-- Asprovaをどのように導入されたかを教えてください。 |
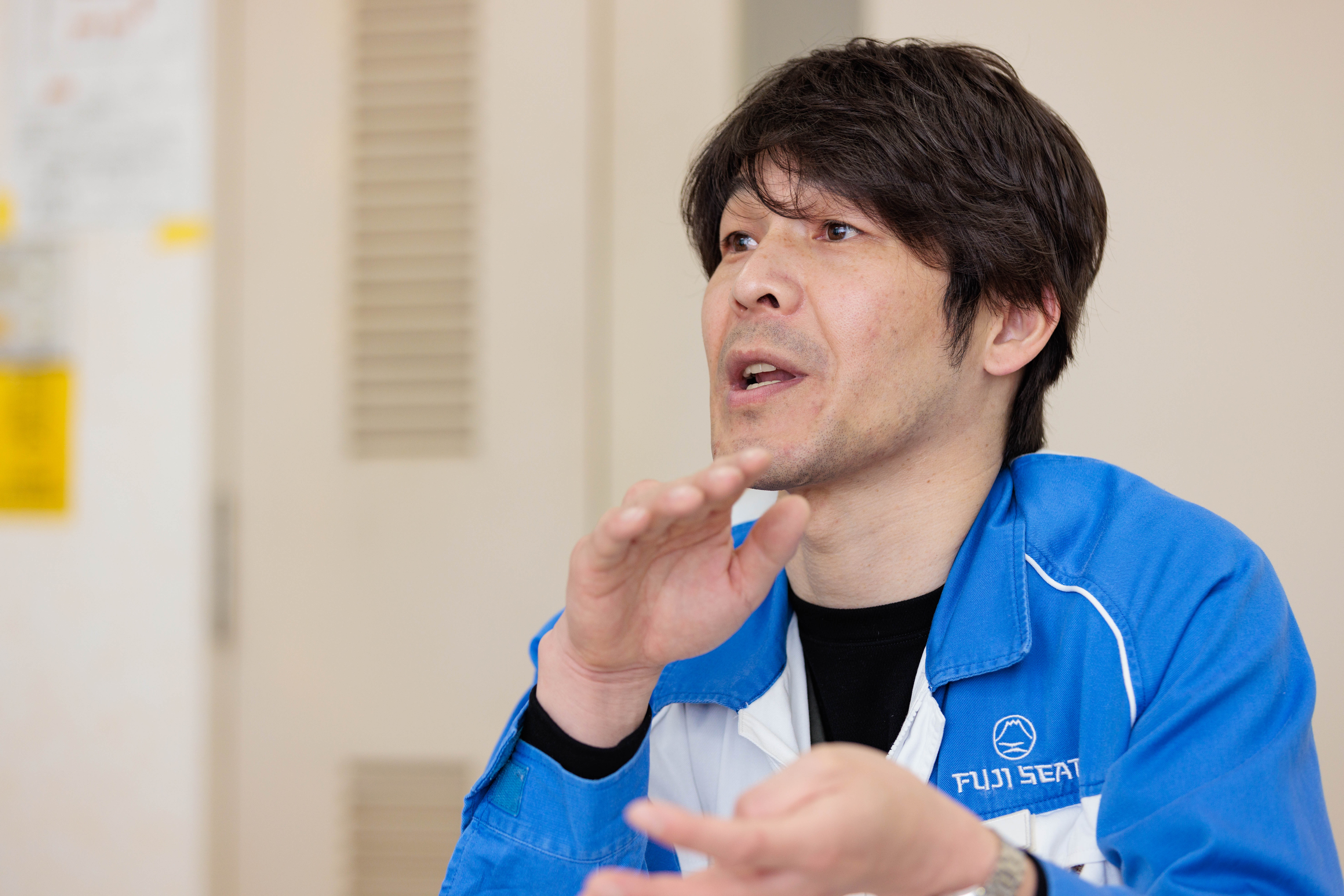
「システム化にアレルギーがある社内で説得を重ね、ようやく導入できました。」(南氏) |
工場をご覧になるとわかると思うんですが、弊社は自動車用シート製造の老舗です。滋賀第1工場も32年の歴史があります。そのため、仕事でも古いやり方が残っていまして、いまだに手書きや手計算をしているところがあります。会社の中にも、システム化でスマートに仕事を進めるよりも人手をかけて手作業で取り組む方がいいんだという雰囲気があります。こういった中でプレス工程のシステム化までには、いくつか苦労がありました。 |
以前に別の部署でシステム化に失敗したことがあるので、システム化に対するアレルギーが社内にありました。数年前にもプレス工程のシステム化を提案したのですが、そのときは否決されています。やはり「システム化のコストに見合う効果が得られるのか?今までどおり人手でやればいいのではないか?」という疑問に堂々と答えられないと、承認してもらえません。今回、導入をサポートいただいたパナソニックさんと一緒にシステム化のメリットを資料にまとめ、何度も提案を重ねて、ようやく社長からOKをもらいました。
