Interview
誰でも使える工場最適化へ ――
製造現場のDXを加速させる
Solverの挑戦
製造現場のDXを加速させる
Solverの挑戦
Ito Hayato
伊東 勇登
Solver開発チーム
エンジニアリングマネージャー
エンジニアリングマネージャー
生産スケジューラーの永遠の課題は、どんな製造現場でも最適化された専門性と、簡単に導入できる使いやすさの両立だ。この課題に正面から取り組む、エンジニアリングマネージャーの伊東氏にお話を伺った。
「より多くのお客様に使っていただけるパッケージ製品を開発したことが、転換点だったと思います」
伊東さんのお仕事内容についてお聞かせください。
伊東
私は、最適化を担当するSolverチームでエンジニアリングマネージャーを務めています。それこそお客様の要件定義から、試作品の作成方針の決定、チームメンバーのアサインなど、プロジェクトマネジメント全般を、お客様と弊社メンバーと相談しながら決めているって感じですね。
なるほど、プロジェクトマネジメントと、お客様との関係構築の両面で重要な役割を担ってらっしゃるんですね。そんな伊東さんの印象に残っているプロジェクトについて教えていただけますか?
伊東
2022年の、Solverの汎用製品の開発が特に印象に残っています。弊社のSolverは、もともと、各ユーザー様の個別要件に応じたカスタム開発が中心でしたが、より多くのお客様に使っていただけるパッケージ製品を開発したことが、苦労もしたし、転換点だったと思います。
そのプロジェクトではどのような課題がありましたか?
伊東
最も難しかったのは、個別のカスタマイズ要件から汎用的な機能をどう切り出すかという判断でしたね。例えば、“製造を始めたら夜や休日に中断してはいけないという制約のもとで、製造できる時間帯を見つけるというニーズに対応する機能”などですね。最初の汎用化の際にはそこまでやると開発も大変で精度の担保も難しいということで、そういった制約には対応しないという判断をしました。お客様のニーズと、エンジニアの開発のしやすさ、そして会社の方針、この三つのバランスを取りながら進めていくのが最も難しく、また面白かった部分です。幸い、社長や会長がアジャイル開発を推進していたこともあり、「お客様に言われていないことは考えてもきりがない」という方針のもと、必要最小限の機能から着手し、徐々に拡充していく アプローチを取ることができました。
20-30時間の作業が2-3時間に短縮。属人化も解消へ
開発はスムーズに進んだのでしょうか?
伊東
その点、最初のパイロットユーザーとの出会いが大きかったですね。コニカミノルタメカトロニクス様や、自動車関連産業の子会社様など、比較的シンプルな要件のお客様とその時期に出会えることができました。1工程、1設備という基本的な構成で、作業を並び替えて納期遅れと段取り工数を最小化する。そういったシンプルなニーズに応える中で、汎用製品の核となる部分が見えてきました。PoC(実証実験)の段階で、こうした理想的な企業様と巡り合えたことは、本当に幸運でした。そのおかげで、立ち上げ時の苦労は想定していたほどではありませんでした。
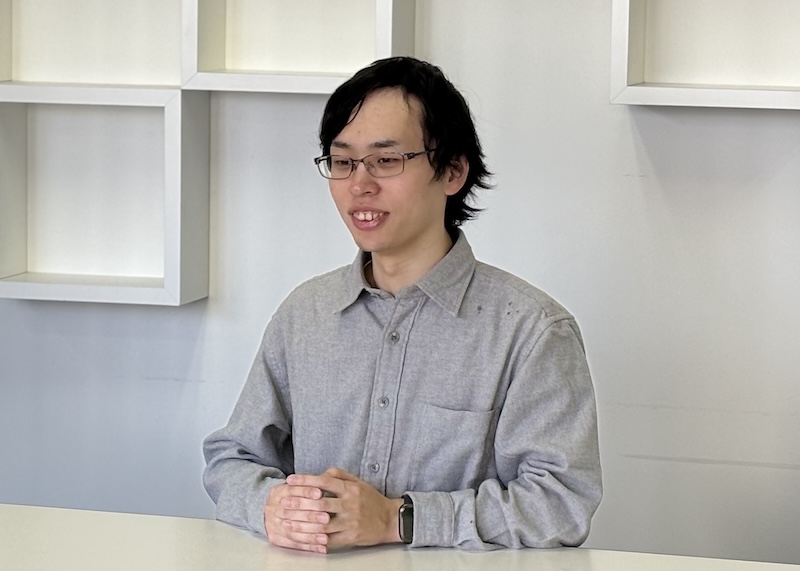
現在の進捗状況はいかがでしょうか?100点満点にするとどれくらいでしょう?
