生産スケジューラを導入すると、どんな効果が期待できますか?
2023.07.03A3:生産スケジューリングの悩み相談生産スケジューラを導入すると
1.製造リードタイムの短縮
2.納期遵守率の向上
3.在庫の削減・適正化
4.スループットの向上
5.属人化の解消
6.見える化・情報共有
などの効果が期待できます。以下、それぞれについて解説します。
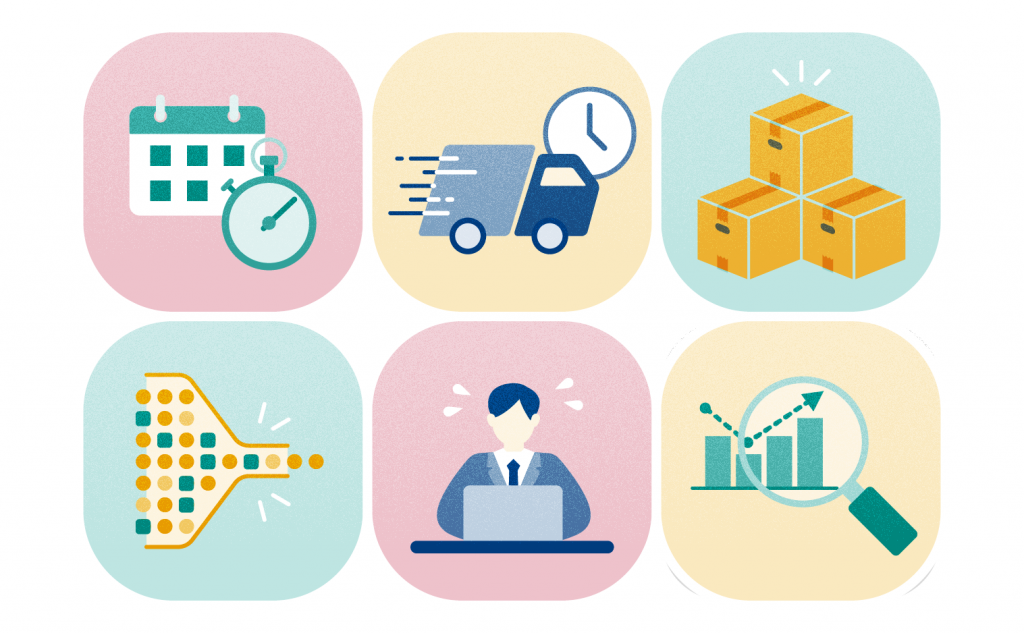
1.製造リードタイムの短縮
製造リードタイムが長くなると、以下の問題が発生します。
・在庫が増大します。例えば、製造リードタイムが2倍になると、仕掛在庫も2倍になります
・短納期要求に対応できず、その結果、受注を逸する可能性があります
・製造の着手が早くなるため、オーダ変更への対応力が低下します
製造リードタイムが長くなる原因は、①各工程の作業時間が長い、②工程間の待ち時間が長い、ことなどです。生産スケジューラがこれら、①②の原因をどのように解決するかを説明します。
①各工程の作業時間が長い
ERPシステムの中にあるMRP(Material Requirements Planning:資材所要量計画)の計算は、作業時間をおおざっぱにとらえ、日単位など長いタイムバケットで設定するために、作業時間(リードタイム)が長くなります。一方、生産スケジューラは秒単位で精密にスケジュールを計算するため各工程の作業時間が短くなり、全体のリードタイムが短縮されます。
②工程間の待ち時間が長い
生産スケジューラは、設備の能力を考慮したうえで、工程間の待ち時間が極力短くなるようにスケジュールしますので、工程間の待ち時間は短かくなります。
具体的には以下の事例記事をご覧ください。
リードタイム短縮の事例~多工程の生産スケジューリングで製造リードタイムが1/3に短縮!
2.納期遵守率の向上
納期遵守率が悪化すると、顧客満足度がさがり、売上げに悪影響をおよぼします。
納期遵守率が悪化する原因は、①正確な納期回答ができない、②資材(原材料)の有無を考慮できない、などです。生産スケジューラが、これら①②の原因をどのように解決するか説明します。
①正確な納期回答ができない
生産スケジューラは、設備の能力を考慮したうえで、秒単位の精密なスケジュールを計算します。よって、受注に対して製造がいつ完了するかが正確にわかります。これを高速に計算しますので、迅速で正確な納期回答が可能になります。
②資材の有無を考慮できない
生産スケジューラは、資材の有無を考慮したうえで、秒単位の精密なスケジュールを計算します。よって、資材の有無を考慮した生産スケジュールを作成します。
具体的には以下の事例記事をご覧ください。
納期遵守率向上の事例~生産スケジューラの導入により納期遅延率が1/3に激減!
