ループコンベアの投入順序最適化~Solverでハンガー交換回数を激減~吉川英二
2022.09.07S05:ループコンベアの投入順序を最適化したい , X1:アスプローバ社員インタビューアスプローバ社 コンサルタントに聞く⑤ 吉川英二
アスプローバのコンサルタント吉川英二(よしかわ・えいじ)さんに、Asprovaのオプション機能「Solver」で、ループ型のコンベアで生産の効率化を図る方法を聞きました。「塗装ラインの周回数とハンガー取替を最小化したい~S5」です。ループコンベアは特殊な生産ラインで、代表的なのが塗装工程です。対象物をぶらさげるハンガーの取り替えが大事なポイントになっています。
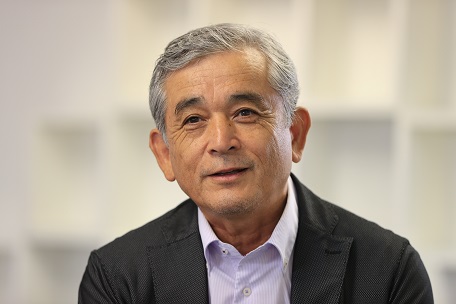
ハンガーが問題だ
- ループコンベアの特色はどんなところにありますか。
ループコンベアが使われているのは、主に塗装工程です。定速で移動するフックにハンガーを掛けて、そのハンガーに塗装対象品目を吊るして塗装します。塗装工程の課題はいろいろあります。まず製造時間が長いことです。取り付けから始まり、1周して取り外しまで、たいてい周回時間は2,3時間かかります。
そしてフックの数ほどハンガーの数はないので、塗装する製造ロット数量が、利用するハンガーの数より多いと、数周に分割して塗装する必要があります。同一製造ロットの製造時間は、分割数×周回時間になります。そしてハンガー取替作業は、ハンガーが重いので作業者に負担を掛けます。多品種や多色の塗装を求められる場合、ハンガーは頻繁に交換しなくてはなりません。色替えやレシピ替えが増えると、混色防止や作業準備のため、フックに塗装対象品目を吊れない期間が多くなります。それによって周回数も増えるので、生産性が低下します。
また塗装工程は周回ごとにロット分割することが多いので、その前後工程と同期して生産するのが難しく、仕掛在庫が多くなり、保管場所がなくなる問題も発生します。
- ハンガーが重要なのですね。
ハンガーの数十分あれば、既存の生産スケジューラで計画できます。しかしたいていの場合はハンガーが制約条件になります。ハンガーの数が少なすぎると周回数が多くなり生産効率がおちます。またハンガーをつるす順番が適正でないと、ハンガーの取替頻度が増えて、作業者の負担が増加します。
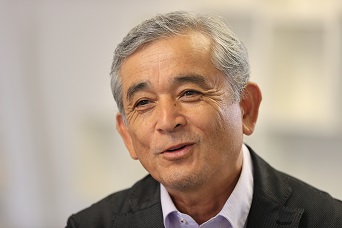
セミナーでは、塗装工程の制約事項を12項目あげています。先に述べたように、ラインの周回数を最小化したい、ハンガーの取替回数を最小化したい、色替えやレシピ替え回数を最小化したいなどです。それに加えて、レシピ替えに必要な空きフックをどう設定するか、一つのハンガーに複数の品目をつる、休憩時間を考慮して吊らない期間を設定するといった事項もあります。
これだけ制約が多いと、標準機能では需要変動に柔軟に対応できません。Solverオプションであれば、需要が変動しても最適な計画を立案することができるのです。
取り替え回数を3分の1に
- 実例をあげてください。
セミナーS5でとりあげた例では、Solverオプションで計画すると、ハンガー取替数が従前の772回から244回に減少しました。また周回数は7.12周から5.69周に減少しました。このように、ハンガー取替数や周回数の総和が少なるような投入順を反復改善して最適な計画を短時間で立案できます。
Solverは、顧客ごとの専用プログラムになります。取り替え回数を重視するか、周回数を重視するか、両方のバランスが大事なのか、要望に応じて変えられます。
- 塗装の他にも使えそうなラインはありますか。
工業生産品目で複数品種で複数色を塗装する工場での利用を想定しています。自動車部品、オフィス家具や電気製品など様々な製品に適用できます。さらにメッキやゴムベルトなど、いろいろな適用候補があります。ループコンベアは、生産工程の中ではニッチな存在です。それでも国内に数千カ所はあるとみています。S3の「納期と段取りの両立」に比べたら少ないかもしれませんが、S5がうまくはまる現場は、これから次々に出てくると考えています。
- ループコンベアの詳細情報はナレッジセンターにてご覧いただけます。(会員登録が必要です)

コラム編集部

最新記事 by コラム編集部 (全て見る)
- MRPの真価を引き出す!生産計画・在庫管理・スケジューラ連携 - 2025年4月22日
- 工程管理:生産スケジューラと連携して納期遅れを防止 - 2025年4月22日
- 段取り時間削減:AI生産スケジューラの活用 - 2025年4月22日