-- Asprovaをどのように導入されたかを教えてください。 |
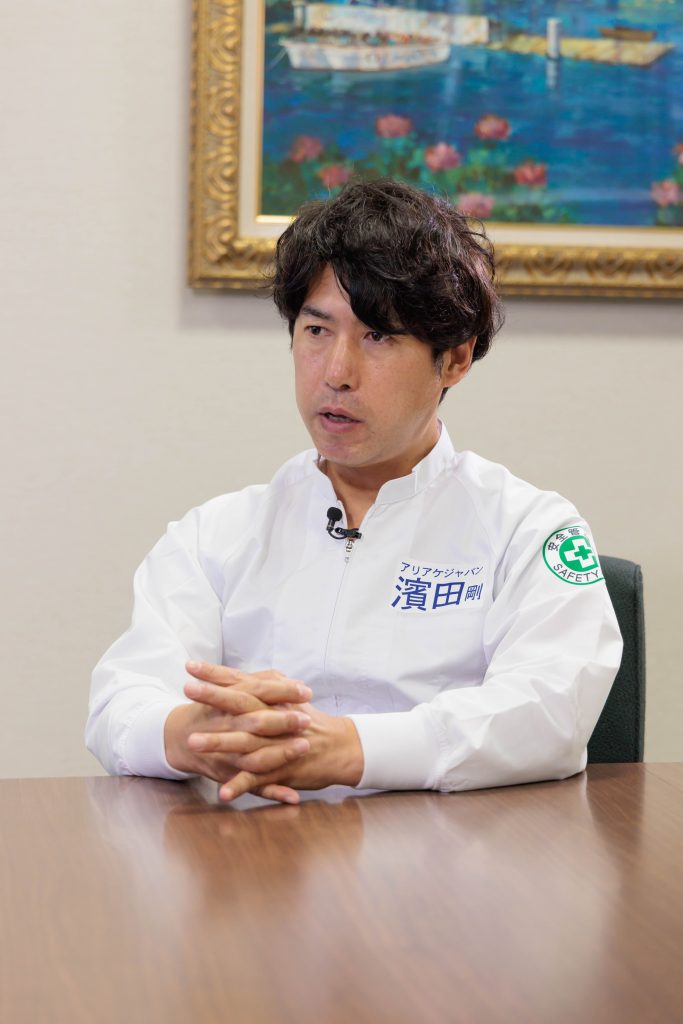
「生産工程の見える化により、さらなる改善ポイントが発見できました。」(濱田氏) |
扱っている品目が約2500種類あり、生産数量の変動が大きいため、生産計画の立案は経験豊富なベテラン社員に頼っていました。ありがたいことに弊社の売上は右肩上がりでアップしていますが、売上が少なかった過去から売上が増えた現在まで生産計画に携わるスタッフの数は同じです。今後も売上を伸ばしていくためには、従来のやり方では限界が来ていると考えざるを得ませんでした。少子高齢化、労働人口の減少などの問題に直面している現在、計画立案のノウハウを脱属人化してITシステムに移植し、省力化することがどうしても必要だと考え、生産スケジューラの導入を決めました。
システム導入では、製造現場、生産管理、情報システムのメンバーとプロジェクトを立ち上げて導入するのが一般的ですが、過去に生産スケジューラの導入を試みたものの実装までたどり着くことができなかった経験から、今回は下準備を入念に整えた上で、NSW様のお力を借りて導入までの協働作業を行いました。システム開発部門とユーザー部門が別れている場合、現場から出るさまざまな要求を開発側に正確に伝えられるかが不安でした。中途半端なコミュニケーションでは、使えるツールができ上がらず、仕様変更の嵐となってしまうのではないかと思い、今回の導入では誰かにまかせるのではなく、現場を知っている私が自分事として導入しようと決めました。 |
しかし、生産スケジューラについては全くの素人なので、NSW様から直接Asprovaについて教えてもらい、課題をどうやってAsprovaで解決するかを一緒に考え、工場でAsprovaのスケジューラを開発するということを繰り返しました。もともとは生産スケジューラを使いこなすなんて無理なんじゃないかと思っていましたが、少しずつ課題のレベルを上げて取り組むうちにロジックの入力やメンテナンスができるようになりました。
最初に行ったことは、生産工程とさまざまな条件をマスター化して、工程間の紐付けを表現することでした。これにより、生産計画を立案するときに頭の中で行っていたことを見える化でき、手応えを感じました。そうやってAsprovaを自分で動かしながら、検討を重ねた結果、あまり欲張らずに難易度の低い工程から開発を進め、一つずつ成功体験を積み重ねていくやり方を取りました。スモールスタートですね。その過程では、開発したスケジューラを無料体験版で動かし、要求にマッチしているのかを何度も確認しました。
この試行錯誤の過程では、NSW様には大変に力を貸していただきました。自分事として導入すると決めたとは言え、始めは右も左もわからないような状態でしたから、NSW様にAsprovaの設定箇所や条件式について根気強く教えていただき、課題解決の方法を考え、実装し、テストするまでをサポートしていただきました。導入ありきではなく、時間をかけて課題解決の相談に乗っていただき、さまざまなアイデアを出していただいたことで導入が進みました。現場の要求を導入支援ベンダーに直接伝えられたのもスムーズに導入できた一因です。 |
