生産計画を見える化するメリットとは?目的や具体的な方法を解説
2024.03.29A1:生産計画・スケジューリング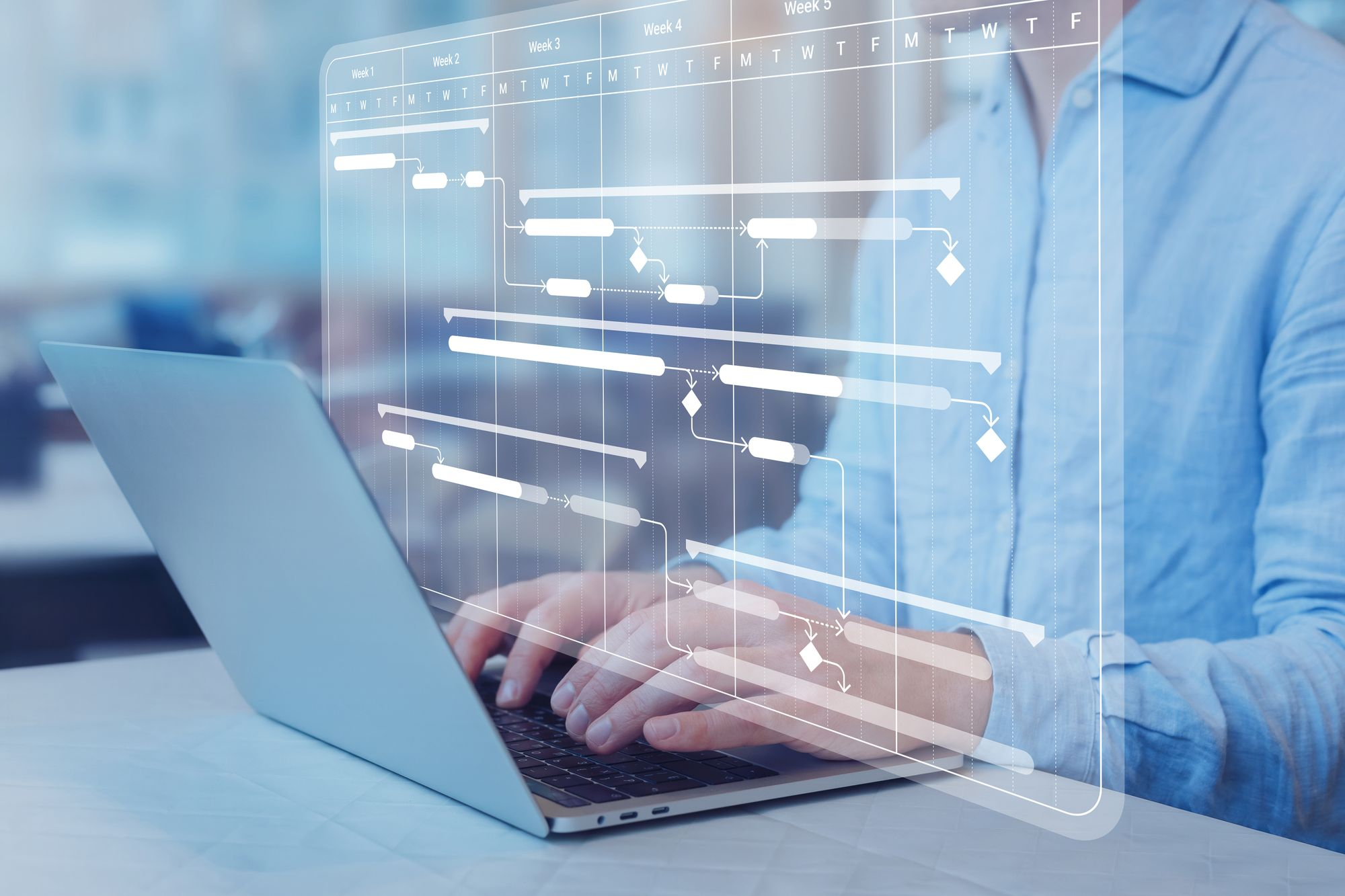
生産計画を目に見える状態にする「見える化」を行うことで、「そもそも計画通りに進んでいるのか把握できない」「生産性がなかなか上がらない」「突発的な作業に柔軟に対応できない」といった問題の解決につながります。この記事では、生産計画を見える化する目的やメリット、具体的な方法を解説します。
【目次】
■生産計画を見える化する目的
■生産計画を見える化することで得られるメリット
■生産計画を見える化する具体的な方法
■見える化の効果を成功事例から学ぶ
■まとめ
生産計画を見える化する目的
「見える化」とは、普段見えないデータを収集し、現状を目で見て確認できる状態にすることを言います。製造現場において見える化できるデータは、設備や機械の稼働状態、各案件の進捗状況などが挙げられます。見える化をしたうえで生産計画を立てることで、生産ラインや機械設備の設定変更が必要とされる段取りの回数や時間を減らすことが可能です。立てた生産計画まで見える化をすれば、自分たちの工程だけに集中しがちな製造現場も俯瞰して自工程を見ることができます。他にも見える化する目的として、以下の3つが挙げられます。
- 見える化によって課題改善の糸口を見つける
- 現場の競争力や生産力を上げる
- 製品の品質や安全性を保つ
見える化によって課題改善の糸口を見つける
見える化のためにデータを集める過程で、自社の抱える課題に気づき、その改善の糸口を見つけられます。様々なデータを集めて分析していくことで、自社における「ムリ」、「ムダ」、「ムラ」(3M)の原因に気づきやすくなるからです。こうして状況や原因を発見することで、「ムリ」、「ムダ」、「ムラ」を改善する策も考慮した上で生産計画を立てることが可能になるのです。
現場の競争力や生産力を上げる
生産計画を見える化するためには、リアルタイムに現場の状況を把握できるようにする必要があります。設備の稼働状況や進捗、在庫情報など、変化し続ける現場の状況を把握できていることで、何か問題や改善が求められる点が生じたときに、速やかに対処することができます。それにより、現場の競争力や生産力の向上につながります。
製品の品質や安全性を保つ
生産計画を見える化することで業務プロセスを自社内で共有することになるため、全員が同じ判断基準で行動できます。製品の品質、安全性といった点も、判断基準があることで共通の基準で判断でき、不良品の発生を防ぐことが可能になります。
生産計画を見える化することで得られるメリット
生産計画を見える化するためには、あらゆる部門や工程の情報を収集する必要があるため、手間と時間がかかります。しかし、生産計画を見える化することで、製品の製造におけるあらゆる面でメリットがあります。主なメリットとして挙げられるのは、以下の3つです。
- 生産の進捗を適切に管理できるようになる
- 業務の属人化防止につながる
- 設備保全計画も立てやすくなる
生産の進捗を適切に管理できるようになる
生産計画の過程では、計画を立案し直すために実績情報を反映します。遅延が発生していれば、その影響を踏まえた上で先の予定も調整する必要があるからです。生産計画を明確にし、それを基に進捗を追跡することで、迅速な情報共有と問題への対応が可能になります。これにより、作業者は状況を正確に把握し、業務の優先順位や順番を明確にすることで、作業をスムーズに行えるようになります。
業務の属人化防止につながる
