トーテック・松野隼弥さんが語る、生産スケジューリングの最適化Solverにおけるアジャイル開発とPoCの有効性
2022.07.07S0: Solverオプション(最適化) , X2:販売パートナーインタビュービジネスパートナー会 松野隼弥さんに聞く
アスプローバ社のパートナーであり、新たなオプション機能「Solver」導入の先駆けともなっているトーテックアメニティ株式会社の松野隼弥(まつの・たかや)さんに生産スケジューラーの現状と将来像をうかがいました。Solverによって、人間が考えたような結果に近いものが示されることができるようになりました。今後の生産管理は、AIのような新たな要素を取り入れながら、標準化、全体最適化をめざすのでは、ということでした。
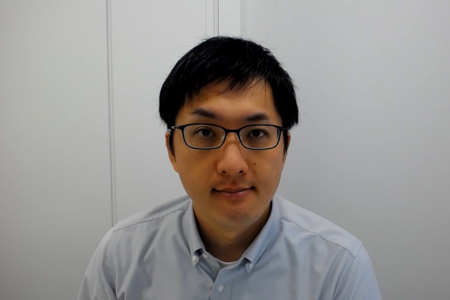
あらゆる製造業が対象
- まず御社とご自身のことについて教えてください
トーテックは、製造業を対象にITソリューションを提供しています。本社は製造業の盛んな名古屋にあり、営業エリアは全国です。私が所属する産業システム事業部のシステムエンジニアは、名古屋と大阪に集約されています。
私は37歳。新卒入社から15年になります。入社後8年間はプログラマーでした。2015年に転機があり、アスプローバ社からAPT(注・Asprova Practical Training seminar)という資格認定を受け、導入のエンジニアに仲間入りをしました。2018年にはシニアAPT認定を受け、以降はプロジェクトリーダーの立場で、生産スケジューラー「Asprova」の導入をしています。今まで10社以上のユーザ様に対して、Asprovaを導入してきました。
- 生産管理システムの事業は、御社内でどのような位置づけになっていますか
中心といってもいいでしょう。Asprova導入をきっかけに、データを可視化するBIツール、実績収集、品質管理など、多様な製品やサービスの導入支援を、部内のさまざまな担当者が連携して行っています。会社としては、10年以上前(2012年頃)からAsprovaを扱っています。対象業種は自動車部品、機械、鉄鋼、化学、電気、印刷などです。プリント基盤のように多品種少量生産のものや、長期間かけて大きな1点ものを作り上げる工作機械など、きわめて多岐にわたります。
人が考えた計画に近づく
- これまでのスケジューラーで不足していた点、実際の現場で使えないな、とされていたのはどんなところでしょう。今回のSolverで改善されたのはどんなところでしょう
今までのスケジューラーでは、あらかじめ決められた優先度通りに計画し、人が修正するといった形でした。ただしその優先度も、オーダの状況、設備の稼働状況、段取り効率など様々な要因で日々刻々と変わります。状況によって最適解は変わってくるはずです。
Solverでは“反復改善、複数結果からより良い計画を選択するといった人が考えて作る計画に近づいてきた”と感じています。そこが今までのスケジューラーでは不足していたところです。お客様からもそうした反応をいただいています。
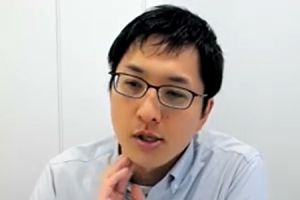
- 足りない点はありますか
お客様の抱える課題は数多く、Solverという手段が増えても、すべてご満足いただくには、まだまだ道のりが長いですね。一つ一つの工程の処理に関しては優れた解が導き出せるのですが、複数の工程にまたがり、全体の最適化を導くには、さらなる進歩が必要だと思います。
Solverは発展途上の機能ですので、早く効果が出せる部分からトライしていくのがいいと思います。
- Solverは、アジャイル開発といって、打ち合わせ、試作、検証を短い期間で繰り返すPoC(Proof of Concept)の仕組みをとっています。これに関してはどうお考えですか
かつては、初めからがっちり仕様を決めておく方式が主流でしたが、ここ数年、小さなサイクルで改修を繰り返すアジャイル型のシステム導入が増え始めていると感じています。文章でみるよりも、実際にアジャイルで出力されたものをみる方が、良し悪しを判断しやすいでしょう。
まずは、PoCの進め方をお客様にご理解いただくことです。solverの機能は少しずつリリース、拡張されていくので、ある程度長期化することを見込んでおかなくてはなりません。緊急性の高い場合、solverに頼らず、標準機能でできる範囲で対応していくことです。
- Solver導入に、向き不向きがあると思いますか。有望な業種や工程はありますか。
向いているのは、ネックの工程がはっきりしており、そこの製造効率を上げれば工場全体のトータルリードタイムが短縮できるようなお客様です。ネック工程をSolverで計画し、前後工程は自動追従するだけといった形が理想的です。あるユーザ様では、段取り効率、オーダの仕様と資源の製造可否などが複雑で、特定の工程だけをSolverで計画しています。
ニーズがシステムを進化させる
- 生産管理のシステムはどういう方向に進むのでしょうか。
生産現場のニーズによって、システムは進化していきます。システムを導入し、標準化を進めていても、どうしても、日々の変動に耐え切れずマニュアル調整は起こります。Solverのようなソフトが発展し、マニュアル調整の負荷がなくなり、真の業務標準化になっていくと思います。
日々カイゼンが求められる生産管理のシステムにおいて、新たな思考、仕組みを検討・導入するニーズは必ずあります。AI的な方向もその一つです。手軽に試せる環境が整うと、さらに導入が進みやすくなるでしょう。
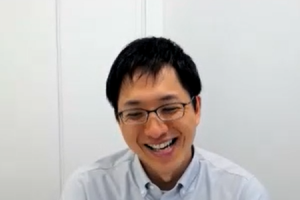
- 将来の抱負をお聞かせください。
今回Solver導入への貢献が認められ、5月19日にアスプローバ社より「Solver Movement Award 2021」を受賞致しました。今後も、Solverの効果を体験していただき、お客様、アスプローバ社、そして弊社の3社でwin-win-winの関係を構築していきたいと思っています。
(了)
本記事の販売パートナーに相談してみる(トーテックアメニティ株式会社)

コラム編集部

最新記事 by コラム編集部 (全て見る)
- 困ったこと35~作業指示と無関係に作業する人がいて困った - 2025年4月23日
- 困ったこと35~一生懸命やっているのに、理解してもらえなかった - 2025年4月23日
- 困ったこと35~「何でもできる」と思い込んでいる人に困った - 2025年4月23日