製造業における「サイクルタイム・タクトタイム・リードタイム」とは?業務効率化のキーポイント!
2020.11.30A0 生産管理
製造業の現場において重要なワード、「サイクルタイム」「タクトタイム」「リードタイム」の意味をうまく説明できますか?
それぞれ意味が混同されやすい用語ですが、製造業の管理を担う上では、意味をきちんと理解して、使い分けられるようになっておいたほうが良いでしょう。「サイクルタイム」「タクトタイム」「リードタイム」の意味を正しく理解できれば、工場の生産能力が把握しやすくなり、余剰在庫や欠品を防ぎやすくなります。「サイクルタイムやタクトタイム、リードタイムの違いを知りたい」「○○タイムを短くしたい」という方に向け、製造業における○○タイムの基本情報、理想的な指標のあり方、タイムの調整方法などを掘り下げて解説します。
【目次】
■サイクルタイムとは
■タクトタイムとは
■リードタイムとは
■タイムは短ければ短いほど良いの?
■生産が追い付かない!サイクルタイムを短くしたい!
■収益性をアップさせたい!リードタイムを短くする方法
■「製造の安定化」と「収益の最大化」は永遠の課題
■言葉の意味を正しく理解しよう
サイクルタイム・タクトタイム・リードタイムの違い | |||
---|---|---|---|
サイクルタイム | タクトタイム | リードタイム | |
概要 | 1つの製品が作られるまで 実際にかかった時間 |
1つの製品製造にかけられる時間 | 製品の生産を開始してから 完成するまでの総時間 |
計算式 | 稼働時間÷実生産数 | 稼働時間÷必要生産数 | ー |
別名 | ・CT ・Cycle Time |
・TT ・Takt Time |
・LT ・Lead Time |
「サイクルタイム」「タクトタイム」「リードタイム」の概要、計算式は上記のとおりです。当コラムでは個別に詳しく解説しますが、まずはおおまかな違いを把握しておきましょう。ですが、中には「このくらいの基本情報はすでに知っているよ」という方もいるかもしれません。「サイクルタイムやリードタイムの短縮を目指したい」という方は、当コラムの前に以下のページをご参照ください。サイクルタイム・リードタイムの計算に役立つ「生産スケジューラ」について、わかりやすく解説しています。少しでもご興味のある方は、まずはこちらをご覧ください。
サイクルタイムとは
1日1,500個の製品を生産できる工場のサイクルタイム例 | |
---|---|
一日の工場稼働時間 | 390分(6時間30分) |
1日における実際の生産数 | 1,500個 |
サイクルタイムの計算式 | 390÷1,500(稼働時間÷実際の生産数) |
サイクルタイム | 15.6秒 |
サイクルタイムとは、「製品を1つあたりどれくらいの時間で作ることができるのか」という1作業サイクルあたりの時間です。例えば、1日の稼働時間が6時間30分の工場で、1日1,500個の製品を製造した場合、サイクルタイムは上記のとおり15.6秒と算出できます。つまり、この工場では「1個の製品を作るのに15.6秒かかっている」といいかえられます。このサイクルタイムは後述するタクトタイムと混同されやすいため、使い分けには注意が必要です。
タクトタイムとは
月50,000個の製品の納品をする際のタクトタイム例 | |
---|---|
月50,000個(必要となる生産数)÷月間25日(工場の稼働日)=2,000個(1日に必要な生産数) | |
1日の工場稼働時間 | 390分(6時間30分) |
1日に必要な生産数 | 2,000個 |
タクトタイムの計算式 | 390÷2,000(稼働時間÷必要生産数) |
タクトタイム | 11.7秒 |
タクトタイムとは、「生産工程における均等なタイミングを計るための工程作業時間のこと」です。わかりやすくいえば、「1個の製品を作るのに指標となる時間」となります。このタクトタイムのタクトは、指揮者の指揮棒のことを指していて、指揮者がタクトで指示をするように全体のタイミングを計るということに由来しています。仮に、月に50,000個の製品の納品をしなければならない場合、週あたりや1日あたりにどれだけの個数の製品を生産する必要があるのかが自ずとわかるでしょう。
例えば、月間25日稼働1シフト体制の工場があったとして、その工場では日に2,000個生産することで、お客様の求めている数の製品を納入できます。この工場での1日の勤務時間が8時間、昼休憩が1時間、休憩が30分だとした場合、本当にこの工場が稼働できる時間は、6時間30分(390分)です。390(分)÷2,000(個)の計算をすると、その結果は、11.7秒/1個ということになります。
つまり、お客様の求めている数を納品するには、「1個の製品を11.7秒で作るのが理想」といいかえられます。
サイクルタイムはタクトタイムとでは、意味や計算の方法が異なります。計算式にすると、サイクルタイムは、稼働時間を生産する製品の個数で割ったものです。一方、タクトタイムは、稼働時間を顧客や市場の必要数で割ったものです。意味の違いとしては、サイクルタイムは生産を中心に考えたもので、タクトタイムは顧客の注文や市場のニーズを中心に考えたものです。
もう少し噛み砕いていえば、「タクトタイムは理論値、サイクルタイムは実測値」という認識でも良いでしょう。
リードタイムとは
ある製品の生産を開始してから、完成するまでの時間の合計。これが、リードタイムです。発注から納品に至るまでの時間すべてのことを指すため、待ち時間や資材が到着するまでの時間など、実にさまざまな要素で構成されています。要素ごとに、「生産リードタイム」、「調達リードタイム」、「納品リードタイム」など、その種類は多岐に渡ります。
○○タイムは短ければ短いほど良いの?