-- NSW 中野氏のコメント |
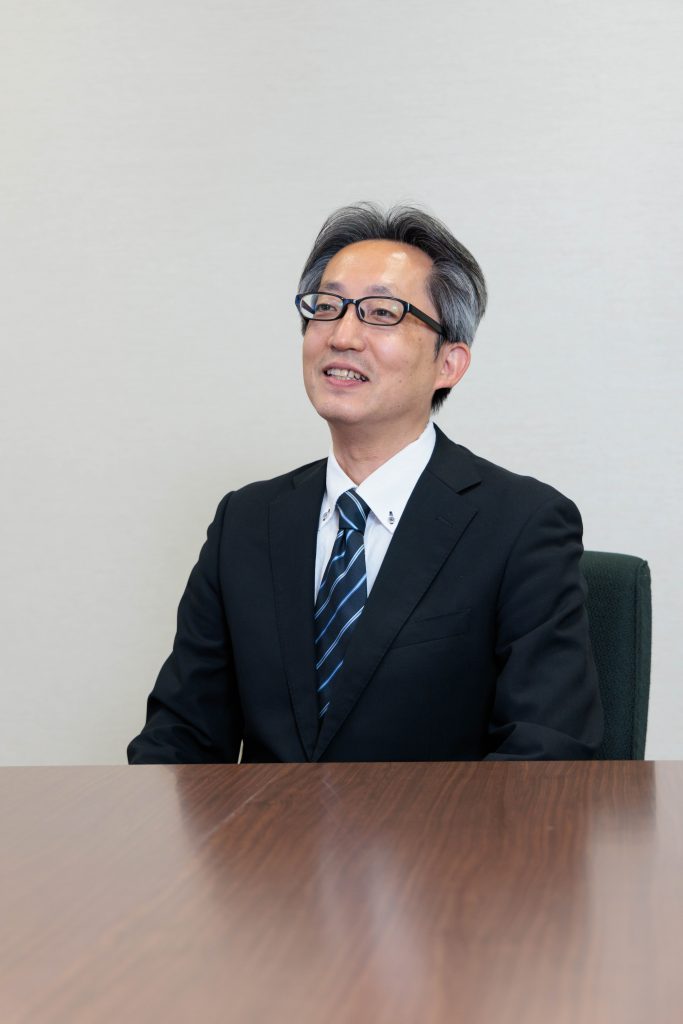
「今回のように、ユーザーが自らAsprovaを理解して導入するやり方は中小企業に向いていると思います。」(中野氏) |
通常の導入プロジェクトでは、スケジューラの要件定義から設定支援までを一連でお引き受けするケースが多いのですが、アリアケジャパン様は自らAsprovaの仕組みを理解された上でお使いになるという珍しいケースです。アリアケジャパン様が生徒さんで、弊社が家庭教師のような形でサポートさせていただきました。
今回の成功要因の一つは、現場をよくご存じの濱田様が先頭に立って導入を進められたことだと思います。通常は、ユーザー部門-システム開発部門-導入支援ベンダーというようにワンクッション入るので、現場の要望がうまく導入支援ベンダーまで伝わらないことがありますが、今回は現場が主導したため、現場のニーズに合っているかを徹底して検討することができました。
今回のケースでは、弊社の労力は通常の1/10程度で済んでいるので、コストを抑えてAsprovaを導入する際の一つの事例となるのではないかと思います。弊社に一通りおまかせいただくケースに比べると、立ち上がりの時間はかかるかも知れませんが、長い目で見ると発展するスピードが上がるのではないでしょうか。 |
-- 導入前にはどのような効果を考えられていましたか。 |
先ほどもお話ししたように、課題は属人化、高齢化、計画変更にかかる膨大な工数の3点です。生産スケジューラを導入することで、さらに以下の3点も実現したいと考えていました。
1)初案の計画を立案した後の修正を減らしながら、ミスも予防できること
2)見える化により、生産設備の持つ能力をさらに引き出すスケジューリングができること
3)シミュレーションを兼ねた計画変更を、繰り返し高速で実行できること
導入してみて、まず感じたのは生産計画の変更が素早く、簡単に行えることです。以前は、膨大な手作業で対応していた生産計画の変更を生産スケジューラは愚痴一つ言わずやってくれます。しかもミスがありません。また、生産工程を変えるとどうなるかというシミュレーションにも使えるので、生産工場の選定も的確に判断できるようになりました。
先行導入した部門では、計画立案後の変更が非常に多く、スピーディーな計画変更が不可欠です。計画立案にAsprovaを導入した結果、生産量を過去の実績換算で16%アップできました。また、製造部門2部門の管理者の工数を年間約500時間削減し、生産計画立案担当の工数は43%削減でき、大きな成果が出ました。さらに生産計画を見える化したことから、波及効果として年間1,000万円のコストダウンを行うことができました。 |