MRP glossary TOP > C > Capacity Requirements Planning CRP
Capacity Requirements Planning CRP
The manufacturing order planned through the material planning (MRP or parts explosion) is usually submitted to the administration division or the person in charge of administration that comprehensively control the manufacturing division, and the validity of its capacity and load is first determined. The manufacturing order is created for each item using B/M based on the production schedule through the material planning, and thus at this point the concept of process is not existing yet. But items are actually produced through a number of processes. Capacity Requirements Planning refers to the planning where the load for each process is grasped according to the manufacturing order, the adjustments are made, and then the work of each process is planned.
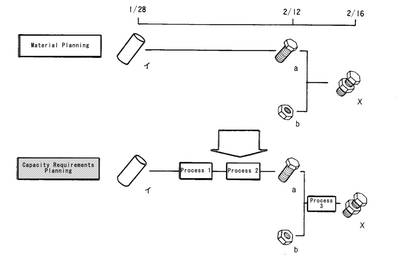
It is necessary to set the capacity after considering the current situation, in order to make Capacity Requirements Planning more practical. In this planning, the following three capacities are used:
- Standard Capacity:
- the ability to produce items in a standard process. The standard capacity is usually set for each process, and such time margin as morning meeting time and break time as well as attendance rate are also considered. In addition, Capacity may be registered for each operation date.
- Maximum Capacity:
- the ability to produce the maximum quantity/quality of items in a process. It can be set according to the actual performance or as an overload tolerance.
- Set Capacity:
- the ability to be set based on the relationship between the maximum capacity and load.
When setting the capacity, such factors as overtime work, shift, and the increase or decrease in staff transfer are considered.
Generally, capacity demand plan can be divided into four functions.
- Process spread:
- MRP calculate the amount of items required, but the actual operation instruction is for each process,Therefore, items level plan need to be broken down into process level plan.This subdivide function is called process spread.
- Load accumulation:
- Orders generated during process spreading called work orders. The work time that calculated when process spreading is recorded into work orders, the time is seen as the job load, calculate the load of each project.
This function is called load accumulation. - Load adjustment:
- Load adjustment happens in the earliest start time (get ready materials, the earliest time you can get to work) to latest start time (the latest start time that do not occur late delivery) scale.
- Ability adjustment:
- In case that unable to deal with by adjusting the load, overtime work, change shift,
outsourcing...est. can be considered.
On base of these functions and planner's adjustment to calculate capacity demand. work orders that generated in the plan, will be succeeded to the work plan.
Reference:JIT Business Research Mr. Hirano Hiroyuki