属人化の原因は、業務のブラックボックス化です。とにかく納期に間に合わせることを優先していると、作業者の業務内容が定量化したマニュアルとして残りません。納期に間に合わせることのみを優先していると、短期的な目標である業務を回すことが最優先になります。担当者が業務を手早く行うことに注力するようになるため、長期的な視点で必要な業務のマニュアル化は後回しになってしまうのです。そうなると担当者しか業務内容を把握していない「ブラックボックス化」につながり、その人が不在の際、他の作業者が代わりに対応することができません。トラブルが発生した際なども、限られた作業者のみが業務内容を把握しているという状況だと、迅速かつ正しい対応をすることが難しいです。業務内容が不透明だと引継ぎも難しく、後任者に同じ業務を任せることも出来なくなります。また、業務内容を把握している人にだけ業務が偏り、特定の作業者にだけ負担が増してしまい心身の健康を損なうことも考えられます。
しかし、生産計画を見える化することで、業務内容を全作業者に共有することが可能になります。また、生産ライン全体の業務内容が透明化され、ブラックボックス化を防ぐことにもつながります。
設備保全計画も立てやすくなる
生産計画を見える化する過程では、機械の稼働状態や部品の使用状況、在庫状況を数値化します。これにより、機械の状態がすぐに把握でき、設備の保全計画を立てやすくなります。生産が遅延したり停止してしまったりする原因の1つに、設備に突然不具合が生じたり故障したりすることが挙げられます。生産計画の見える化で設備状況を把握しておくことで、こうした事態を未然に防ぐことにつながるのです。
生産計画を見える化する具体的な方法
生産計画を見える化する具体的な方法として、以下の3つが挙げられます。
- 業務内容を洗い出す
- 見える化させる情報の優先順位をつける
- 判断基準を明確に設定する
業務内容を洗い出す
業務内容を洗い出すことで、業務内容の全容が明らかになります。あらゆる業務を残らず丁寧に洗い出すことで、「ムリ」、「ムダ」、「ムラ」に気づくことができ、改善策を考えた上で生産計画を作成することができます。業務内容を洗い出すにあたって重要な要素は以下の4つになります。
- スケジュール管理:作業者の業務スケジュールを管理すること。業務実態を明らかにするために全員の業務スケジュールを把握する必要がある。
- タスクの進捗共有:現場で共有することで、タスクの実行状況が思わしくないときに迅速な対応が可能になる。
- 業務フローの構築:業務を完遂するための手順や流れを示したもの。業務のプロセスや役割分担がひと目で把握できる。
- ナレッジの共有:従業員に対するヒアリング等で集めた、業務を通して得られた知見を共有することで全体の生産性向上につながる。
こうした情報を収集するために、業務の責任者や担当者をはじめとする作業者にヒアリングを行います。また、ヒアリングに加えてアンケート調査や現場のモニタリングを行うと、より詳細な情報が集まるでしょう。
見える化させる情報の優先順位をつける
見える化は業務の全体像を掴むために必要なことですが、あまりにも見える化をし過ぎると情報過多になってしまいます。情報が多すぎると重要な情報がわからなくなり、的確な判断をすることができなくなります。
こうしたことを防ぐために、どの情報を見える化するか優先情報をつけることが必要です。見える化をする目的を考え、その目的を達成するために何の情報が必要なのかという点から優先順位をつけます。“目的達成のために行う見える化”であることを忘れないようにしましょう。
判断基準を明確に設定する
全作業者に生産計画を共有し、その計画通りに製品製造を進めるためには、共通の明確な判断基準を作ることが求められます。同じ情報を見たときに、判断基準がしっかりと定められ、かつ共有されていなければ、生産計画に沿って製造を進めることができません。例えば品質基準を明確に設定して自社内で周知することで、不良品の製品をすぐに見分けることが可能です。
