ最後まで読み、在庫管理の参考にしてください。
【目次】
■欠品とは
■欠品を起こさないための対処法
■欠品すると起こるデメリット
■生産スケジューラは「欠品」をなくす在庫管理そのもの
■まとめ
欠品とは
製造現場で多く発生する欠品とは顧客から発注された注文数に対して、現物の数量が足りないという状態です。欠品の場合には、仕入れ先や他店舗から再入荷や補充ができる可能性があります。一方、在庫切れは「店舗での商品が完売してしまい、仕入れ先にも在庫がない」という状態です。在庫切れの場合には、再入荷される時期が分かっていれば、その時期を待たなければならず、再入荷されない場合には他の商品で代替しなければなりません。欠品は店頭にはないが在庫はあるという状態で、在庫切れは店頭にも在庫にもないというのが違いになります。
欠品を起こさないための対処法
欠品が出てしまうのには、さまざまな要因があります。ここでは、どのような工夫をすれば欠品を防げるのか、5つの対処法をご紹介します。5つの対処法を理解し、欠品を起こさないための行動を起こせるようにしましょう。
- 在庫の整理整頓
- 入出庫時の確認の徹底
- 適正在庫の確認
- システムを導入する
- リードタイムを含めて考える
在庫の整理整頓
在庫の整理整頓は欠品をなくすために必要なことです。在庫が整理されていないと、商品を探す手間がかかってしまったり、誤って在庫を出庫したりしてしまうリスクがあります。整理整頓のコツは「どこに何が置いてあるか」を明確にすることです。置き場所が分かれば必要なものがすぐに探し出せ、作業効率向上にもつながります。
入出庫時の確認の徹底
入出庫時の確認も欠品を起こさないための重要な要素です。検品等が属人化されていたり、マニュアルがなかったりすると対応者が個別に判断することになります。業務が属人化してしまうと、ルールが守られず、きちんと確認できていないため、必要なものがないのに気付けないといった事態が生じます。しかし業務が属人化されておらず、入出庫の確認を常に行っていれば、欠品を防ぐことが可能です。業務に慣れてくると、自分の経験で作業をしたり、マニュアル通りに業務を進められなくなることがあります。そのような状況に陥ると、各業務が省略化されてしまい、入出庫の確認を怠ってしまうこともあるでしょう。結果的に、商品の欠品が起こりやすくなってしまいます。商品の欠品が起こらないように、入出庫時の確認は徹底するようにしましょう。
適正在庫の確認
欠品を起こさないためには、需要予測を立てて必要な在庫を確保することが重要です。欠品を恐れるあまり過剰在庫になった結果、在庫が余る状態になっては管理にかかるコストが発生してしまいます。欠品も過剰在庫も起こらないように、どのくらいの数があれば、急な発注がかかっても対応できるかを知っておくようにしましょう。定期的に棚卸があることで、自社に適した在庫数を知ることができます。棚卸の際に自社に適した在庫数を把握し、適正な在庫数になっているかこまめに確認することで、欠品を防ぐことが可能です。
システムを導入する
在庫管理をスタッフがしている場合、かなり手間のかかる作業になり、在庫管理を正確にするのが難しくなります。また、ノートやエクセルを使用するアナログな管理方法では、ミスが発生しやすかったり、常に最新の在庫データを知ることができなかったりと問題が起きやすいです。そのため、担当者の手間を最小限に抑えながら正確に在庫管理をするためにはシステムの導入が必要です。在庫管理や入出庫管理ができるシステムなどを利用し、デジタルに在庫管理することで、欠品をなくす手助けになります。デジタルな在庫管理では、バーコードリーダーを活用することで、読み取ったデータを基に在庫データを最新の状態に保つことも可能です。最新の在庫データを常に把握できれば、入出庫管理の精度も上げることができるでしょう。
リードタイムを含めて考える
欠品をなくすためにはリードタイムも含めて考えた在庫管理が必要です。リードタイムとは、商品を注文して入荷するまでの期間を指します。リードタイムが短い場合には欠品が起こりづらく、機会損失もしづらいので特に気にすることはありません。しかし、リードタイムが長い場合には、一度に大量の商品を受注することが必要になります。その結果、過剰在庫を抱えるリスクが高くなり、在庫管理に手間がかかってしまうでしょう。そのため、できるだけリードタイムを短く設定する工夫が必要になります。
欠品すると起こるデメリット
欠品すると起こるデメリットは主に以下の4つです。前章では、欠品を起こさないためにどのような対処法があるのかを説明しました。それでは、ここでは、欠品すると起こるデメリットについて解説します。
- 販売の機会を失う
- 顧客満足度が下がる
- 過剰在庫になる
- 管理担当者の負担が増える
販売の機会を失う
