16%の生産増と43%の工数減を果たす
2023.11.19X0:ユーザーインタビュー2023年11月2日、東京駅前のミッドタウン八重洲で開催された「Asprovaユーザ会2023」で、アリアケジャパンと日本エー・エム・シーの2社が事例講演を行いました。アリアケジャパンで導入を担当した濱田剛さん(生産管理課 課長)のお話を、要約してお伝えします。
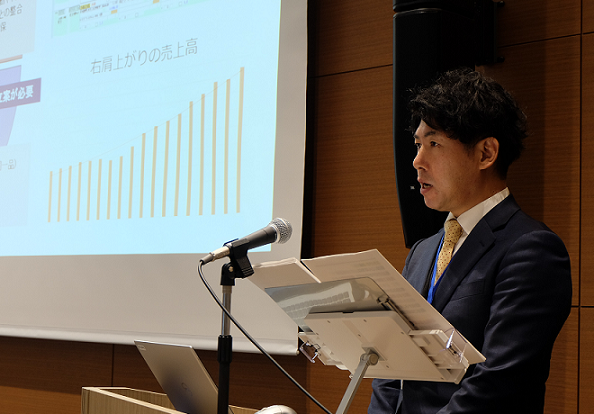
売上高は右肩上がりも生産計画は…
アリアケジャパンは、長崎県に主力工場を置く畜産系の天然調味料のメーカーです。2500品種を扱い、高度な技術力により、高級ホテルをはじめ2万社以上の取引先があります。本物志向、一貫生産、高付加価値を求めています。手間も時間もかかりますが、コクや風味を大事にしています。
製品の需要は変動が大きく、ライフサイクルは短い傾向があります。食品は新製品が次々に出て、需要も事前予想通りにはならないことが多く、いかに効率的に生産するかが、大きな課題です。これまで列車の時刻表のような生産計画を立て、工程を一つずつ基幹システムに入力していました。長いと10工程以上あり、生産変更に伴う書き換えも大変です。週3500件のデータについてチェックを行わなければならず、それに大半の時間をとられることもあります。こうした作業の属人化、スタッフの高齢化も問題になってきました。
売上高は右肩上がりなのに、スタッフが増えることはなく、限界にきていました。省力化のため、スケジューラ導入を決めました。導入に際し、力を入れたのは次のような事項です。
まずAsprovaのオプション機能である「重なりMAX」の活用です。食品製造には、工程と工程の間にあけなくてはならない時間があったり、逆に工程と工程の間があいてはならない場合があります。こうした生産工程を「重なりMAX」を利用して割り付けていきました。
次いで「副資源」機能の活用です。従来の工程表では、攪拌に続く次工程が1つの工程として処理されていました。この機能を用いて、表示が省略されていた工程をわかりやすく示すことができました。
さらにオリジナルのロジックを作成し、登録ミスをなくすことに努めました。
新人社員でもできた
期待していたのは、前述のような属人化の防止と、ミスの予防、高速な計画立案です。導入の結果、スピーディーに変更を実行でき、ミスも生じませんでした。チェック作業を省くこともできました。さらに可視化によって、生産設備の能力を引き出すことができました。生産実績は16%増。計画工数は43%減。年間1000万円のコストダウンを実現しました。製造現場管理者の業務は、年間500時間分の削減となりました。今は、入社2年目の若手社員が1年目からアスプローバを習得して、やっています。これまで長い経験が必要で、苦労して習得したものですが、一変しました。
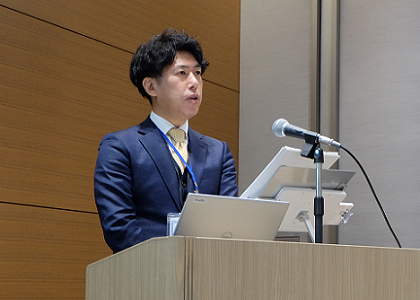
課題は、24%にとどまっている導入率です。拡大にあたっては、人材育成も必要になります。アジアやヨーロッパにも生産拠点があり、グローバルにAsprovaの活躍が広がることを期待しています。
次の段階として、ローコードツールのTALONの活用を図っています。Asprovaとの相性がよく、さまざまなデータを集約して可視化し、意思決定や課題解決を支援する「BIツール」として使えると考えています。
未知のソリューションを導入する際には、変化に対する不安が多かったのですが、ベンダーであるNSW社の助けもあり、成果を上げることができました。欲張りすぎず、スモールスタートで行ったのもよかったと思います。おかげさまで、社内でも成果を評価してもらうことができました。みなさまに心より感謝いたします。
(了)

コラム編集部

最新記事 by コラム編集部 (全て見る)
- 困ったこと35~作業指示と無関係に作業する人がいて困った - 2025年4月23日
- 困ったこと35~一生懸命やっているのに、理解してもらえなかった - 2025年4月23日
- 困ったこと35~「何でもできる」と思い込んでいる人に困った - 2025年4月23日