整流化の事例~スケジューラ導入により生産計画の固定率が40%から90%に向上!
2022.08.03A2:導入事例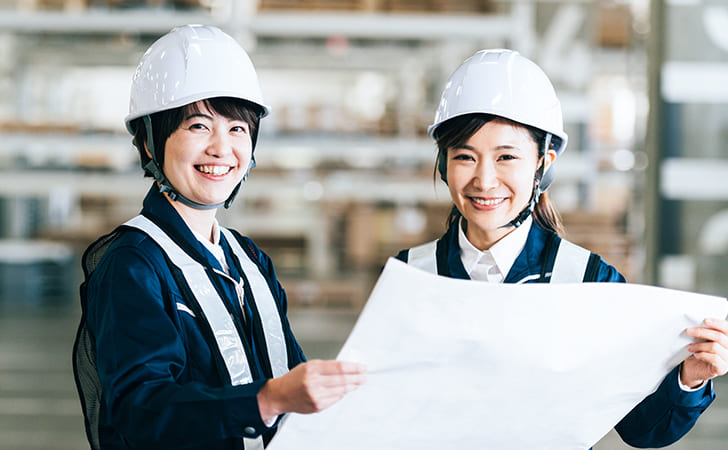
受注から納品までをスムーズに行うためには、生産の進捗状況や在庫量、設備の稼働状況、ボトルネック工程はどこか、などを把握(見える化)し生産工程を整流化する必要があります。
本記事では、生産スケジューラを利用した生産工程の整流化について、事例を用いてご紹介します。
生産工程を整流化するための課題
生産工程の整流化とは、リードタイムの短縮や生産性の向上につながります。
そのためには、どのような状態にしたいかといった「目的」と、各作業の「見える化」が重要となります。
つまり、目的を達成するためにネックとなっている箇所を発見し、解決することで生産工程を整流化することが可能になると言うことです。
たとえば、受注数量に対応する在庫量が無い場合、リードタイムが伸びてしまうため、スムーズな流れとは言えないでしょう。
また、稼働している設備と稼働していないものがある場合も、最大限に活用ができていないため、こちらもスムーズな生産工程であるとは言えません。
それらを解決し、生産工程を整流化するために、目的と見える化が重要となります。
生産スケジューラ導入で改善できたこと
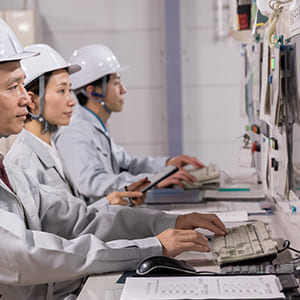
改善事例1:生産計画の固定率と、計画のリカバリ作業時間の削減
日本電産サーボ株式会社 様
https://www.asprova.jp/casestudies/nidec-servo.html
課題:個人のカンや経験に依存せず迅速に漏れのない計画立案
以前の生産活動において、情報の把握が困難なため生産達成率を遵守するための状況確認や関係者との調整などリカバリ作業に追われていました。納期短縮や納期変更の要請、部品が予定通り納品されない、部品納期の確認漏れなどの要因で、できるものから優先して組み立ててしまうというように生産計画に狂いが生じていました。
生産スケジューラ導入後の効果:生産計画の固定率、納期遵守率の向上
生産スケジューラを導入することで、ムリやムダ、漏れのない計画を自動で立案できるようになりました。スケジューラ導入以前の生産計画の固定率は40%程度でしたが、導入後は固定率が90% に高まっただけではなく、余剰在庫削減にも成功しました。
改善事例2:見える化によって在庫量や稼働状況を確認し再計画が可能に
株式会社東北TKR(現株式会社TKRマニュファクチャリングジャパン)様
https://www.asprova.jp/casestudies/tkr.html
課題:作業の見える化ができていないため、根本的な課題の解決ができない
作業の全体が見えていないため、下記のような課題を解決することができませんでした。
- 在庫最小化
- 不確実性への対処
- オーダの進捗状況の把握
- 納期の確定
- ボトルネックとなっている設備の特定
生産スケジューラ導入後の効果:さまざまな情報の可視化による生産工程の整流化が実現
部材の入庫から製品完成までの作業を流れとして一元管理することにより、生産工程の整流化が実現できるようになりました。
たとえば、外注先から支給された部品の増減を登録、部材支給予定や、納品指示に変化がある都度、再計画を実施することで、不足分をあらかじめ確認することができるようになったため、生産が止まる前に発注することができるようになりました。
生産スケジューラを使用して見える化と生産工程の整流化を行おう
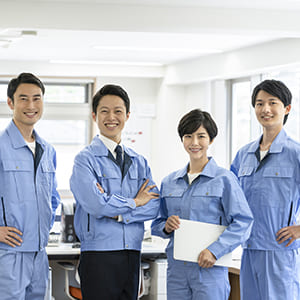
生産スケジューラに登録されたマスタ情報や実績をもとに生産計画を立案します。
人の経験則による整流化ではないため、ムリ・ムダのない生産計画の立案や納期遵守を達成することができます。
生産スケジューラを有効活用することで、手作業では確認が難しかった生産工程の全体像の把握や、問題となっていたボトルネックの改善といったことが可能となります。
おわりに
本記事では、生産工程の整流化についてご説明しました。
生産工程の整流化のためには、明確にどのような状態にしたいかといった「目的」と、各作業の「見える化」が重要となります。
整流化を行うべき課題には、下記のようなものが挙げられます。
- 過不足が無い、最適な在庫数の確保
- 不確実性への対処
- オーダの現状把握
- 納期の確定
- ボトルネックとなっている設備の特定
生産スケジューラを有効活用することで、全体像を把握することができるため、課題の解決や改善点を考慮した計画立案などを行うことができるようになります。

コラム編集部

最新記事 by コラム編集部 (全て見る)
- 困ったこと35~作業指示と無関係に作業する人がいて困った - 2025年4月23日
- 困ったこと35~一生懸命やっているのに、理解してもらえなかった - 2025年4月23日
- 困ったこと35~「何でもできる」と思い込んでいる人に困った - 2025年4月23日