商品が欠品してしまうと、販売の機会を失ってしまいます。なぜなら売れ筋商品であっても欠品が発生すると、販売の目途が立たなくなるからです。売れ筋商品であれば、常に店舗に在庫があればそれなりの販売を見込めるでしょう。しかし、商品が欠品すると、販売目途が立たなくなり、その結果立大きな利益損失にもつながります。そのような状況にならないために、売れ筋商品だけでなく、すべての商品において在庫管理を徹底しましょう。
顧客満足度が下がる
商品の欠品を起こし、販売の機会を失うと、当然ながら顧客満足度が下がります。人気商品であればなおのこと、商品の販売を楽しみにしていた顧客の期待を裏切ることになるからです。買いたい商品が店舗に置かれていないと、店舗の品ぞろえが悪いというイメージにつながります。その結果、顧客満足度が低下し、クレームにつながったり他のライバル店舗に顧客が流れたりする事態になるでしょう。顧客の満足度を維持するためにも、在庫数を把握して常に適正な在庫数を保てるように在庫管理を徹底しましょう。
過剰在庫になる
欠品を多く発生させてしまうと過剰在庫になってしまう恐れがあります。担当者が欠品をなくしたいという気持ちが先走ってしまい、多めに商品を発注してしまうと、本来必要な予想数を大幅に上回った数の在庫を抱えてしまいかねません。注文数の多い商品であれば、多めに発注しておいても功を奏することもあるでしょう。しかし、予想に反して発注数が少なかった場合は、かなりの数を余らせてしまいます。特に、シーズン物などを発注する場合には、発注時点でどんなに売れていてもシーズンが終わったら売れなくなるということを考慮しなければなりません。過剰在庫になってしまうと、その分コストがかかるなど、在庫以外でもデメリットが出てきてしまいます。そうならないためにも在庫管理を徹底し、欠品も過剰在庫も起こらないようにしましょう。
管理担当者の負担が増える
商品が欠品してしまうと、管理担当者の負担が増えてしまいます。なぜなら、欠品が出れば、その対応を余儀なくされるからです。管理担当者は欠品が出てしまった商品の発注をかけるだけでなく、いつ、どの段階で欠品が起きていたかなどをもう一度洗い出さないといけなくなります。商品の欠品が起こる原因は、在庫管理がシステム化されていない管理体制にあります。在庫管理がシステム化されていれば、常に最新の在庫データを把握できるため、欠品が起こる前に商品を発注することが可能です。しかし、アナログで在庫を管理していると、最新のデータを常に把握するのが難しいため、欠品が起こりやすくなってしまいます。欠品が起きてしまい、管理担当者の負担が増えることがないように、システムを導入するなどの工夫をしながら在庫管理を徹底しましょう。
欠品が起きた時の対応方法
ここまでで欠品が起きることで被るデメリットや欠品を起こさないための対処法を解説してきました。これらの情報を参考に欠品対策を講じていても、欠品が起きてしまうことはあります。そうなってしまった場合、何をすればいいか分からなくならないために、ここでは欠品が起きてしまった際にするべき対応を解説します。
謝罪
欠品が起きた場合、取引先への謝罪は忘れてはいけません。お詫びをする際には、発注された商品が品切れである事実を伝え、現在どのような状況であるかを踏まえ、今後の対応を相談しましょう。取引先も、欠品の事実を知った上で、「次回からこうしてほしい」といった提案があるかもしれません。取引先の提案を聞いたら、その場でしっかり確認を取りましょう。その場で確認を取ったら、すぐに取引の提案に対する回答をお伝えすることが重要です。そうすることで、次回以降も継続して取引先に発注していただくことができるでしょう。
次回入荷予定の有無
欠品が起きてしまった場合でも、取引先によっては再入荷を待ってもらえることがあります。謝罪の時には現在の状況を踏まえた上で、次回の入荷予定の有無を必ず伝えましょう。再入荷の見通しがあれば、不服ながらも待ってもらえる場合があります。入荷の予定がない場合は、欠品した商品と似た代替品を提案してみるのがおすすめです。
入荷が無い場合の返金や代替品での対応
次回入荷の目途が立たない場合には、取引先への返金や代替品での対応をしましょう。いずれの場合も、先方からキャンセルを求められたら、無理に待ってもらえるように説得するのではなく、速やかに返金処理の対応を取ることが重要です。もし、発注されていた商品のイメージに近いものがあれば、代替品として提案してみる対応を取ってみるのもいいでしょう。入荷の予定がない場合に謝罪するだけで終わってしまうと、取引先は在庫のある企業からの入荷を考えるでしょう。自社以外の企業がいい条件で早く納品する場合には、そのまま契約を終了し、他社と取引を開始してしまうかもしれません。そのため、できないことは諦めが必要ですが、自社でできる最大限の行動を起こすことが重要です。生産スケジューラは「欠品」を無くす在庫管理そのもの