伊東
2024年の12月に、複数工程に対応したSolverをリリースすることができ、これは大きな進歩だと考えています。これまでは1工程のみの対応でしたが、複数工程への対応ができるようになったことで、より多くのお客様に興味を持っていただいてもらっています。理想的なゴールから見るとまだまだ20~30点くらいですが、簡単な加工業や部品加工、簡単な組立てなどに対しては50~60点くらいのところまで来ているのではないでしょうか。
実際の導入効果はいかがでしょうか?
伊東
ありがたいことに、加工業や組立産業のお客様からかなり好評の声をいただいています。「2週間に1回、20-30時間かけていた調整作業が2-3時間で済むようになった」とおっしゃっていただきました。また「人手での調整よりも機械(Solver)に任せた方が、納期遅れや段取りの面で良い結果が出ている」との評価もいただいています。さらに、工場内の個別システムに入れないような現場の調整も最低限で済むため、属人化の解消にも貢献できているようです。
気軽に導入ができる、工場最適化のデファクトスタンダードへ
今後のビジョンについてお聞かせください。
伊東
誰でも導入できるレベルになることが、大きな転換点になると考えています。現状、工場のDX化はかなり難しく、例えば担当者1人や小さな部署が自力で業務用ソフトを導入することは、生産管理ソフトウェアに限らずそれなりに難しいです。だからこそSIerさんやSEさんの存在が必要とされているんです。それに対して、私たちは業種別パッケージという形で、導入をすごく楽にするツールを提供しようとしています。例えば加工業の方であれば、用意されたボタンを押すだけで、ほとんどSEさんの手を借りずに導入できるような形を目指しています。それによりSEさんには、システムとの連携や、どのようにシステムにデータを入れていくかといった、現場に密着したオペレーションテクノロジー的なところに注力していただく。ITの部分については、現場の担当者レベルで最低限の知識があれば導入できる、そんな状態を目指しています。
それが実現すると、どのような変化が起きるとお考えですか?
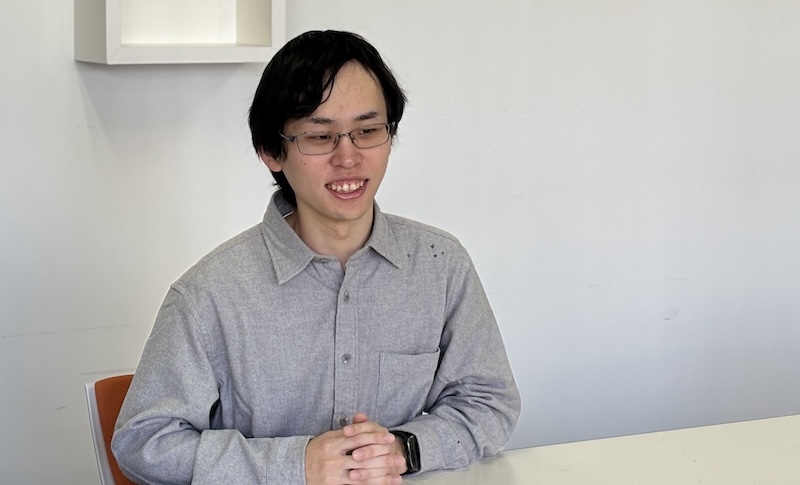
伊東
現状では製品の導入に関しては部門が上司に承認を取り、SIerさんと契約を結び、検証期間を設けてテストを行うという長いプロセスが必要です。それが「これ面白そうだから使ってみよう」という感覚で導入できる、いわばBtoC製品に近い形で使えるようになれば、大きな転換点になると思います。そうやって気軽に導入できれば、「ちょっと試してみよう」という気持ちになり、うまくいけばそのまま使い続け、「あれ、よかったよ」という一言が次の導入を生む。そういう好循環が生まれていくと考えています。
それにより、「このSolverは素晴らしい」とお客様同士で評判が広がっていくような状態が理想です。現在は私たちから積極的に導入効果を確認させていただいていますが、将来的には自然と評判が広がっていくような、工場の最適化のデファクトスタンダードになっていくような、そこまでいくと夢がある、誇らしい話だなと思います。
近年、AIの活用が進んでいますが、SolverとAIの関係性についてどのようにお考えですか?
伊東
AIテクノロジーは二つの側面から捉えています。一つは、製造時間の推定や、ChatGPTを活用した“Techアシスタント”機能など、補助的な機能としての活用です。私たちは、既に取扱説明書や仕様書の内容をAIに学習させて、お客様の質問に答えられる仕組みを実装しています。
では、Solverの核となる最適化の部分ではいかがでしょうか?
