Asprova導入後、さらなる改善をめざしてSolver PoCを進めた経緯について伺いました。
Asprovaを使って生産計画作成の自動化とリソースの見える化を行い、以前に比べればはるかに効率が良くなりました。生産管理部としての業務は確立できたので、次のステップとして生産計画の視点から生産性を向上できないかと考えました。
弊社は典型的な多品種少量生産型で、生産品目は1万種類前後ありますが、1回の生産指示で生産する数量は平均20~30個です。そのため、ある製品を作り終わると次の製品、次の製品が終わるとその次というように、加工する製品を切り替えるたびに段取りを繰り返します。この段取りに使う時間に目を付けました。
生産リードタイムは、大別して、1)段取り時間、2)加工時間、3)その他除外時間で構成されます。生産管理部で2)と3)を短縮することはむずかしいのですが、段取り時間なら短縮できるのでないかと考えました。弊社での段取り時間は、主に加工する工具を切り替える時間と材料・治具を交換する時間の2つの合計です。交換する時間を短縮できれば、生産リードタイムが短縮できて、生産性を向上できます。いろいろと調査してみると、加工する工具は種類が大変多く、交換時間を短縮するのはむずかしいことがわかりましたので、材料・治具の交換回数削減を課題に設定しました。とは言え、材料の数だけでも1,000~2,000種類もあり、治具も1設備あたり1日に7回、多い設備では10回ほど交換するので、どう実現するかに頭を悩ませました。
―― 生産性向上のアプローチ ――
当初は、材料・治具の交換回数の削減をAsprovaの標準機能で実現しようと試行錯誤したのですが、なかなか思い描いたような生産計画になりませんでした。導入ベンダーのAJSさんに相談してみると、Asprovaの標準機能ではむずかしいかもしれないが、アスプローバ社で開発しているSolverというオプションを使うと解決できるかもしれないとのお話を聞き、アスプローバ社にお話をつなげていただきました。
