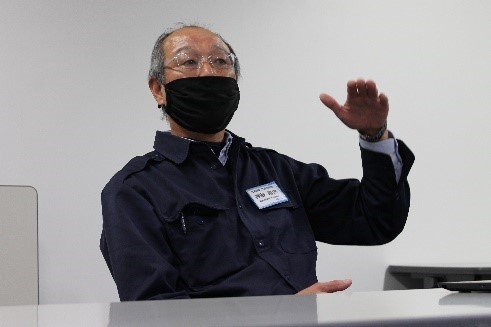
「充電工程をコントロールすることが在庫削減のキーポイントです。」(神谷氏)
バッテリー製造には課題が多いので、生産計画は担当者が手動で立案し、毎日更新していました。しかし、過去2年連続で欠品を出してしまい、大きな機会損失が出てしまったため、生産計画の立て方を見直すことになりました。生産計画のDX化を推進する取り組みを行い、その一環として数年前にAsprovaを導入しましたが、期待していたような効果は得られませんでした。
その理由は、見込み生産をしながら、生産効率を上げるために充電槽をフル稼働させたいという難しい要求があったからです。弊社の場合、いくつかある充電槽の大きさが異なるため、どの品種をどの充電槽で充電するのかを決めないと充電槽をフル稼働させるだけの生産数量が決められません。我々が求めていたのは、受注生産のようにあらかじめ決まった数量を充電槽に割り当てて最適化することだけではなく、最も設備利用効率が良くなるように生産数も最大化する生産計画を立てることでした。
Solverを導入する前は、Asprovaで立案した計画を実際の計画に落とし込むには人の介在が不可欠でした。在庫数と見込み要求数を見ながら、充電槽がフル稼働するようにAsprovaの計画を手動で修正するため、毎日、計画立案に約2時間、手動修正に約1時間かかっていました。しかも手動修正は専門的な知識が必要になるので、作業が属人化していました。結果として、手動修正で生産計画の精度は上がっても、人的コストが上がってしまうというジレンマに陥っていたのです。この解決法が思いつかず、悶々としている中にSolverのご提案を頂き、ジレンマを解決できるポテンシャルがあるとピンと来たことから、開発に参加しました。
「Asprovaは受注生産向きかつ、人の介在が不可欠なツールだと感じていました」と中林氏。仮に見込み要求数が100個だとしても、充電槽をフル稼働させるために受注を先読みして120個作っても構わないのです。しかし、生産スケジューラでそんなことができるとは思ってもいなかったので、今回Solverで先読みして生産計画が立てられるようになったのは、とても面白いと思います。
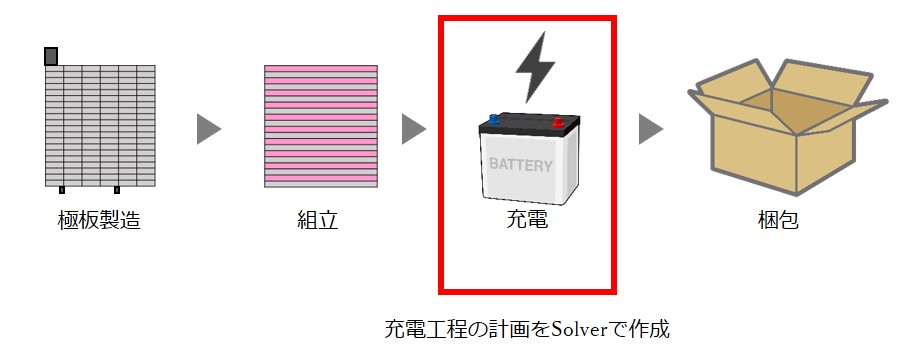
|