納期を守りながら段取り時間を減らす~最適化AI 、S3
2025.02.12S03:納期遅れと段取りを同時に最小化したい工場の生産スケジューリングは、従来のルールベースから大きく変化し、AIを用いる時代になりました。スケジューラのトップ企業であるアスプローバ社は、「最適化AI」を利用したSolverシリーズを次々に世に送り出しています。数あるSolverの中のベストセラーが、今回紹介する「S3」です。生産設備を取り換える「段取り」の時間を短縮しながら、納期を守ることができる計画を立ててくれます。
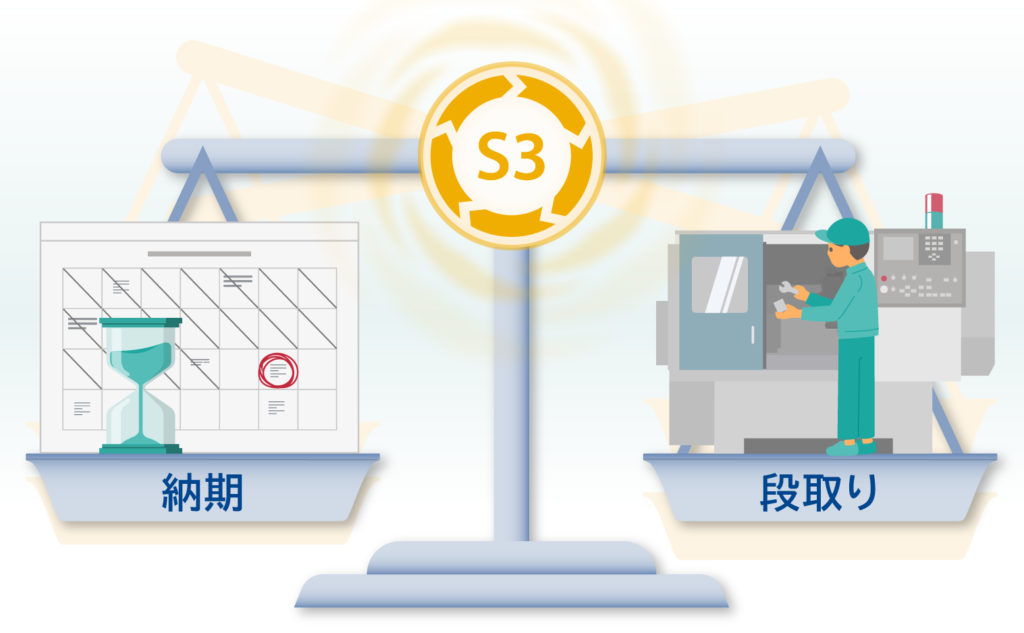
バランスをとる
段取りとは、さまざまな品種を同じラインで生産するために、金型を切り替えたり、機械の設定を変えたりすることです。段取りの時間が増えると、製造していない時間が増え、効率が下がります。プログラムや治工具の再調整や清掃などに時間と人手がかかるからです。長い場合には1回の段取りに20時間以上かかるケースもあります。生産計画においては、段取り時間を最小化することで、設備停止などによる機会損失をなくし、単位時間あたりの生産量を最大化することをめざします。
ここで問題になるのは、段取りが少ないほどいいとは、必ずしもいえないことです。同じものをまとめて作ると段取りは削減できます。たとえば、黒、赤、青の3種類のボールペンを作っているような工場があったとします。一年分の注文を色ごとにまとめて黒→赤→青という順番に作れば、段取り時間は最小化されます。しかし、青ボールペンが作り始められるのは半年以上先となってしまいます。これではお客さまの需要にこたえることができません。同じものを作り続けると、変化する需要にこたえられず、納期遅れにつながるのです。したがって、納期と段取りのバランスが重要になります。
従来の計画では、納期を重視し、余裕を見ながら品目まとめを行うように設定するのが普通です。しかし、そのルール化やパラメータの設定が難しく、手作業に頼る部分が大きかったのです。アスプローバ社では、最適化AIの手法を用いてこの課題の解決に挑みました。「最適化AI」は、特定の目標に向かって複数の変数を調整し、制約条件の中で、最も効率的な解決策を見つけます。膨大な組み合わせの中から、最もよい生産の順番を探索し、示してくれるのです。
豊富な実績
現在、単に納期と段取りを最適化するものであれば、他社からも作られているようですが、アスプローバのSolverは、生産スケジューリングや段取り最小化に特化することで、それを超える速度と精度を出せるよう、さまざまな工夫をしています。
実例をご覧ください。自動車部品製造のアイコクアルファ株式会社では、「以前は6時間かかっていたレース(旋削)工程の生産計画が、Solverのおかげで、2時間で立てられるようになりました。時間をかけて手作業で立てていた計画も今ではボタン1つです。ほとんど修正もありません」と話しています。
コニカミノルタメカトロニクス株式会社では、デジタル商業印刷機の高精度部品を多品種少量生産しています。社内で最適化技術を開発しており、アスプローバ社と考え方が一致して、Solverを共同開発しました。その結果、板金加工の工程で「生産計画作成を90~95%自動化でき、計画の最適化により段取り時間を22%削減できました」との結果を得ています。
アスプローバ社では現在、この段取り最小化を、複数の工程で一気通貫で行うチャレンジもしています。顧客から案件を示され取り組み中ですが、難易度が高く、アスプローバ社の技術を結集しないと実現が難しい問題です。それでもすでに「1回の計画立案に20時間かかっていたところ、前処理や微調整など含めて5時間程度で、今まで人が立てていた計画とほぼ同等のことができるようになった」との声が出ているそうです。
段取り効率化と納期順守の問題は、全国どこの生産現場でも起きています。アスプローバ社は、さらに顧客の要望を聞きながら、Solverを進歩させていきたいと考えています。
(了)

コラム編集部

最新記事 by コラム編集部 (全て見る)
- 納期管理:生産スケジューラの活用 - 2025年4月14日
- スケジューリング技術の応用による生産性の改善 - 2025年4月14日
- Lean Manufacturing~生産スケジューラの活用で最適な生産を - 2025年4月14日