「コンビニ」は「トヨタの生産方式」と同様の概念で、「ジャスト・イン・タイム」を実践し、社会の無駄な在庫を大幅に削減しています。スペースのない日本社会の生活ではジャストフィットです。そうです、社会システムを「在庫管理」で捉えると、よく理解できるのです。 生産管理は大きく全体から見て在庫管理システムであり、材料購入・販売現場はもちろん、生産工程のどこに焦点を当てても、在庫管理システムそのものです。最大に大きく見て、MR(マーケットリサーチ)で想定される販売予定数量を「有効数(引き当てされていない在庫数と見るのが通常)」として見ると、企業は巨大な倉庫です。
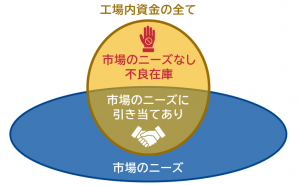
生産工程に焦点を絞ってみると、生産工場内にある全てが在庫管理であると言えます。生産管理はもちろん、生産技術、工程管理も全ては在庫管理で包括することが出来ます。在庫量を極限し、ライン停止を招く「欠品」を無くし、生産効率を最大限に効率化することを目指して、「生産スケジューラ」が使われます。
「生産スケジューラ」の目指す基礎数字は、「販売予定数」です。つまり「市場のニーズ」を目指すのであり、製造業の全資金は、この「市場のニーズ」に「引き当てられている(予定されている)」ことが究極です。
【「欠品」にも等しい「過剰在庫」の大失敗の事例】
ある建設車両メーカーの50年ほど昔の大失敗事例です。50年ほど昔は、現在の情報管理に比較して、ネット通信もなく、事務処理においても手作業が多く情報整理が遅れていました。そこに不況が来て製品の販売数が減り始めたのですが、その割に完成車在庫が増えないので、工場責任者は安心していました。一方、販売店サイドでは日増しに在庫が増え、ついに工場への減産要求が厳しくなってきた時、工場従業員が総務部に苦情を上げてきました。
「クラブ活動で、グラウンドを使用できないから何とかしてくれ」と言うのです。総務部員と工場長がグラウンドの実情を見に行くと、なんと完成車在庫で埋め尽くされているのです。そこで在庫管理の帳簿を見ると、「販売店在庫」となっていました。
工場側では販売店に在庫を押し付けており、帳簿上は在庫を少なくしていたのですが、押し付けられた販売店側はスペースがないので「工場預け」としていたのです。つまり、大失敗の「過剰在庫」が判明したのです。在庫管理の不首尾で多大な作り過ぎを起こし、倒産の危機に直面しました。 この事例から分かるように、在庫管理は帳簿処理とかデータ管理ではないのです。「在庫を管理」する上で重要なことは、「経営者たるもの現場に立て」の格言です。
【効率化の技術は「工程結合」】
生産現場の「セル生産方式(通称:屋台)」は工程結合であり、結合された工程間の中間在庫がなくなっています。よく考えてみれば、材料と加工工程が離れているなどはムダな運搬が生じるだけです。二重に置き場所が必要になるだけの組み立てラインと部品製造工程が離れていることもムダなことです。 生産工程の結合で、中間在庫や置き場所を無くし、リードタイムを短くすることが普通と見るべきでしょう。
「工程結合」が、生産管理・生産技術では切り札なのです。工程間在庫を仮想の倉庫内と見立てれば、過不足ない「ジャスト・イン・タイム」を「生産スケジューラ」が実現します。 つまり、生産工程の「過剰在庫」を無くし、ライン全体を止めてしまう「欠品」を起こさないための工程管理者の武器が「生産スケジューラ」と言えます。
生産スケジューラを導入して欠品を最小限に抑えよう!
欠品とは、店舗から在庫がなくなってしまったが、他店舗や仕入れ先には在庫が残っている状態のことです。欠品が起きてしまう要因には、在庫が整理されていないことや、需要予測が見誤りってしまったこと、システムが導入されておらずアナログで管理されているような適切でない生産管理体制などがあります。欠品が起きてしまうと、販売機会を失ったり顧客満足度が下がったり、管理担当者の負担が増えてしまったりするでしょう。こういった事態を未然に防ぐためには、生産スケジューラを導入して欠品をなくす努力をすることが重要です。生産スケジューラとは、日程計画や詳細なスケジュールを一つにしたデジタル方式です。生産スケジューラを導入することで、デジタルな在庫管理をすることが可能になり、スムーズな管理と欠品などのリスク回避につながります。生産スケジューラを導入して、欠品を最小限に抑えられるようにしましょう。生産スケジューラ導入によって具体的にどのような業務改善が実現したのかはこちらのページをご確認ください。

コラム編集部

最新記事 by コラム編集部 (全て見る)
- 納期管理:生産スケジューラの活用 - 2025年4月14日
- スケジューリング技術の応用による生産性の改善 - 2025年4月14日
- Lean Manufacturing~生産スケジューラの活用で最適な生産を - 2025年4月14日