MRP glossary TOP > Cost Control > Job Order Cost System
Job Order Cost System
Job Order Cost System
It is a calculation method used in such a production form that individually different products are produced according to the manufacturing instructions, or in a job-order production form. According to the issued manufacturing instructions of each product, each cost is divided into direct costs and indirect ones, where direct costs are accumulated by manufacturing instructions, while indirect costs are allocated according to a certain standard, and then added to the product cost by manufacturing instructions, by which the product cost is obtained.
In the Job Order Cost System, a product cost is individually calculated, and thus it is possible to properly evaluate the profit expectations for each order, and the result can be also used as basic documents for subsequent cost estimation. But, it takes much time and cost because of the calculation for an individual product required, leading to unreliability of the allocation standard and allocation calculation itself.
Related term: Cost Accounting
It is a calculation method used in such a production form that individually different products are produced according to the manufacturing instructions, or in a job-order production form. According to the issued manufacturing instructions of each product, each cost is divided into direct costs and indirect ones, where direct costs are accumulated by manufacturing instructions, while indirect costs are allocated according to a certain standard, and then added to the product cost by manufacturing instructions, by which the product cost is obtained.
In the Job Order Cost System, a product cost is individually calculated, and thus it is possible to properly evaluate the profit expectations for each order, and the result can be also used as basic documents for subsequent cost estimation. But, it takes much time and cost because of the calculation for an individual product required, leading to unreliability of the allocation standard and allocation calculation itself.
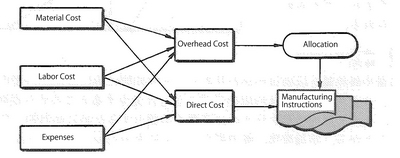
Related term: Cost Accounting
Reference:JIT Business Research Mr. Hirano Hiroyuki
Internal Cost and External Cost | Cost Control | Overhead Cost