プレス工程のシステム化のメリットは、4つあると考えていました。
1)生産計画立案の工数削減
2)在庫量の削減
3)生産計画立案の脱属人化
4)生産計画を立案する現場管理者が本来の管理業務に専念
システム化が承認されてからも、すんなり導入できたわけではありませんでした。手作業に慣れているところに生産スケジューラを導入するとなれば、現場から反発を受けることが予想されます。そこで、あえてパソコンに不慣れな担当者をスカウトし、彼にAsprovaの使い方を覚えてもらうことでパソコンが得意ではなくても使えることを現場に浸透させようと思いました。 |
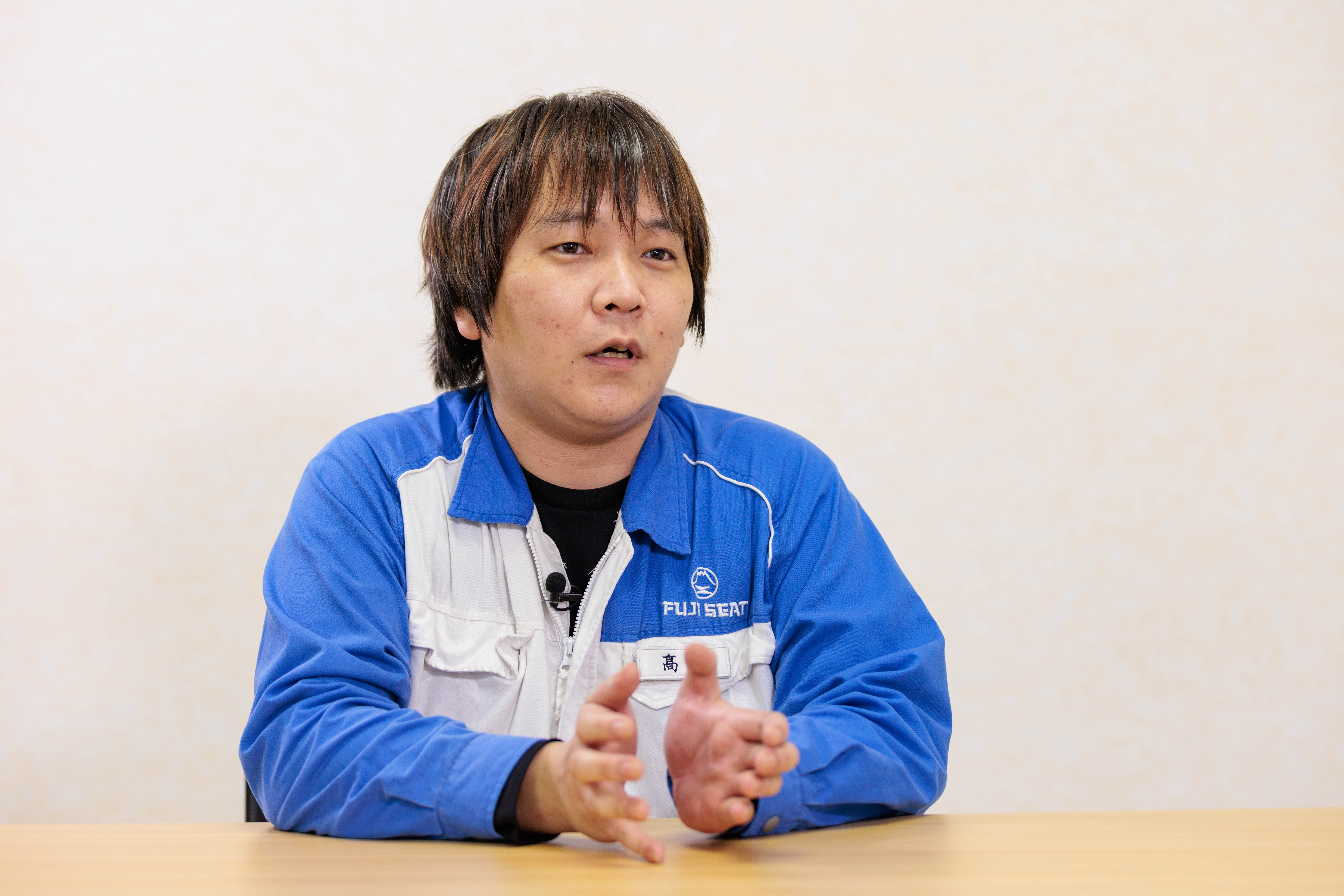
「Excelも使えなかったのですが、パナソニックさんにOJTで教えてもらい、慣れることができました。」(高橋氏) |
他部署からスカウトされた高橋班長は、着任したばかりの頃をこう振り返っています。
「Asprovaどころか、パソコンも不慣れだったので、最初は無理なんじゃないかと思いましたが、パナソニックさんが丁寧に教えてくださるので、徐々に操作にも慣れていき、自信が付きました。今では、以前のような手計算に戻れと言われても、とてもできないと感じます。今後はAsprovaマスターとして、使い方を広めて行きたいと思っています。」 |