サイクルタイム・タクトタイム・リードタイムの関係性として、「どのような状態が望ましいか」を解説します。
どんな状態 | |
サイクルタイム=タクトタイム | 必要な個数を必要なだけ生産できている状態。 |
サイクルタイム>タクトタイム | 需要に対して生産が追い付いていない状態で、欠品や納期遅延などを招きやすい。 |
サイクルタイム<タクトタイム | 製品を目標よりも多く生産している状態で、余剰在庫を抱えがち。 |
リードタイムが長い | 注文に対して回転率が低く、収益率や顧客満足度が低下しやすい状態。 |
リードタイムが短い | 注文に対して回転率が高く、収益率や顧客満足度が向上しやすい状態。 |
結論からいえば、サイクルタイムとタクトタイムは近い数値の状態が理想的です。
サイクルタイムとタクトタイムの数値が近い状態は、「必要な量を必要な分だけ製造できている状態」といいかえられます。一方、どちらかに偏っている状態だと、欠品や余剰在庫が出る可能性も高くなります。一見すると、タクトタイムに対してサイクルタイムが短いと、「製品を十分に生産できている」という印象を抱きがちです。しかし、製造業において作り過ぎは在庫を抱えることになり、発生した保管費でコストを圧迫します。以上の点から、サイクルタイムとタクトタイムは数値を近づけることを目指しましょう。
一方、「リードタイム」(生産を開始してから完成するまでの時間)は、短いほうが理想です。リードタイムが短いと、注文に対して回転率が高くなり、収益率や顧客満足度がアップしやすくなります。わかりやすくいえば、リードタイムが短い状態は「顧客の要望に素早く対応できている状態」なので、時間が長くなることにあまりメリットはないのです。
なお、製造業において悩みのタネになりやすいのは、「生産が追い付かない!」「欠品が多い」というケースです。そのため、製造業の管理を担う方の中には、「いかにサイクルタイム・リードタイムを短くするか」という点に悩む方が大勢います。そこでサイクルタイム・リードタイムを短縮させて、適切な製造をする方法を伝授します。
生産が追い付かない!サイクルタイムを短くしたい!
サイクルタイムを短くするためには、無駄な時間であるロスタイムを減少させることが効果的です。

例えば、上記のような製造工程があった場合、グレーの部分がロスタイムとなります。加工(工程②)に時間がかかってしまっている分、それ以外の工程にロスタイムが発生している状態です。この状態だと、どんなに早く材料の搬入(工程①)を行っても、加工のできない材料がどんどん溜まっていくだけで意味がありません。生産効率がアップすれば、生産工程におけるムダが減少し、サイクルタイムとタクトタイムの数値に近づきやすくなります。
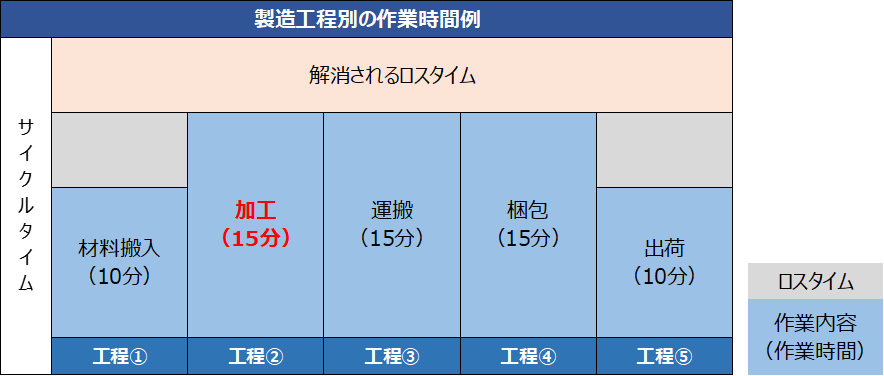
上記のように、工程②の作業時間が減少するだけで、工程別で発生するロスタイムも少なくなります。工程の作業時間を解消する方法はさまざまですが、ボトルネックとなっている作業量の調整や、作業スペースの見直しなどが有効です。この他、作業者を増員させて処理のスピードを向上させるのも良い方法といえるでしょう。
ちなみに、製造業では「作業時間が余る」「ラインがヒマを持て余す」というケースもありますが、こちらは単純に「契約数を増やす」「現場の稼働時間を減らす」「配置転換を行う」などを行うことで解消が可能です。