目標:生産性1%向上
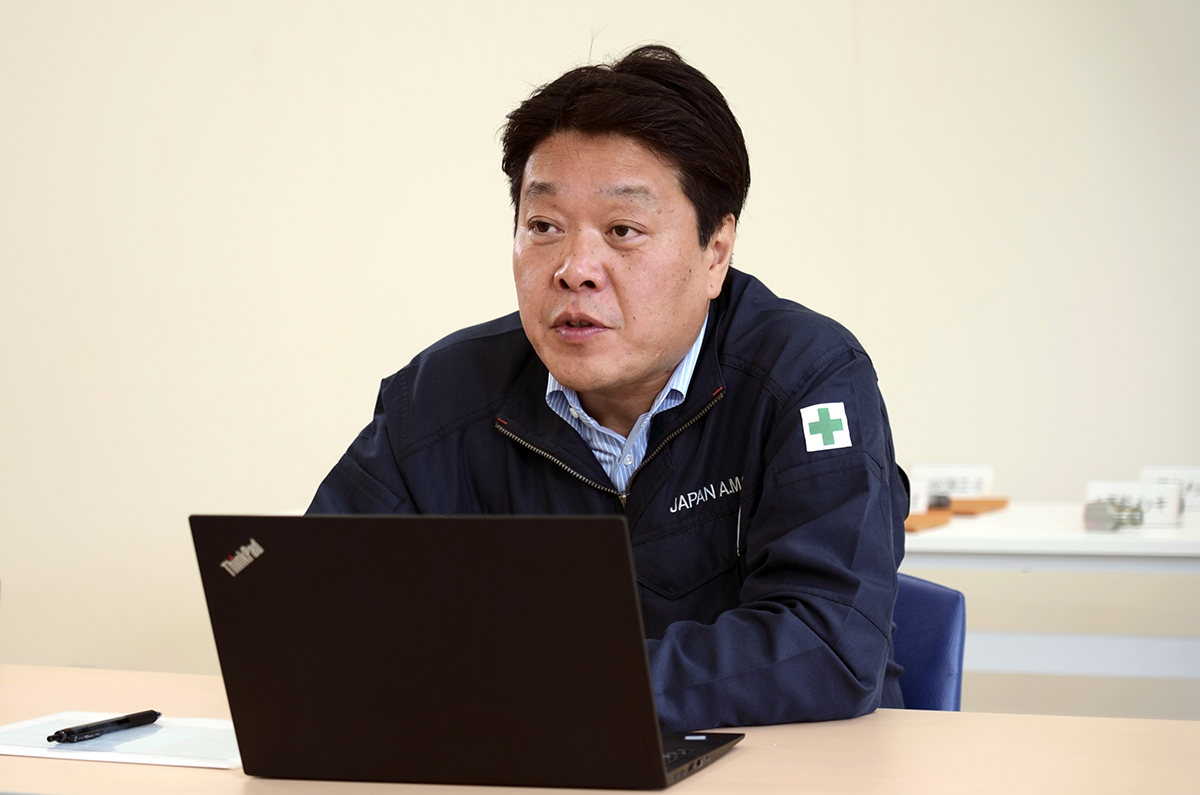
生産管理部 部長 有川氏
「生産計画の視点から生産性向上にアプローチしました」
Solver開発への参加を社内で承認してもらうために、「生産性を1%向上させる」という数値目標を掲げました。この目標を実現するための具体的な手段は以下の2つです。
- 顧客納期遵守を優先した上で、同じ材料を使う製品を連続生産するように生産計画を立てる。これにより、治具の交換回数を最少化でき、段取り時間を短縮できるので、設備稼働率が向上できる。
- 同じ材料を使い続けることにより、材料倉庫での出庫時間と外段取り時間を短縮できる。
合わせて、生産計画を作成する時間の短縮にも取り組みました。これも、手動で行っていた序列変更作業の時間を1か月あたり10時間短縮するという数値目標を立てています。このように目標を数値化して費用対効果を明確にしたので、社内の承認は早めに得ることができました。
アスプローバ 今岡竜也のコメント
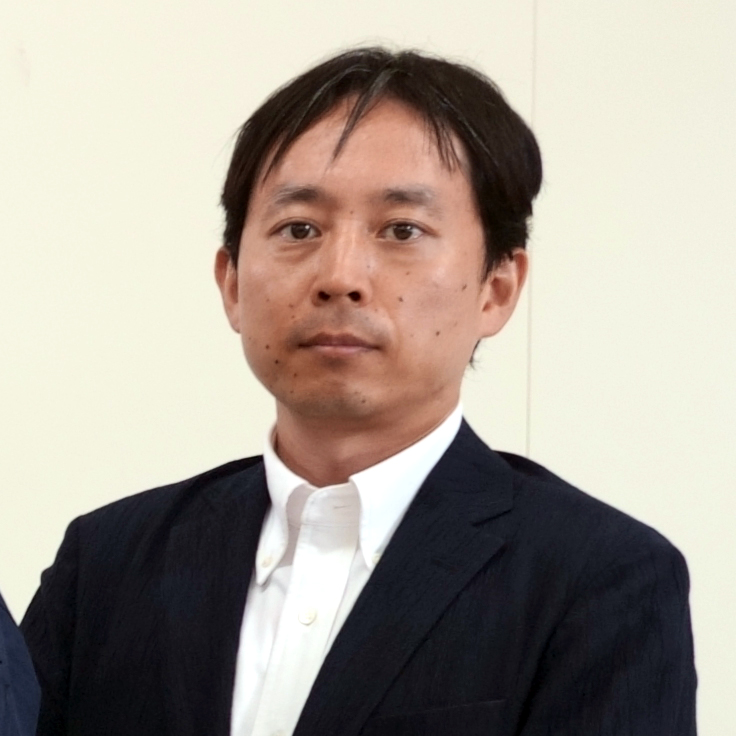
本来Asprovaはプログラミング不要で生産計画を作成できるツールなのですが、お客様の実情に応じた生産計画を作成するにはプログラミングと同様なロジック設定が必要になってしまうのは、お客様にやさしくないと思っていました。Solverはこの課題を解決するためのオプションで、お客様に「生産計画の良否を判定する指標」だけを設定していただくと、指標に基づいてSolverが良い計画を作成するというアプローチです。日本エー・エム・シー様では生産計画の指標と要件が明確でしたので、Solverの開発が4か月、日本エー・エム・シー様のテストが2か月と短期間で導入できました。
|