生産スケジューラを導入しやすい工場と導入しにくい工場
生産スケジューラを導入しやすい工場と導入しにくい工場
生産スケジューラの導入のしやすさは、社内業務のシステム化の進み具合、製品点数や生産資源の数など、プロジェクト開始前に予測できる要因だけでなく、組織内の部門間の関係や計画立案者のシステム導入に対する理解度によっても変わってきます。
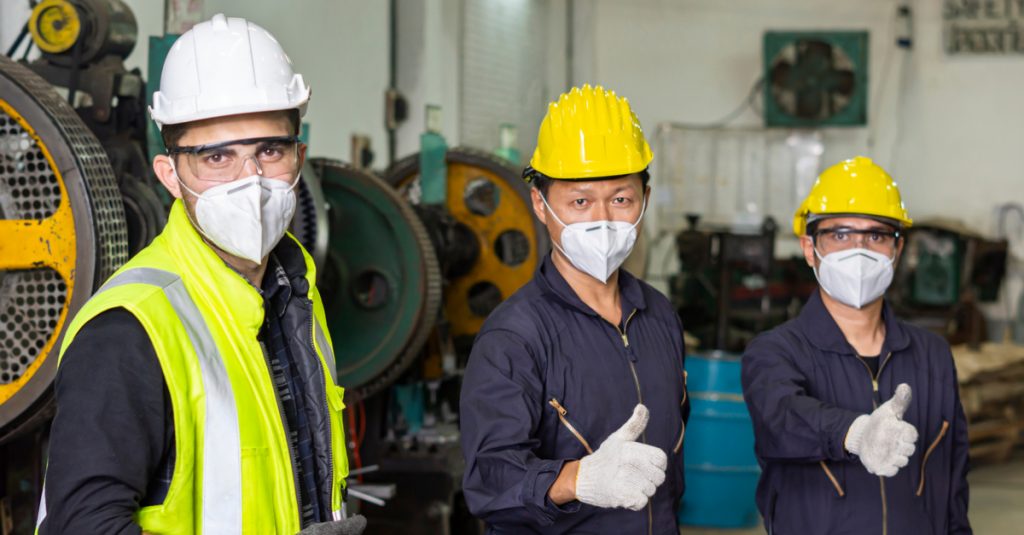
(1)生産スケジューラの導入のしやすさの基準
工場の生産管理業務のシステム化の進み具合は多種多様で、高額なERPシステムを導入し、MRPを回して購買オーダと製造オーダを発行し、実績入力を行うことでシステム内で予実管理出来ているレベルの高い工場もあれば、ERPは導入済みだがMRPは使っておらず、ERPから必要な情報をExcelにエクスポートし、外で生産スケジュールを作成している工場もあります。
生産スケジューラを導入するには部品構成表(BOM)や品目別の標準作業手順、や標準作業時間(能率)が必要であるため、当然ながらERPシステムのマスタがきちんと整備された工場のほうが導入しやすいと言えます。マスタがExcelで管理されて複数ファイルに分散化しており、情報を統合するのに一苦労するような工場は、導入環境の準備に工数を取られます。
また製品点数や工程数が多く、リスケジュールした結果としての作業数が膨大な数になる工場では、一般的に生産資源に対する制約条件も多く複雑であるため、計画立案担当者が最適と考える生産スケジュールに近づけるのに苦労します。反対に製品点数や工程数も少なく、受注に対する生産能力が十分に確保されている工場では導入しやすいと言えます。
このような生産スケジューラ導入に必要となる最低限の基本情報は、導入前のヒアリングで得られるため、事前に導入プロジェクトの難易度を測ることができます。
(2)プロジェクト開始後に発覚する組織内外の問題
しかし事前に製品情報や工程情報など、スケジューリング上必要な基本情報を貰っていたとしても、プロジェクト開始後に導入の難易度を上げる問題が出現してくるケースがあります。その多くは組織内外上の問題に起因します
スケジューラの導入では営業部、生産管理部、製造部、購買部など社内業務フローで主体となる部署間で、システム運用後の業務の流れについて、コンセンサスが取られている必要があります。今後は受注情報から生成された生産スケジュールが製造指図に落とし込まれ、製造現場で作業が行なわれるが、そのタイミングに間に合うように必要な原材料の購買が行われていくという、一連の流れです。社内の意思決定が個人や部署の政治的意図によって押し切られたり、部署内の要求事項が多く横の連携が取れない縦割り組織の場合、プロジェクト開始後に必ず特定の部門がボトルネックとなります。
また社内業務は社外の顧客や取引先、外注先との関係に影響されますので、サプライチェーンの制約が原因で商慣習が変更されるような環境では、スケジューリングに必要な情報が安定して貰えなかったり、フォーマットが変更されることで、システムの外部インターフェイスを頻繁に改修する必要が出たりします。
このように組織の業務はサプライチェーン全体の中で、モノと情報を流すことで成立していますが、プロジェクト開始前に組織の環境の現状がどうであるかは、明確に文書化されているわけではないため、いざ蓋を開けたら想定外の問題が山積みだったという事態が起こりうるわけです。
(3)運用を回すことを最優先に考える
生産スケジューラに設定するパラメータや制約条件が完璧であったとしても、それらの設定はあくまでも標準値に過ぎず、日々変化していく生産環境では必ず誤差が開いていきます。
理想とするスケジュール結果に極力近づけるという意識は必要ですが、それがどんなに理想的で美しい計画であったとしても、現場が動いてくれなければ意味がありません。
今のスケジュールが完璧であったとしても、次のリスケジュール時には不測の事態に基づいた調整が行われるわけで、スケジューリングに影響を及ぼす要因はリスケジュール前だけでなく後にも発生します。だとすれば、ある程度完成度に見切りを付けて、運用でカバーすることを優先したほうが現実的です。
つまり、自動的に生成されるスケジュールで80点を目指し、残りはマニュアルで調整すると割り切って、現場の運用を回すことを最優先に置くことが重要です。この見切りが付けられず、自動計算で生成される数字の完璧さを求め続けると、いつまでたっても運用は開始されません。
(4)計画は実績と比較することに意味がある
生産スケジューラは標準値であるサイクルタイムベースで積み上げた作業を、パラメータの設定によって制約条件を反映し、並べ替えを行いながら負荷平準化します。時間制約違反を起さない理論上実現可能な計画を立てるシステムであり、導入当初から人間が生産現場の制約条件を100%漏れなく設定することは不可能です。
そうであれば出力された結果をそのまま現場のスケジュールとして適用すべきいう理想論よりも、リスケジュールによっておおよそ納期遅れしないことを確認できたらそれで十分、とするのも人ルの考え方です。後は万が一のために余裕を持たせて何日分かの安全在庫を設定しておくというように、導入開始時はシステムを運用することを最優先にし、慣れていくにつれてパラメータを少しずつ厳し目に調整していくのが現実的なのです。
計画は実績と対比して進捗を確認することに意味があります。例えば1週間分の計画を作成する場合、計画作成時に表示される数量はすべて現在庫数量に基づく予測ベースの数量であり、生産実績が入力されるたびに在庫数量の推移が変化します。次の1週間分の計画作成時には、その時の現在庫数量に基づく予測ベースの数量にリセットされます。
スケジュールを基準に実績の進捗具合を監視し、事前に遅れが出そうなタイミングを見極め挽回策を取る、最低限この繰り返しの運用が出来るまでを運用開始当初は目指すべきだと考えます。最初から分刻みの細かいスケジュール管理を目的とするのではなく、日単位またはシフト単位という、最低限実績入力結果と対比できる最小単位での運用から始めるのが現実的な方法です。