Solverで納期順守と効率化を両立
2023.11.19X0:ユーザーインタビュー2023年11月2日、東京駅前のミッドタウン八重洲で開催された「Asprovaユーザ会2023」で、アリアケジャパンと日本エー・エム・シーの2社が事例講演を行いました。日本エー・エム・シーで導入を担当した生産管理部・竹内有美子さんのお話を要約してお伝えします。
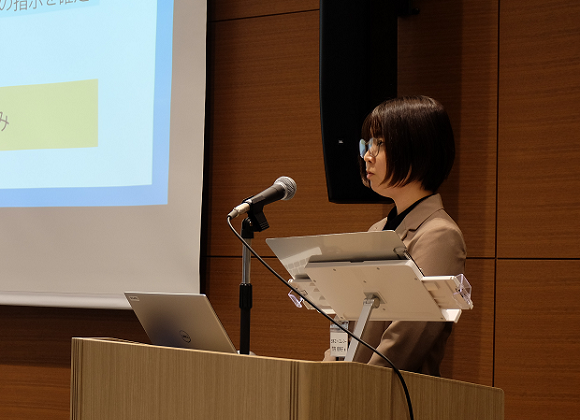
手動からの脱却
日本エー・エム・シーは、福井市に本社を置く高圧配管用継手の専門メーカーで、生産は国内の他、タイ、フィリピン、中国でも行っています。原料の金属を機械加工し、メッキ、組み立て、洗浄というシンプルな工程です。
従来の生産計画は、手動で立てていました。週ごとに700~800件の指示書がきて、一週間分まとめてエクセルで計画を作ります。時間がかかるので、休日出勤したり、丸一日かかりきりになったりして作業しました。飛び込み受注があると再計画しなくてはならず、無駄作りや無駄な日程も生じていました。
日々修正可能な計画を求めて、スケジューラ導入を図りました。高度な機能とシンプルな使い方が魅力で、Asprovaを選びました。
弊社では、Asprovaは、SAP(基幹システム)からマスター情報や製造オーダを受け取り、作成した作業指示情報をSAPに返します。Asprovaでは、自動計画作成により、3か月分の生産を平準化、必要に応じて手動修正し、うち直近1日分の作業のみを確定指示とします。指示書は3か月分で約7000件。1日分は150件ほどになります。手動で修正するのは、材料の有無や納期の前倒しに対応するためです。
導入の後、負荷の平準化や納期遅れの解消、見える化といった成果が得られました。
材料と治具の交換を大幅減
そしてさらなる改善と生産性の向上をめざしました。改善項目は、加工時間の短縮、段取り回数の削減、段取り時間の短縮の3点です。そのうち3つ目の「段取り時間短縮」について、AsprovaのSolverオプションを試してみることにしました。
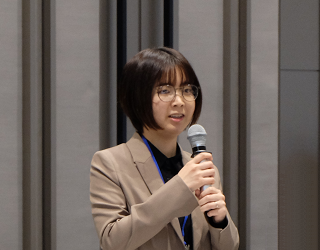
弊社の製品は1万種にも及びます。一方、1つ1つの製品は平均で20個~30個しか作らない多品種少量生産型です。そのため材料や工具・治具を交換する「段取り」を繰り返さなければなりません。1日10回以上やることもあります。段取り時間は、工具を交換する時間と、材料・治具を交換する時間の2つに分けられます。工具の方は種類が多く、改善が難しいため、今回は材料・治具の交換回数削減を課題に設定しました。
納期遅れがないよう、しかも同一材料を連続加工する生産計画を、Solverで作成します。材料を「副資源」に設定し、その切り替えを最小化することを目的としました。Solverは最適な計画を求めて、自動的に試行を繰り返してくれます。そして試行回数600万回程度で、約20分の計算により、よい計画が自動作成できることがわかりました。
これによって、3か月間の材料切り替えは、3210回から2138回に減り、1か月で50時間の削減となりました。Solver導入は、着手後半年という比較的短い期間で完了することができました。
次の段階として、段取りの中で、今回は難しいとされた工具交換の削減にも取り組み、生産性向上につなげたいと考えています。
(了)

コラム編集部

最新記事 by コラム編集部 (全て見る)
- 困ったこと35~作業指示と無関係に作業する人がいて困った - 2025年4月23日
- 困ったこと35~一生懸命やっているのに、理解してもらえなかった - 2025年4月23日
- 困ったこと35~「何でもできる」と思い込んでいる人に困った - 2025年4月23日