収益性をアップさせたい!リードタイムを短くする方法
リードタイムは、要素別に短縮方法が変化します。おおまかな短縮方法は、以下のとおりです。
- 開発リードタイム:部品や仕様を共通化する
- 生産リードタイム:生産計画の見直し、各作業員の業務のスリム化、人員の配置転換などを行う
- 調達リードタイム:社内の調達計画の見直しを行う
- 配達リードタイム:人員の増加、倉庫内の整理方法や配達手段の見直しを行う
リードタイムの短縮を目指す場合、要素に合わせて自社に合った手法を選びましょう。なお、材料の調達を自社ではなく取引先からしている場合は、発注計画書の提出を求めて計画の見直しを行うことで、調達リードタイムの短縮が可能となります。リードタイムを見直すことは、市場への対応力が向上する他、滞留在庫の削減や生産性の向上などの享受にもつながるでしょう。
「製造の安定化」と「収益の最大化」は永遠の課題
製造業の管理者にとって、「製造の安定化」と「収益の最大化」は常につきまとう問題です。
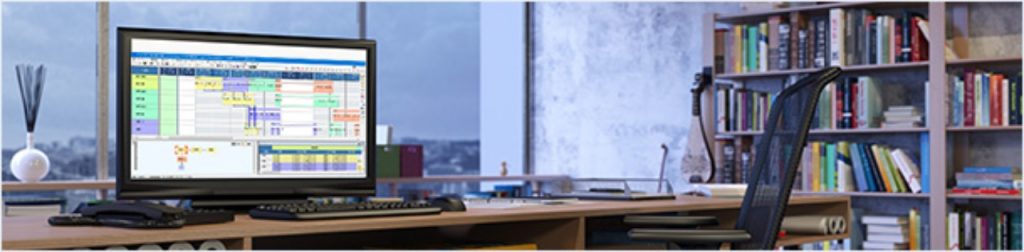
これらの問題解決に取り組む方に向けて、生産スケジューラ「Asprova」の導入をおすすめします。ここでいう生産スケジューラは、いわば「生産スケジューリングのための専用計算ツール」です。Asprovaの基本機能である「有限能力スケジューリング」を使えば、資源(設備や人員)のキャパシティを超えないように作業配置ができます。つまり、必要な個数に対して必要なだけ生産ができる(サイクルタイムとタクトタイムの数値を近づられる)体制を作りやすくなるのです。
また、Asprovaを使えば、製造工程におけるボトルネックなどの問題点を可視化できます。問題点を見つけ対策を打つことで、前述のリードタイムの短縮も夢ではありません。この他、スケジュールの変更や共有はもちろん、表示は時間単位から数ヶ月単位まで切り替えも可能なので、当日のスケジュールから長期に渡るスケジュールの確認も簡単です。サイクルタイムやリードタイムの短縮を目指す管理者の方に向け、Asprovaの機能や詳しい導入方法・導入実績は以下のページで紹介しています。少しでもご興味のある方は、まずはこちらをご覧ください。
言葉の意味を正しく理解しよう
業務効率化の重要なポイントとなる、「サイクルタイム・タクトタイム・リードタイム」を紹介しました。それぞれの意味を正しく理解し、業務効率化を目指しましょう。ですが、製造工程のどこに問題があるかを、目視だけで判断するのは困難です。製造業における業務効率化を実現するなら、生産スケジューラの導入を検討してください。生産スケジューラを利用すれば、サイクルタイム・タクトタイムを計算して、「製造工程のどこにボトルネックが」が判明しやすくなります。
急な差し込み案件の対応や迅速な計画変更など、生産管理に課題を感じている方は、生産スケジューラの導入を検討してみてはいかがでしょうか。なお、当コラムで紹介した生産スケジューラ「Asprova」は、「お試しで使ってみたい」という方に向けて無料体験版をご提供しています。この他、Asprovaの資料請求なども承っているので、詳しくは以下のお問い合わせページからお申し込みください。