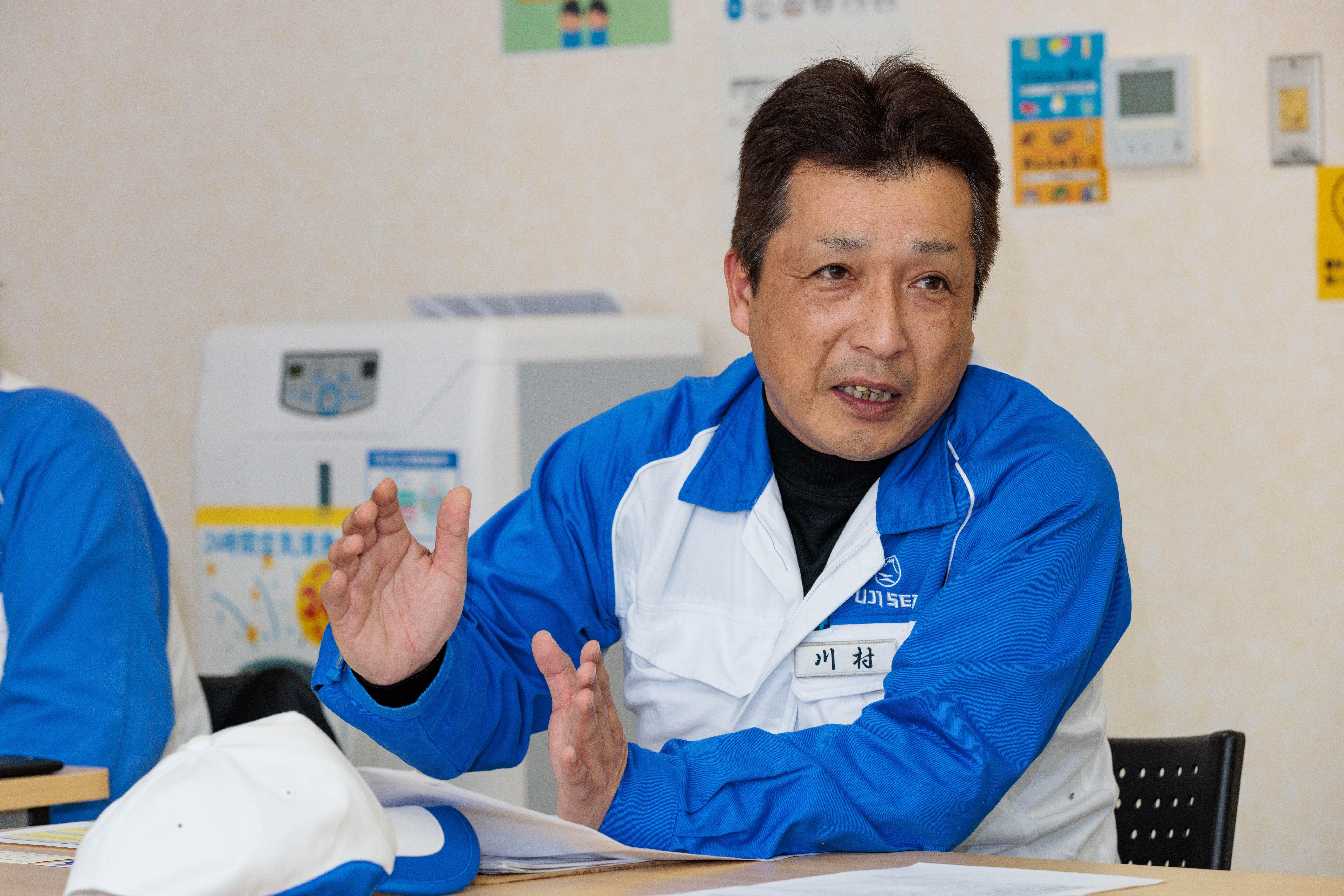
「条件設定には悩みましたが、現場密着型でサポートしてもらい、スムーズに導入できました。」(川村氏) |
Asprova導入作業を担当した川村係長は、マスター準備で条件の設定に悩んだそうです。
「実際の生産の動き、プレス機ごとの特性、稼働率などの条件設定に一番苦労しました。例えば、金型交換作業はどういう条件を設定すればいいのか。また、本来ならば一度にプレスできる左右ペアの部品の必要数が左右で違う場合などイレギュラーな設定をどう実現するのか悩みました。それでも、困ったことがあると、パナソニックさんに相談して要望を聞いてもらい、プロトタイプをまた改善していくというやり方を繰り返して計画の精度を上げていきました。」 |
-- パナソニック 迫田真士氏のコメント |
要件定義で欲張らず小さいところから始めたことが、導入が成功した理由ではないかと思います。富士シート様はマンパワー重視型で、システム導入には慣れていらっしゃいません。通常であれば、導入の際は[要件定義]-[構築]-[テスト]-[導入]というウォーターフォール型のプロセスで進めますが、今回は最初にすべての要件を定義するのが難しいので、小さく要件定義をして、プロトタイプを作り、ディスカッションして改善していく、アジャイル型のプロセスを採用しました。手間はかかりましたが、早い段階で業務が理解できたので、最終的な精度も上がりました。昨年12月に導入して3か月経過していますが、不満やトラブルは出ていません。もし、これがウォーターフォール型のプロセスで導入したとすれば、稼働後にさまざまなトラブルや変更要求が出て、修正が大変だったでしょう。
今回の導入はプレス工程1つだけなので、パイロット1か月、導入4か月と短い期間で導入できました。 |
-- Asprovaを選んだ決め手は、何でしたか? |
他社製品も検討しましたが、パナソニックさんの製品説明が弊社の理想に一番近かったのが決め手となりました。また、ITの専門家でなく、誰でも使えるというのもポイントです。パナソニックさんとは溶接ロボットでお付き合いがありましたが、プレス工程のシステム化でも親身になってサポートしていただき、現場に密着して進めてもらったのが良かったと思います。 |