業務の見える化を実現するツールの1つである生産スケジューラ。生産計画によって作業期間や必要なリソース、進捗度合いが変わってくるからこそ、精度を上げて計画を立てたいけれど時間を掛けてられない…とお悩みの方は、ぜひ「Asprova」の生産スケジューラをご検討ください。素早く最適な計画を可能にします。 Asprova概要 – 生産スケジューラ Asprova APS | アスプローバ株式会社
見える化の効果を成功事例から学ぶ
生産計画を見える化したことで、様々な効果が上がった成功事例が数多くあります。ここで紹介する会社の事例は2つです。どの会社もそれぞれの課題や問題点を抱えていましたが、共通するものとして以下が挙げられます。
- 生産計画の作成が手作業で時間がかかる
- 計算スピードが遅い
- 生産計画の変更ができない
こうした問題点があったため、納期遅れや多くの工数が必要な状況になっていました。しかし、生産スケジューラ「Asprova」を導入したことで、生産計画の作成が手早く行えるようになり、計画の変更にも柔軟に対応出来るようになりました。具体的にどのような課題や問題点を抱え、「Asprova」の導入でどのような効果が現れたのか、さらに詳しく会社ごとの事例を見ていきましょう。
株式会社日本エー・エム・シーの事例
株式会社日本エー・エム・シーでは、週に1度、1日がかりの手作業で生産計画の作成を行っており、作成にとても時間がかかっていました。作成後の計画は変更が難しく、状況の変化に対応した計画にならないことから、計画通りに生産が進まず、結果的に納期遅れを引き起こしていました。
そこで「Asprova」導入し、生産計画を見える化したことにより、現在の進捗がすぐにわかるようになりました。また、計画の変更も簡単にできるため、リクエストを反映した計画を作成できるようになりました。
「Asprova」にSolverオプションを取り入れたことで、さらに生産計画を作成する時間が解消され、生産リードタイムにおける段取り時間の短縮にもつながったという成果も上がっています。 株式会社日本エー・エム・シー 様
株式会社T&KTOKAの事例
株式会社T&KTOKAでは、手作業に近い状態で週単位の生産計画を作成していましたが、計算に時間がかかる上に計画の精度が悪いという悩みを抱えていました。そのため、急増する生産量に対応できず、原料などの在庫が不足して生産が追いつかない、納期に関する問い合わせに回答できないという状況に陥っていたのです。計算スピードが早い「Asprova」を導入したことで、これらの悩みが解消され、納期の事前把握が可能になりました。また、突発的な事態が起こっても生産計画の変更を速やかに行えるようになったことで柔軟な対応も可能になりました。
株式会社T&K TOKA 様
まとめ
生産スケジューラを導入することで、生産計画の作成にかかる時間が短縮され、変更も簡単に行えるようになります。
生産スケジューラは生産計画立案の効率化だけでなく、見える化にも役立ちます。生産計画が見える化することで、生産の進捗を適切に管理できるようになり、設備保全計画も立てやすくなります。また、生産ライン全体における業務内容の全容を把握することができるため、業務の属人化を防ぐことが可能です。
特定の作業者のみが業務内容を把握しているという状況だと、その従業員が何らかの理由で業務にあたれなくなったときに生産が滞ることになってしまいます。そうした事態を回避するためにも、生産スケジューラを導入して業務の属人化を防ぎましょう。

コラム編集部

最新記事 by コラム編集部 (全て見る)
- 納期管理~生産スケジュールの最適化による納期厳守率の向上 - 2025年4月14日
- スケジューリング技術の応用による生産性の改善 - 2025年4月14日
- Lean Manufacturing~生産スケジューラの活用で最適な生産を - 2025年4月14日