伊東
そこはAIによる代替は相当先の話だと考えています。現在のAIは似ているものを探すパターンマッチングが基本ですが、生産スケジューリングでは一つの判断が後続の工程全てに影響を及ぼすため、曖昧な判断は許されません。この領域でAIが実用レベルで活用できるようになるのは、早くても10-20年後ではないでしょうか。
AIとSolverの違いについて、もう少し詳しく教えていただけますか?
伊東
AIの本質は「曖昧さ」を含む判断の連鎖なんです。例えば、AIが「この工程は2番目っぽい」という判断をすると、その曖昧さが次の判断、その次の判断にも影響していきます。それぞれの判断に含まれる曖昧さが掛け合わさって、最終的な出力は砂の城のように不安定なものになってしまいます。
一方、Solverは明確なロジックと判断基準に基づいて意思決定を行います。「この工程をなぜ2番目にするのか」という判断根拠が明確で、その判断がどのように後続の工程に影響するのかも予測可能です。生産管理においては、この予測可能性と確実性が非常に重要になってきます。一つの判断ミスが大きな影響を及ぼす可能性がある製造現場で、Solverは確実な根拠に基づいて最適な順序を導き出しています。
あらゆる工場でスケジューリングができるSolverを目指して
なるほど、そこが現状のAIでは全く向いていないのですね。ではSolverのこれから目指していく方向性についてはいかがでしょうか?
伊東
現状のSolverは加工・組立・成形業界向けが中心なんですが、醤油や牛乳、洗剤といったプロセス系の製造などにもさらに領域を広げていきたいと考えています。
私が現在のSolverを“20-30点”あるいは“50-60点”程度だと評価している理由は、対応できる範囲がまだ限定的だからです。現時点では、最も単純な製造工程、つまり「部品を受け取り、加工して、次工程に流す」といった一連の単純作業にしか対応できていません。
しかし、私たちは、今後5-10年かけて、あらゆる種類の工場でスケジューリングができるSolverを開発していきます。これは技術的に大きなチャレンジで、なぜなら、業種が変われば必要なロジックや最適化手法も大きく異なってくるからです。いちプログラマーとしても一から勉強し直し、試行錯誤を重ね、各業界特有のニーズを深く理解していく必要があります。
素晴らしいチャレンジだと思います。
伊東
はい。なのでSolverは今後、二つの方向性を同時に追求していきたいと考えています。一つは、先ほど申し上げた通り、個別の業種や現場に最適化された専用Solverの開発です。それぞれの業界特有の課題や制約に対応できる、きめ細かいソリューションを提供していきます。
もう一つは、BtoCのように簡単に導入できる使いやすさの実現です。現状、生産管理システムの導入には専門家の支援が必要で、時間もコストもかかります。これを、現場の担当者が自分で導入できるレベルまで簡単にしていきたいです。
この、一見、相反する二つを同時に実現することで、日本中、世界中のあらゆる工場の最適化問題をSolverで解決する、という状態になるのかなと思います。
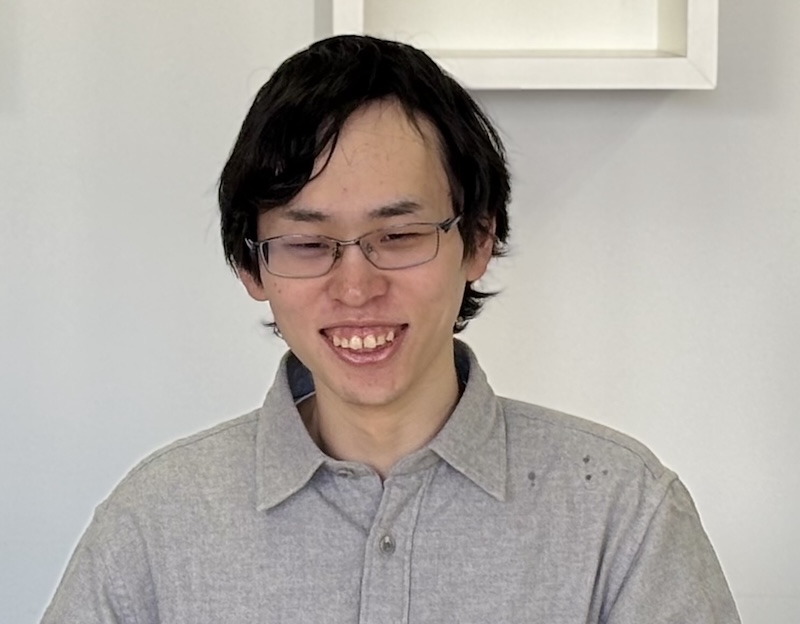
伊東
なるほど。そこまでいくと、工場内のそういう生産管理業務に関わる会話が変わってくるのかなという気がしますね。今日はありがとうございました。