生産スケジューラの導入事例として、ナブテスコ株式会社様と株式会社リコー様の事例が紹介されています。それぞれ、生産ラインの能力を考慮した計画の自動立案や、多品種少量生産に対応した生産計画の立案により、生産リードタイムの短縮や納期遅延率の低減が実現されたと報告されています。
3.在庫の削減・適正化
過剰在庫になると、以下の問題が発生します。
・在庫資産が増え、会社のキャッシュフローが悪化します
・在庫保管費用が増え、会社の利益が圧迫されます
・売れない在庫は死蔵品となり価値がゼロになります。廃棄費用がかかると価値はマイナスになります
過剰在庫になる原因は、①製造リードタイムが長い、②製造の完了が早すぎる、③資材(原材料)の購入が早すぎる、などがあります。生産スケジューラが、これらの原因をどのように解決するかを説明します
①製造リードタイムが長い
生産スケジューラを導入すると製造リードタイムが短くなり、結果、在庫低減効果があることは前述のとおりです。
②製造の完了が早すぎる
納期より製造の完了が早すぎると、製品在庫の山ができてしまいます。生産スケジューラを用いて納期からバックワードにスケジュールすると、納期に近くで完了するジャストインタイムなスケジュールができます。その結果、製品在庫の山は激減します。
③資材の購入が早すぎる
資材の購入が早すぎると、資材の在庫の山ができてしまいます。生産スケジューラで、バックワードにスケジュールすると、資材の必要なタイミングが精密にわかります。結果、資材の購入が早すぎて、資材が在庫の山になることを防ぎます。
生産スケジューラを導入した事例として、少量多品種のオーダに対応できていなかった日本電産サーボ株式会社様と、担当者の手作業による管理であった株式会社T&K TOKA様が挙げられます。導入後には、在庫不足を防ぎ、余剰在庫の削減が実現でき、生産計画の立案時間を削減し、素早い計算と柔軟な生産計画の変更対応が可能となりました。
具体的には以下の事例記事をご覧ください。
在庫削減の事例~生産スケジューラ導入で在庫削減80%達成!
4.スループットの向上
スループット(単位期間あたりの生産量、または、生産額)が大きいほど、需要が大きい時、売上は向上します。
スループットが低下する原因は、①正しい生産スケジュールが立てられないために生産が非効率、②ボトルネック設備を最大限活用できていない、などです。生産スケジューラが、これらの原因をどのように解決するかを説明します。
①正しい生産スケジュールが立てられないために生産が非効率
多くの企業では生産スケジュールを人間が作成しています。しかし、生産スケジュールの作成は、設備の能力、原材料の有無、在庫、納期、段取り時間など多くの制約を同時に考慮する必要があり、精密なスケジュールを人間が立案するのは、データ量が多くなるにしたがって困難になります。よって、スループットを最大化するスケジュールを立てるのは容易ではありません。生産スケジューラは上記の制約を考慮した、効率の良いスケジュールを作成します。その結果、スループットは向上します。
②ボトルネック設備を最大限活用できていない
スループットを向上するには個別最適ではなく、全体最適をする必要があります。そのためには、ボトルネック設備の生産効率を最大化する必要があります。生産スケジューラを用いると、ボトルネック設備の生産効率を最大化して、前後工程を従属させる、いわゆるTOC(Theory of Constraint)の考え方を取り入れたスケジューリングが可能です。
具体的には以下の事例記事をご覧ください。生産能力の最大限の活用や生産リードタイム短縮、在庫削減などを実現した中国の順徳蜆華多媒体製品有限公司様や泰豐輪胎株式会社様の導入事例が紹介されています。
スループット向上の事例~ボトルネック中心の有限能力スケジューリングにより全体最適を実現!
5.属人化の解消
生産スケジュールを人間が作成している場合、生産計画担当者の頭の中に膨大なノウハウがたまり、属人化してしまいます。年月がたち生産計画担当者が高齢化し退職することを想定すると、次の世代にその膨大なノウハウを伝授する必要がありますが、それは容易なことではありません。
生産スケジューラを導入すると、生産計画業務の属人化を解消し、高精度で標準化された生産計画の立案が可能です。
改善事例として、アリアケジャパン株式会社様では、生産計画を立案するために必要だったベテラン社員の経験に頼ることがなくなり、ミスなく計画立案ができるようになりました。また、生産スケジューラを利用することで、手作業での計画立案に必要な時間が削減され、社員は本来の業務に専念できるようになります。生産スケジューラは、誰でも高精度な計画を手作業よりも早く立案できるため、生産計画立案にかかる労働時間の削減も可能です。
具体的には以下の事例記事をご覧ください。
脱属人化の事例~経験や勘頼みから脱却した生産スケジューリングを実現!
6.見える化・情報共有
製造業では、IoT, DX, AI化などが求められています。生産スケジューラの導入により、生産工程とさまざまな条件をマスター化し、高速な計画変更が可能となり、計画結果をグラフィカルに表示して見える化を実現します。その結果、必要な量の材料調達や納期遵守を実現することができ、スタッフがさまざまな視点を持つことができたため、納期遵守と顧客からの信頼を獲得することができます。
具体的には以下の事例記事をご覧ください。
見える化の事例~生産スケジューラ導入により生産量を過去の実績換算で16%アップ!
(了)

コラム編集部

最新記事 by コラム編集部 (全て見る)
- MRPの真価を引き出す!生産計画・在庫管理・スケジューラ連携 - 2025年4月22日
- 工程管理:生産スケジューラと連携して納期遅れを防止 - 2025年4月22日
- 段取り時間削減:AI生産スケジューラの活用 - 2025年4月22日